How are students preparing for the future of AEC?
As the largest Industry in the world, the Architecture, Engineering & Construction (AEC) industry accounts for approximately $13 trillion of annual expenditure and is responsible for 43 to 48% of the global greenhouse gas emissions that fuel climate change. This heavy toll is due to the construction process, but even more so… to their massive operating costs.
Added to growing population, rapid urbanization and explosive demand especially in the global South, those figures make it urgent to answer a need for more efficient, lower carbon, on time and on budget construction that does not compromise on quality.
Why wouldn’t we build houses, condos or flats just as we build cars and airplanes?
What is modular construction?
A possible turnkey solution seems to be modular construction, which involves the “productization” of the AEC industry, i.e. moving the first stages of the production process from the site to the factory using parametrically intelligent and adaptable parts, ready for assembly. It’s a new way of thinking about building that leverages technology to win on several fronts, from flexibility to sustainability to productivity.
Yet, as in many large and complex industries, the AEC industry faces a lot of resistance to change and still shows the smallest technology adoption. But the good news is: the game is changing… and it starts in the labs and studios of the university!
David Gerber is a professor of practice in civil and environmental engineering and architecture at USC’s Sonny Astani Department of Civil & Environmental Engineering (CEE), and is the sole AEC 3DEXPERIENCE Edu Center of Excellence. His work is entirely focussed on using technology to support sustainable design, architecture, engineering, construction and entrepreneurship.
“Civil and environmental engineers, as well as architects, will play a crucial role in shaping the future of our planet, leveraging emerging technologies to address the pressing challenges of the built world and create sustainable solutions.” D.Gerber
A new way of building (enabled by virtual twins)
As easy as assembling toy construction blocks?
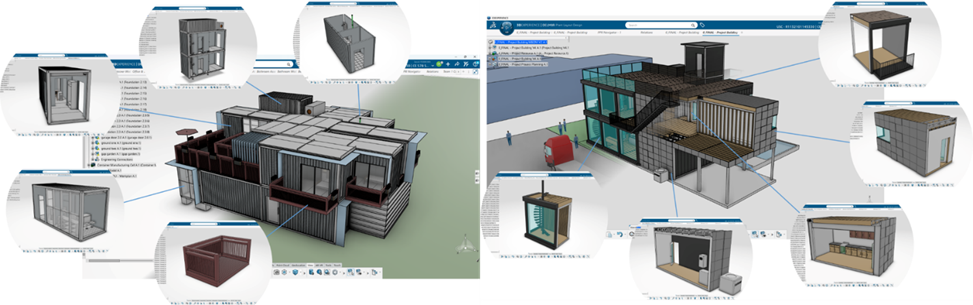
The focus on modular construction[1] represents a profound opportunity for change for the AEC industry. By moving from a fragmented, entirely on-site approach to a modular, repeatable, factory-oriented approach, “we’re creating a whole new way of thinking and working for all stakeholders – a way that isn’t the norm in the AEC industry today, but is in productizable industries”, Gerber says.
“We’ve been very inefficient for 100 years! Not enough manpower, extremely wasteful processes, always over time and over budget… Why? Because we are not embracing technology, and the benefits of a productization and off-site mindset!” D.Gerber
Breaking down the modular approach
The modular approach encourages thinking of buildings not as one-off projects but as sustainable, potentially and partially reproducible products. Pre-building blocks in factories – from pre-cast walls to window frames to underfloor wiring – eliminates many on-site delays caused by weather for example, and ensures higher consistency in assembly, for more precise scheduling, cost control, and higher quality.
“Although buildings cannot be productized to the level of a car”, says Gerber, “It’s already a huge step forward in gaining efficiency.” Gerber’s professional experience with major designers such as Zaha Hadid Architects, Gehry Technologies and ARUP is proof that even a unique creation can emerge from using advanced digital design, engineering, and fabrication methods.
Indeed, modularization doesn’t mean standardization! A module is actually a smart, adaptive component that is able to configure itself to different cases, to slightly change, because it’s parametrically modelled, first virtually and then in the real world.

This shift towards modular design and construction is thus highly supported by cloud innovation platforms and virtual twins, which enable high-fidelity 3D modeling of those blocks and their smart integration at all stages — design, engineering, manufacturing, and assembly — both off-site and on-site. “Virtual twins create a shared data repository that promotes real-time collaboration, testing, and feedback, ensuring that projects’ data and integrations evolve dynamically and sustainably throughout time and space and people”, adds Gerber.
“The 3DEXPERIENCE platform enables the precision of product manufacturing, where a centralized system helps you and your teammates manage the entire lifecycle, from idea to design and production.” D.Gerber
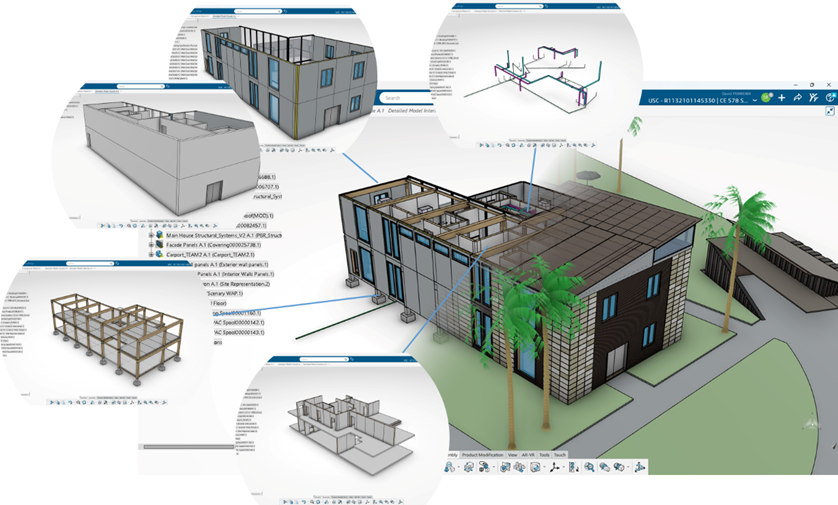
➡️ Discover all aspects of productization by listening to our Disruptors Unleashed podcast.
