Aerospace historically has been one of the world’s most powerful engines of technology innovation, fundamentally influencing the way in which people everywhere live, work, travel, communicate, and compete. The Internet, GPS navigation, and life-saving diagnostic and imaging medical equipment are just a few of the more game-changing innovations for which the industry is directly responsible.
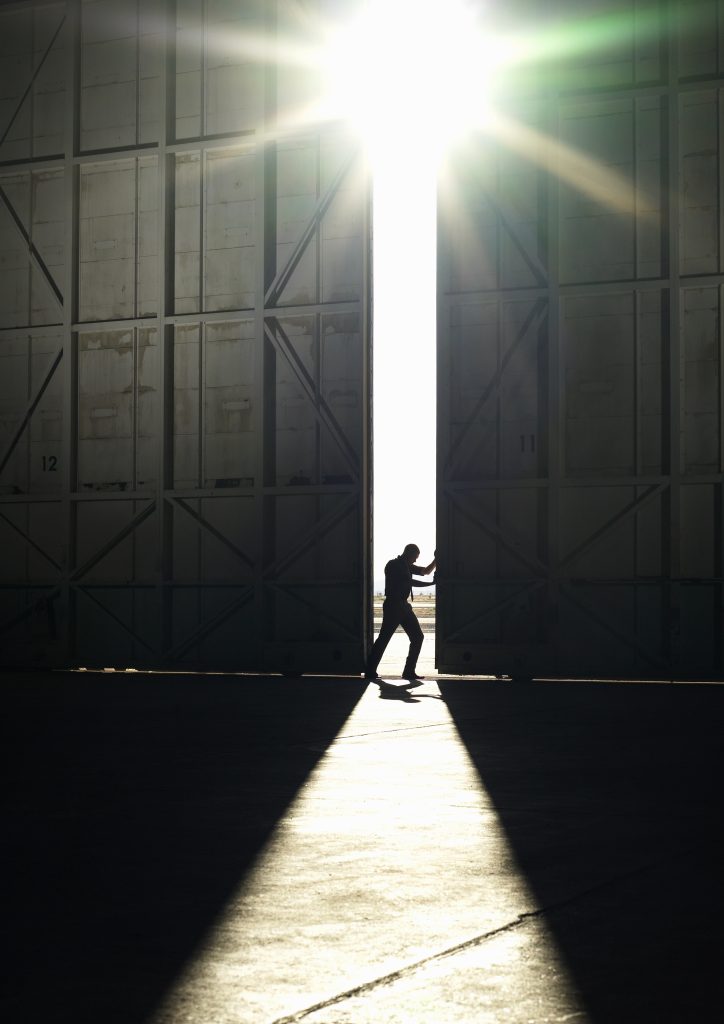
But not all aerospace-connected advances rise to this level. A plethora of other innovative technologies were simply the result of meeting the demand for more stringent performance expectations wholly unrelated to aerospace. For example, when Woods Hole Oceanographic Institution designed its next-generation vehicle for extreme deep-sea human exploration, it turned to a small Wisconsin supplier of forgings used in aerospace applications. Ladish Co., developed an innovative process for forging a two-piece vessel made of titanium able to ensure higher structural integrity of the spherical structure at extreme ocean depths.
It’s hard to imagine these innovations—big and small—occurred years before the digital and smart technologies came into play. Twenty-first century technology such as; artificial intelligence, machine learning, digital models, simulation, the Industrial Internet of Things, data analytics, virtual and augmented reality, generative design, advanced materials science, additive manufacturing software, cloud computing, and more are transforming product development and manufacturing. (Read more here).
Harder still is imagining how much more innovative the industry may become as more manufacturers—already accustomed to producing highly engineered, highly dependable equipment—leverage these digital tools using an integrated platform to optimize the tools’ potential to accelerate the innovation process.
At the very least, it would seem reasonable to expect manufacturers’ rate of innovation to increase, to sustain this higher rate, and even generate production-ready innovation through virtual testing and verification of products designs earlier at less cost and greater speed. Currently, testing represents about 25 percent of a product-development program’s cost and time, and nearly a quarter of tests are unplanned.

There is no shortage of examples of how companies already exploit these digital technologies.
