Prashanth Mysore, DELMIA Strategic Business Development Senior Director, Dassault Systèmes
Traditional manufacturing work has turned unappealing to the newer generation of workers compared to highly digitalized industries. At the same time, the challenge to recruit and retain these workers has never been higher than today as supply chain disruptions and geopolitical realities force governments worldwide to prioritize local manufacturing and the development of sovereign capabilities.
Gen Z and millennial workers often avoid the manufacturing industry or leave soon after joining for more digitalized sectors, taking their skills with them due to the outdated way of working. Fast-paced technological changes also necessitate engaging and enjoyable work platforms.
Companies in the Asia Pacific region are trying to catch up with the evolving employee preferences to stay competitive in the race for indigenous strategic manufacturing capabilities development. According to a survey by Mercer, in 57% of companies in the region are already focusing on enhancing the employee experience to retain top talent while close to half are redesigning processes around people’s skills. The time to rectify the manpower shortage by digitalizing the employee experience is now or the development of sovereign manufacturing capabilities could be jeopardized.
How virtual twins help retain, train and create a smarter workforce
Amid retention challenges, reskilling and upskilling through knowledge management and employee safety have become top priorities after COVID and the current platforms used in manufacturing are being upgraded to facilitate smarter workforce and smart manufacturing.
Virtual twin technologies provide the environment to retain and continuously upgrade the skills of the current and newer generation of workers in manufacturing while applying smart factory paradigms. They provide a human-centric approach to upskill and digitally empower the workforce.
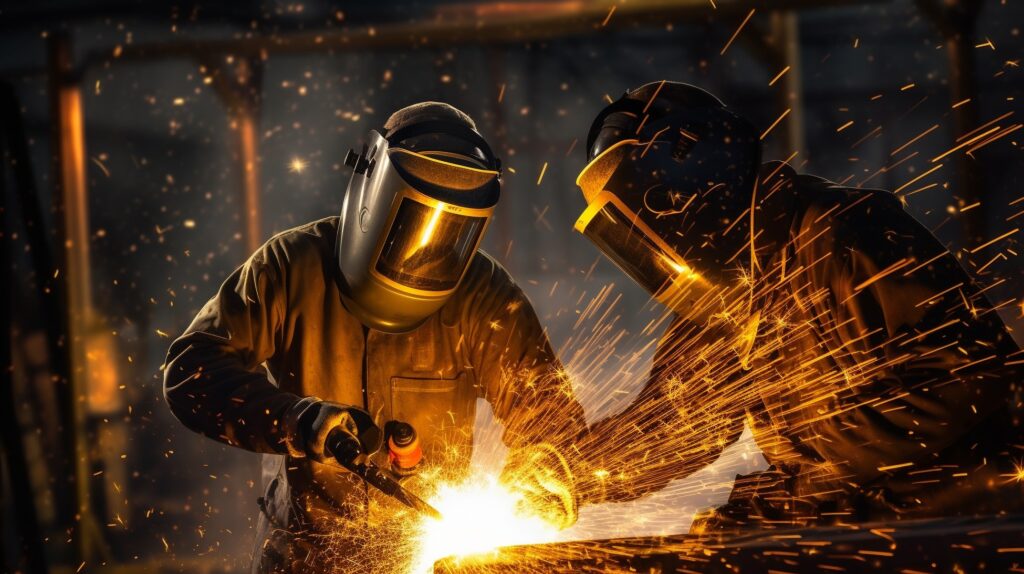
Helping build the workforce of the future and developing skills relevant to the future is a task with a moving target. Dassault Systèmes keeps updating its strategies to meet the needs of the market. The ‘future of industrial work framework’ is based on three axes with overlapping areas: leadership, total employee experience, and connected workforce.
Commitment, change management, establishment of the recruitment culture, performance management, succession planning, talent management, and knowledge management are the prerogative of the leadership. Dassault Systèmes’ connected 3DEXPERIENCE platform helps the management take care of all these factors in an integrated and dynamic manner using virtual twin technologies.
It helps capture experienced employees’ skills for knowledge management while enabling job flexibility as part of the employee experience. The 3DEXPERIENCE platform-based technologies such as augmented reality and mixed reality that are backed by artificial intelligence make work more enjoyable and connected with data-driven insights for decision automation. The platform also helps introduce a complete employee experience, and an employee-centric way of working to make work more meaningful.
People-centricity the crux of the 3DEXPERIENCE platform
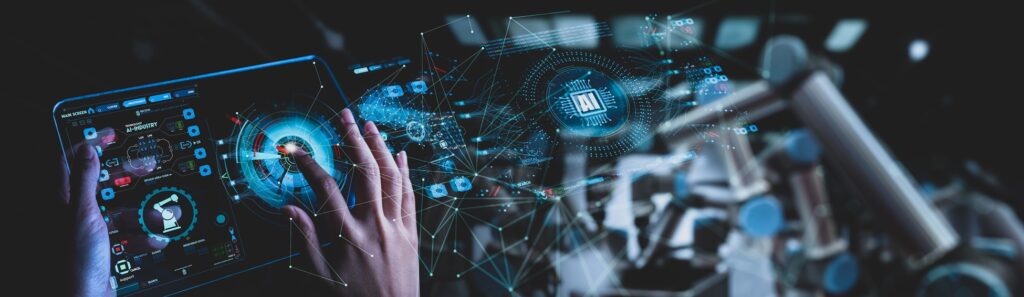
With regard to creating a smart and connected workforce, it is the people centricity of the platform that comes to the fore. The 3DEXPERIENCE platform integrates best practices and ensures that the latest technologies are being used by the workforce at the manufacturing workplace. This helps enable safety while ensuring that the work processes are enjoyable for the new generation workforce.