Moving forward, even if it looks like the holy grail, productization of the industry will require a whole new mindset and a new major competency: the art of integrating design and engineering with that of manufacturing (both in real and virtual), which represents a new emphasis for all the AEC stakeholders.
And Gerber’s focus is indeed to prepare students for this new paradigm!
Skills needed! A new way of teaching and learning.
Modular construction is hence a technological and methodological shift that requires new tools, new methods, and new skills. These have to be at the heart of university curricula, to make students future-ready for the challenges of the industry.
“We’re not educating people the right way! We have to teach students to think beyond the status quo, and to challenge the future through the lens of data, technology, integrations, and sustainability in order to build the AEC industry of tomorrow.” D.Gerber
Preparing students for the future of AEC
Prof. Gerber’s teaching philosophy, as part of the 3DEXPERIENCE Edu Center of Excellence are indeed very practical, and entirely built around modular, and industrialized construction with four main pillars of knowledge: 1. DATA, 2. TECHNOLOGIES, 3. INTEGRATION, and 4. SUSTAINABILITY. Through this lens, he is preparing the next generation of built environment professionals!
Using the 3DEXPERIENCE platform in class, for his students to be in real-work conditions, he drives them to apply this new way of “building” to every project, integrating both the modeling of the EBOM within CATIA (Engineering Bill of Materials) and MBOM within DELMIA (Manufacturing Bill of Materials), all in one place and connected for a full value chain approach.
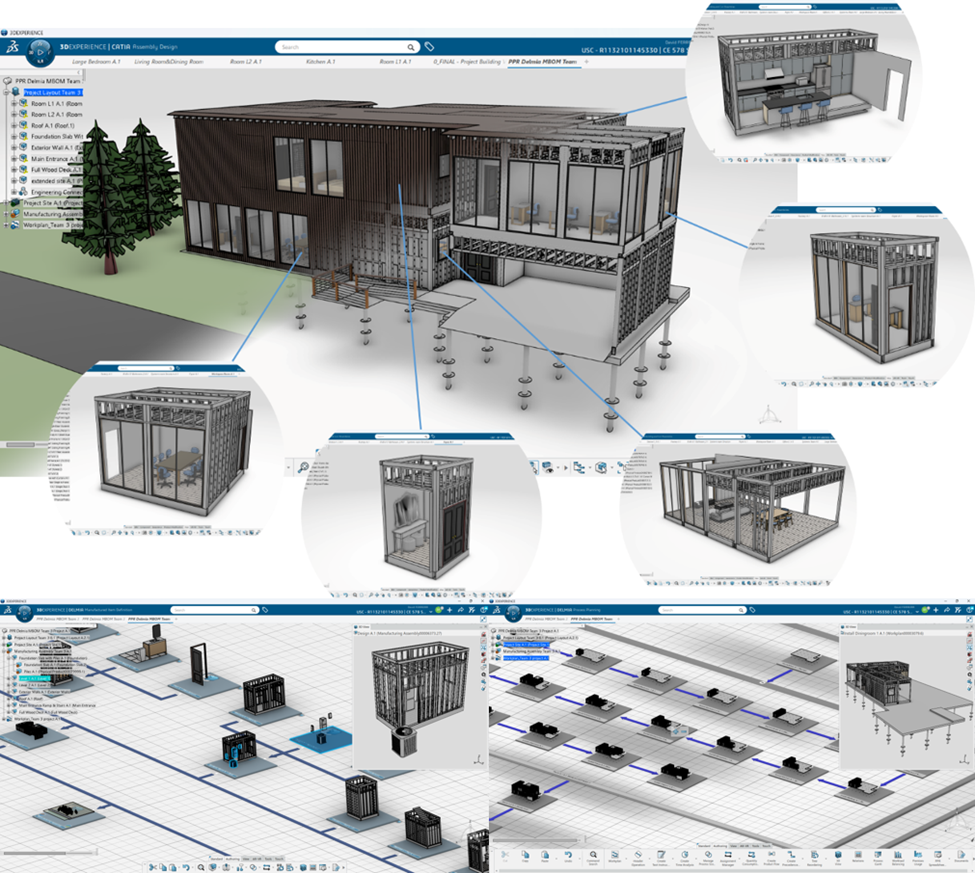
According to Gerber, architecture and engineering students in the AEC must indeed develop a range of new skills that go beyond their original and technical expertise.
- First, communication skills are essential. “Future leaders need to not only calculate and design but also effectively present, lead teams, and facilitate collaboration across disciplines”, Gerber says.
- Second, students must master modeling and simulation, allowing them to visualize and test designs in real-time.
- Third, process modeling is a critical skill borrowed from product and manufacturing industries like Automotive and Aerospace, where architects and engineers must consider how their designs anticipate constraints and integrate with manufacturing processes.
- Finally, data management is key. Students must be proficient in handling and interpreting data, integrating both software and hardware tools, and working seamlessly with experts across different fields.
This is only with such a holistic understanding of communication, modeling and process modeling, as well as data integration that students will be ready for their upcoming work adventure: create sustainable, efficient, and innovative projects in the modular construction era!
A learning method that would gain to be replicated across academics to drive the future of AEC.
🤫 Pssst ;) 3DEXPERIENCE Edu can help you with that!