The following article is excerpted from DFMA for Construction: The 4 Perspectives Shifts Enabling Scalable Urban Development, a whitepaper developed by Dassault Systèmes. To read more about the design configuration approach, download the full whitepaper here.
A design configuration approach entails setting up an interface for designers to select combinations of pre-defined, standardized options. The configurator then automatically generates detailed manufacturing and assembly instructions. Configurability is made possible through data-driven design automation, which requires continuous integration and simulation capabilities as described above.
In truth, configurability is a more scalable business model than bespoke design services. Rather than designing one-off prototypes, designers can develop extensible building delivery platforms. Instead of engineering every project to order, stakeholders can configure existing components to meet project requirements.
There’s a misconception that configuration leads to limited design creativity. In truth, DfMA begins to meet the growing demand for mass customization. Through configurability, these processes open the door to massive variation and flexibility.
For example, Scania is a major Swedish manufacturer of commercial vehicles. Powered by the 3DEXPERIENCE platform, Scania’s Configurator can automatically design hundreds of different vehicles from just a few modules.
“Scania’s renowned modular system opens up innumerable variants of products and the continuous introduction of design changes,” said Michael Thel, Engineering Director, Scania. “This requires a comprehensive repository of designs that can be joined together in building the applications of the customer’s choice.” Mr. Thel further explained the 3DEXPERIENCE platform was chosen in part for its ability to “enable full traceability and digital continuity from design to manufacturing throughout our unique virtual product development processes.”
While standardization isn’t likely to be practical for an entire building, up to 80 percent of a project could be configurable from predefined options. An effective strategy is to standardize the most repetitive portions of a building, which are often those defined by code.
CASE STUDY
Configurable, modularized “plug-and-play” MCCs eliminated 6 weeks of labor
Laing O’Rourke developed a variety of DfMA objects using SOLIDWORKS and the 3DEXPERIENCE platform and made them available to clients through their DfMA configurator. It presents an easy, accessible interface through which the design team can select different options for standardized DfMA products.
Matt Jenkins, Digital Engineer at Laing O’Rourke, attributes the inspiration to online car configurators. Just as automotive consumers can log on to a website to change the alloys or the color of a car, Laing O’Rourke’s customers and design teams can access a 3D model with dropdown boxes to choose from combinations that have already been digitally engineered.
A configuration approach reduces design time and errors, according to Mr. Jenkins. Instead of redesigning solutions repeatedly, a DfMA configurator hosts the design calculations and all the necessary rules.
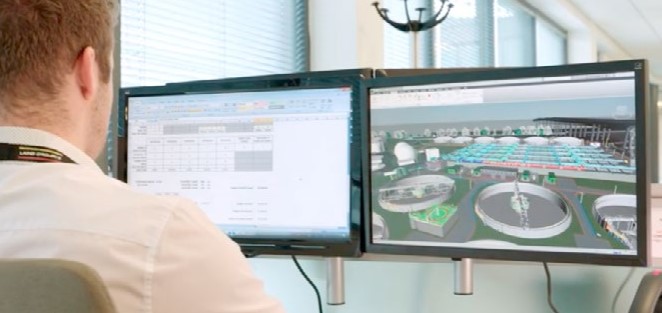
For example, motor control centers (MCCs) were engineered as DfMA products for two major reasons: they are required on all of Laing O’Rourke’s projects, and many disciplines are involved-civil engineering, structural, mechanical, and electrical-making it a complex component that held the promise of major efficiencies if repeatability could be achieved.
Using a dropdown list of options, the design team indicated what foundation they want it placed on, how many elements of each kind are needed within the kiosk, and so on. These design inputs were used to automatically configure the MCC to the project requirements and produce all documentation, risk assessments and method statements.
Remarkably, DfMA configuration reduced the duration of an MCC design process from up to four weeks down to one day, according to Laing O’Rourke.
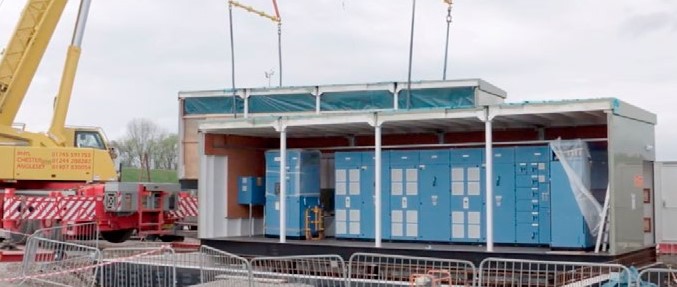
Plus, Laing O’Rourke engineers were able to reduce the number of interfaces on an MCC from thousands to just one. Each unit is “plug-and-play” when it arrives on site, saving approximately six weeks, calculated David Marsh, Project Director.
In addition to the significant time savings, the supplier can test everything off site as built, therefore offering higher quality assurance. Standardization also enables also cost predictability, embedded construction program details, and reliable delivery.
Clearly, DfMA configuration sets a new standard for customers’ expectations of modular components.
Learn more: Digital Engineering and DfMA at Davyhulme
Excerpted from DFMA for Construction: The 4 Perspectives Shifts Enabling Scalable Urban Development, a Dassault Systèmes whitepaper
Download our free whitepaper to learn more.
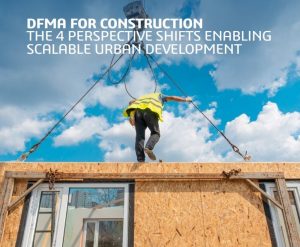
DfMA has the potential to transform the construction industry. This transformation will gain traction as project stakeholders increasingly discover the cost and time savings DfMA offers. Shifting to modular assemblies demands an initial investment in time spent reengineering processes and the tools and equipment needed to support new components. Companies that lead the change will see greater long-term benefits than those who try to catch up on the later side of the adoption curve.
Related links:
Dassault Systèmes Construction, Cities & Territories Industry