The platform uses digital technologies to connect workers to operational systems such as those for tracking of manpower in terms of safety and materials while updating the knowledge of the workers through AI-based KPI charts and predictive management tools. These features help the workers immerse themselves in the concept of smart and connected workforce.
With regard to the applications used on the 3DEXPERIENCE platform, it is collaborative in nature with people, process, technology and data connected on a flexible IT system. In addition, the platform can leverage IoT applications that analyze data from sensors as well as AR applications to enhance the skills of the workers.
Dassault Systèmes’ 3DEXPERIENCE platform supports predictive management on the factory floor which is key to the smart factory experience. The prediction of potential failures are intimated to the workers using analytics to empower them to take action before mishaps occur.
In terms of operational technology, Dassault Systèmes works with multiple partners and clients for enabling the introduction of robots and cobots into the manufacturing shopfloor through the platform. Cobots or collaborative robots help workers and robots work in conjunction with the enablement done on the platform. In addition, it empowers the workforce to work with autonomous vehicles in places such as assembly shops and hazardous maintenance sites.
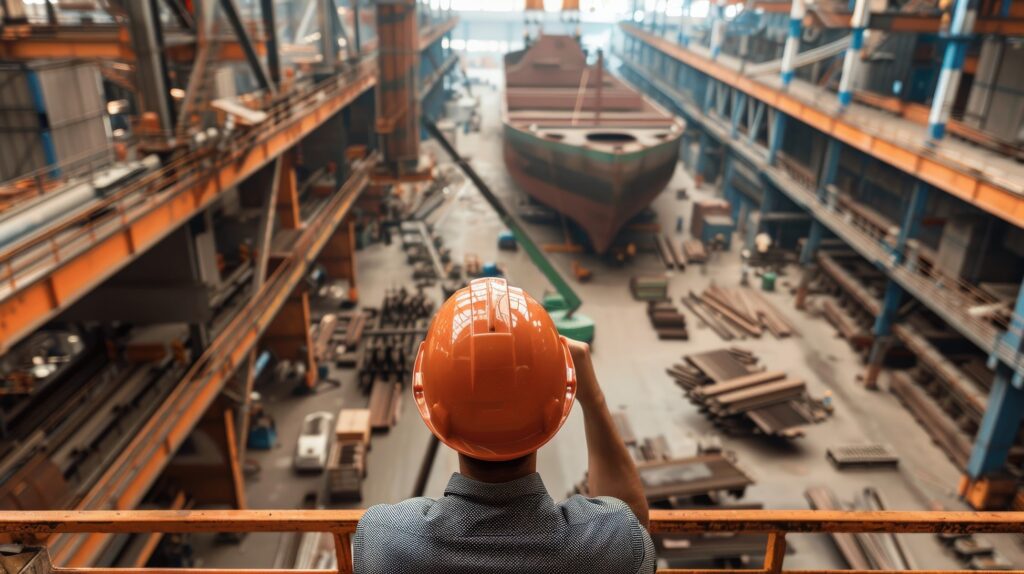
As far as work area connected devices are concerned, workers and the management can automate sensors, geofencing, proximity beacons and local clouds using the platform to make work more efficient. Wearable technology such as smart glasses enabled with AR and VR are extensively used on the platform along with assisted reality. The platform also enables video analytics for on-the-job training and predictive analytics for equipment maintenance management software.
The smart factory is IoT and sensor-driven and the workers are trained to work on the smart factory system with the knowledge to extract information from the decision support and automation systems in compliance with Industry 5.0 principles.
3DEXPERIENCE platform enables seamless collaboration
The 3DEXPERIENCE platform’s key benefit is the seamless collaboration – across technology, process and people – while cutting through siloes and empowering workers with integrated data. The platform is highly data-driven with high level data analytics capabilities embedded into it that helps the workforce achieve operational efficiency and excellence.
With regard to processes, along with the smart factory approach the 3DEXPERIENCE platform supports industry 4.0 as well as industry 5.0 frameworks. In terms of technology, the virtual twin supports five standard business processes.
- Modeling of the business processes: Modeling of factories, supply chains, warehouses, airports, rail infrastructure and shipyards among others
- Collaboration: Once something is modeled, the platform enables seamless collaboration within the organization and with external stakeholders as well – for instance, it integrates the academia, industry, and government stakeholders on a single platform
- Optimization: From optimization of manpower, scheduling to delivery of material and logistics and supply chain planning and optimization software, Dassault Systèmes’ best-in-class virtual twin technology supports the optimization efforts of companies in all industries
- Execution management: Execution is where the people factor comes prominently into the picture enabling seamless integration between the work processes of production managers, factory workers, and manufacturing quality control managers, robotics engineers, warehouse workers and production engineers among others.
- Innovation for sustainability: The process and technology help the people imbibe sustainability values intuitively
Why the 3DEXPERIENCE platform for manufacturing?
Globally, smart and connected workforce initiatives are growing rapidly, with digital natives accelerating the adoption of digital tools and platforms. Users now seek comprehensive solutions that transform work processes rather than individual tools, with solutions that accommodate business changes and evolving challenges. Technology is shifting to a system-of-systems approach to empower employees, favoring scalable, cross-functional solutions with open and interoperable technology. All of these factors point to the need of deploying technologies such as virtual twins and the 3DEXPERIENCE platform in the pursuit of empowering the new generation of workers to find manufacturing work meaningful, enjoyable and fulfilling.