By 2050, there will be nearly 10 billion people in the world. These people must be housed; and this housing must be safe, affordable, and increasingly – sustainable. A whole new generation of innovative construction approaches are needed.
This was the mission that lay at the heart of our Building Tomorrow project, which you can explore in full here. Across the project, Dassault Systèmes teams sought to demonstrate how virtual solutions can allow us to totally transform how we collaborate on, design, and operate buildings with carbon neutrality in mind – even the very biggest structures.
Like the Eiffel Tower, for example.
Innovation: a legacy from Gustave Eiffel
When it was first built, the Eiffel Tower was seen as a global marvel, not only for its eye-catching design but also for demonstrating what could be achieved with state-of-the-art manufacturing techniques and technologies. For example, rivet holes on the structural beams were precision-drilled in a factory offsite, with the actual riveting then done on-site to maximize quality and efficiency.
The same spirit of innovation has been applied in the new tower project, which makes use of a technique called productization. This means that rather than being seen as a single entity, the tower is conceived as a modular building – one composed of multi-trade, integration-ready prefabricated modules. These can be manufactured in micro-factories and then installed on-site, requiring fewer trade workers during the assembly process.
Rather than designing the prefabricated modules from scratch, the various elements of the building are selected from an existing library of virtual construction bricks. These modules have been designed based off established data and knowledge from general contractors, specialty contactors, and building product manufacturers.
General contractors serve as the prime integrators to procure and install modularized systems for building projects. By using a virtual construction twin, a construction project team can model and test different building designs, utilizing different combinations of virtual construction bricks.
This is the power of productization. Inspired by the modular approach that has long been used in other manufacturing sectors, like automotive manufacturing, it helps answer the growing demands of personalization and regionalization, by leveraging tried-and-tested libraries of elements. These can then be used in future modular construction projects.
This productization approach also enables designers to methodically consider manufacturing and logistics constraints, and then make informed decisions that support truly sustainable and personalized construction approaches. It also greatly reduces the amount of construction work done onsite, helping developers navigate the challenges of the global skilled labor shortage, and mitigate safety risks.
A key benefit of productization is traceability – by being able to trace each module as it is produced, transported, and assembled, manufacturers can monitor the environmental impact across a building’s lifecycle, helping minimize things like carbon footprints. This includes being able to disassemble and reuse each module elsewhere as needed. By doing so, project waste is greatly reduced at every stage, from manufacturing and construction, to operations, and ultimately dismantling.
Throughout the process, the 3DEXPERIENCE® platform is a critical element in powering productization. Virtual twin solutions enable teams to effectively manage design models, product lines, drawings and documentation, and all associated production data. All stakeholders can easily work together thanks to effective collaboration tools.
With productization, buildings are no longer one-off projects – a new, modular approach allows for both building elements knowledge and know-how to be reused across projects. This creates substantial savings in time and cost, improves quality assurance, and helps realize truly sustainable buildings.
How to adopt productization?
Click below to learn how we applied productization to our tower with the 3DEXPERIENCE® platform. In the interviews below, Nicolas Senemaud and I, detail as team members on the Building Tomorrow program, the value productization can bring to your next project, and how it can benefit the Infrastructure & Cities sector as a whole.
The pressure on the construction industry to find new ways to meet the increasing needs of an increasing number of people in less time and with fewer resources grows unabated.
The only answer is to rethink how we design and construct buildings. Productization is a new paradigm for the Infrastructure & Cities sector. It is a powerful way for construction companies to innovate around their approach to projects, reducing the risk of design and construction errors while allowing for greater agility, customization, and sustainability.
Discover more about the Building Tomorrow program here:
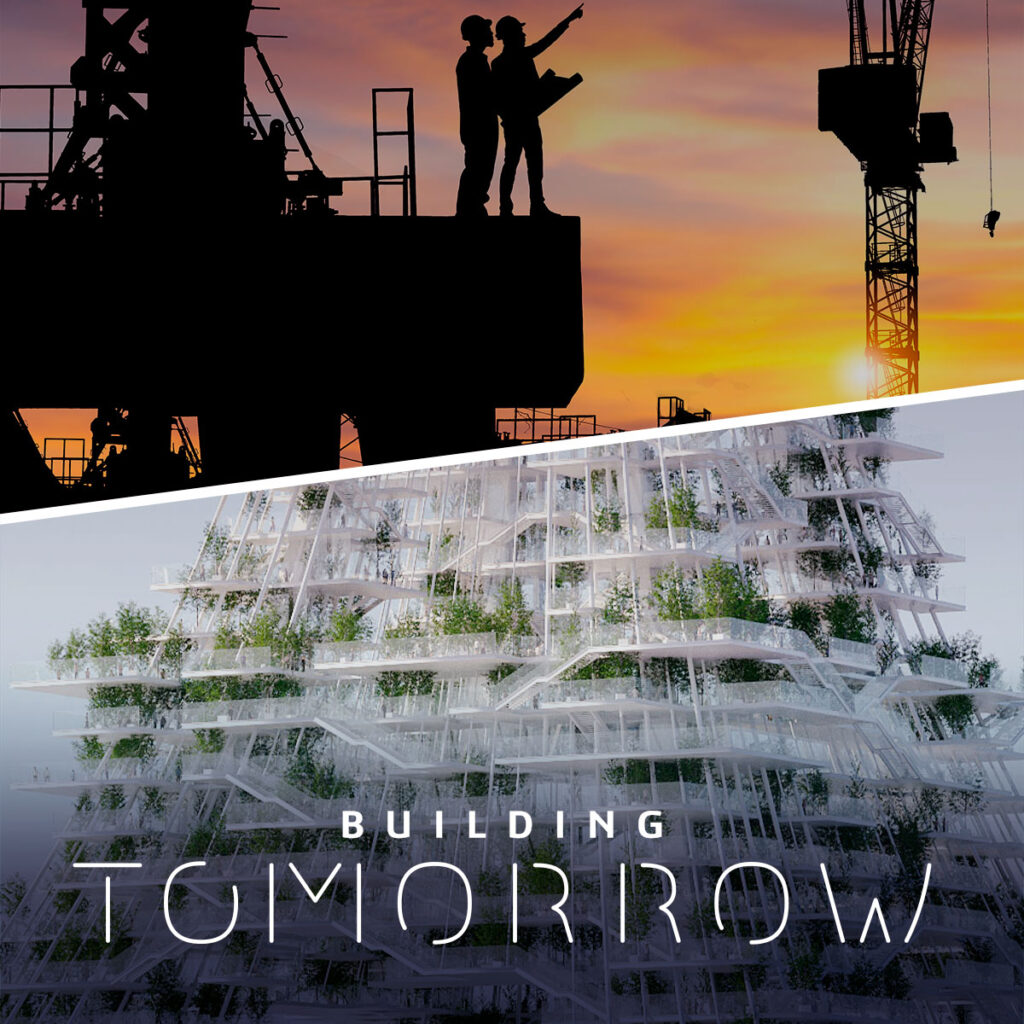