The following article is excerpted from DFMA for Construction: The 4 Perspectives Shifts Enabling Scalable Urban Development, a whitepaper developed by Dassault Systèmes. To read more about off-site prefabrication of construction systems, download the full whitepaper here.
The shift from off-site construction to automated manufacturing
Off-site prefabrication of construction systems is an outcome of AEC culture changes over previous decades. It’s an approach that provides significant benefits over on-site construction. By working in a controlled environment, contractors can improve product quality and generate improvements in worker safety as well as logistics, by providing near-site storage.
Off-site construction is necessary, however it’s not a complete solution to the challenges plaguing project teams today. Simply bringing indoors a collection of parts that must be assembled by siloed disciplines doesn’t transform the building construction process to the degree necessary to address today’s challenges. The next step-function improvement to prefabrication is automation, achieving industrialized construction.
Automated manufacturing practices drive new levels of efficiency in construction. Through automation, contractors realize higher levels of efficiency and quality through controlled process improvements and labor reductions. Factories are vastly more capable of system-and component-traceability through certification. Manufacturers can provide more quality assurances through controlled variables and inspections than even the most skilled human laborers.
There is a broad range of strategies for deploying off-site, automated manufacturing:
- Owned factories: While impractical for most contractors, as they must be fully utilized to justify the investment, large players like Laing O’Rourke and Katerra operate their own automated facilities to fabricate building products.
- Micro- or pop-up factories: These facilities make use of nearby temporary manufacturing space. Small-scale assemblies can leverage local suppliers and subcontractors to efficiently fabricate components near the site.
- Third-party factories: Most of the construction industry depends on supply chain partners to prefabricate building products and systems in supplier-owned facilities.
Regardless of the relationship to a facility, a model-based approach enables the manufacturing process. A manufacturing-grade modeling tool like CATIA communicates design data with precision and integrates directly with machines on any shop floor.
Even for contractors that are not ready to embrace full-scale automation, incremental steps are possible. A model-based design delivers the fabrication-ready data at the right time, right place and right level of detail to support off-site manufacturing.
Case study: Grange University Hospital
Automated manufacturing accelerated on-site assembly and allowed Grange University Hospital to partially open almost a year ahead of schedule in response to COVID-19.
For the Grange University Hospital (GUH) project in Llanfrechfa, Wales, Laing O’Rourke digitally engineered 4,000 components and manufactured them 200 miles offsite in its automated concrete products facility.
Off-site, automated manufacturing offers a 60% improvement in productivity and a 30% improvement in project schedule for Laing O’Rourke’s customers overall. Automation also enabled Laing O’Rourke to reduce its dependency on scarce skilled laborers; 85% of the factory workforce was recruited locally.
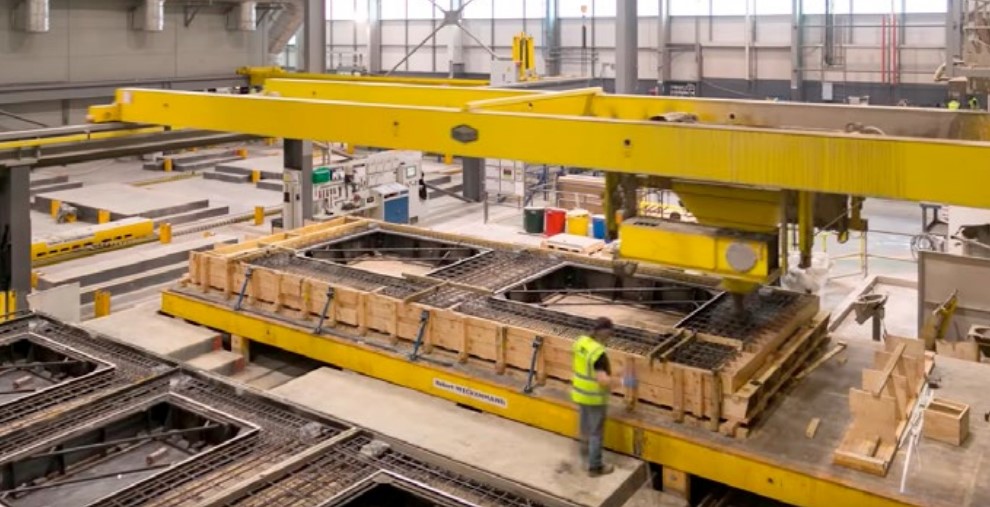
“The benefit of Laing O’Rourke’s approach is there for all to see. The concrete product is manufactured off-site, transported ready-made and of a very high quality,” said Judith Paget, CEO of Aneurin Bevan University Health Board, owner of the new 55,000m3 hospital. “The progress we have seen on-site in a short space of time has been quite remarkable.”
Faced with the COVID-19 pandemic mid-build, the health board asked the project team to fast-track the completion of critical care facilities. They collaborated closely, reprioritized site activities and within just four weeks of their request the health board took possession of 50% of the hospital–almost a year ahead of schedule.
Such flexibility and speed would not have been possible on a traditional build, says Victoria Head, Project Director for Gleeds, the construction consultancy on the project: “We’ve always been proud of the modern methods of construction involved at GUH and the program savings which it offered…but never have the benefits been more apparent than during this crisis.”
Learn more: The Grange University Hospital, Inside Explore Industrial Park
Excerpted from DFMA for Construction: The 4 Perspectives Shifts Enabling Scalable Urban Development, a Dassault Systèmes whitepaper
Download our free whitepaper to learn more.
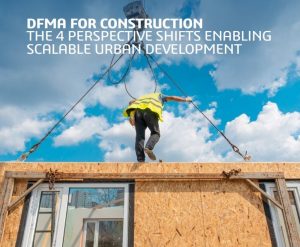
DFMA has the potential to transform the construction industry. This transformation will gain traction as project stakeholders increasingly discover the cost and time savings DFMA offers. Shifting to modular assemblies demands an initial investment in time spent reengineering processes and the tools and equipment needed to support new components. Companies that lead the change will see greater long-term benefits than those who try to catch up on the later side of the adoption curve.
Related links:
Dassault Systèmes Construction, Cities & Territories Industry