One of the most versatile of these tools, additive manufacturing (AM) or 3D printing, offer the flexibility to build products designed with novel geometries that would be difficult or impossible to achieve through traditional manufacturing. (Discover why here).
When Airbus was producing A320 nacelle hinge brackets, it used direct metal laser sintering to build an optimized design that reduced the part’s weight by 64 percent while maintaining its strength and performance. For its part, GE Aviation uses AM to produce parts designed to deliver maximum performance in the form of optimized airflow for higher efficiency.
In a third example, Chicago-based Sciaky, specializing in electron beam additive manufacting (EBAM) technology, has been working with Airbus, Lockheed Martin, and other aerospace customers on qualifying materials, processes and parts using their own EBAM machines. Work completed thus far has shown EBAM can produce components that meet or exceed the properties of forged parts. Printing versus forging these components avoids long lead times and the waste of expensive metal involved in machining finished parts from forgings.
New additive manufacturing techniques in development will allow the technology to print parts with multiple materials to optimize properties in different segments—as in the use of iron-nickel alloy for its thermal expansion characteristics in one segment and chrome alloy in another segment where corrosion resistance is needed.
Advanced simulation, digital twins, and artificial intelligence are other digital technologies that are expected to profoundly change the manufacturing and the innovation process.
For example, using AI software and the computing power of the cloud, generative design allows engineers to create multiple options by simply defining their design problem—inputting requirements, limitations, and other qualities, such as the total cost of materials, into a software program. As the designer winnows the choices, the program helps iterate even better options. Airbus used this tool to redesign an A320 interior partition with a configuration that was 45 percent lighter than the previous one.
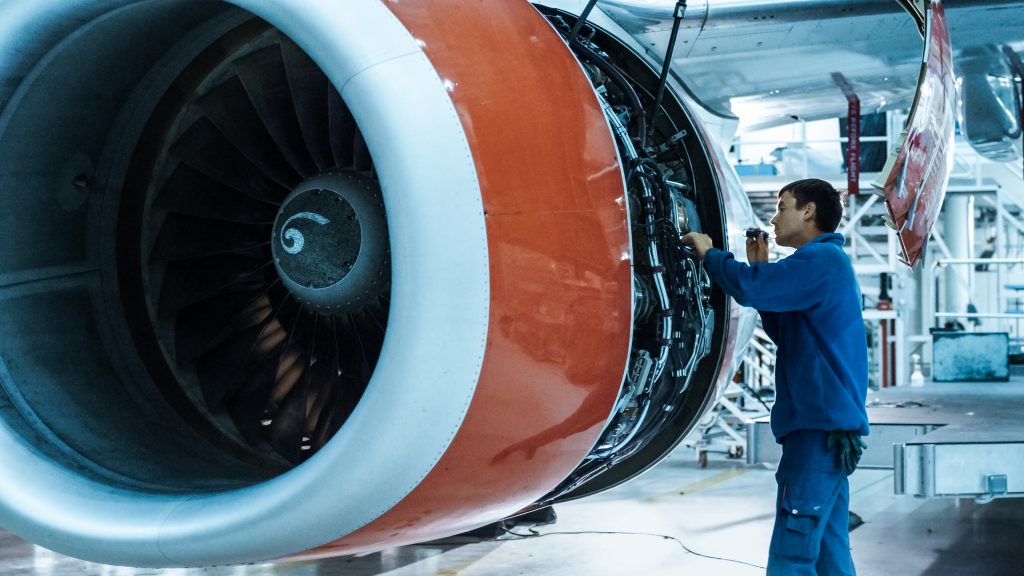
None of these examples represent great leaps in technology innovation. Nonetheless, they are advances made possible by a digital tool that can help aerospace manufacturers produce high-quality, innovative parts at less cost.
A new industrial revolution that will transform production value chains and business models is dawning. However, there’s something to be said for reminding aerospace industry professionals that market dominance is not guaranteed, any more than success is a foregone conclusion.
The barriers to entry in aerospace continue to come down; start-ups threaten to disrupt various market segments, while competition from regional competitors pose other challenges to established players. Moreover, many companies remain reluctant to embrace digital transformation and commit to the digital tools that have the potential to accelerate the innovation process. To take advantage of these opportunities, great digital leadership – starting with a compelling transformative digital vision, is the first step.