To learn more about Stefanie Feih and her work, click here.
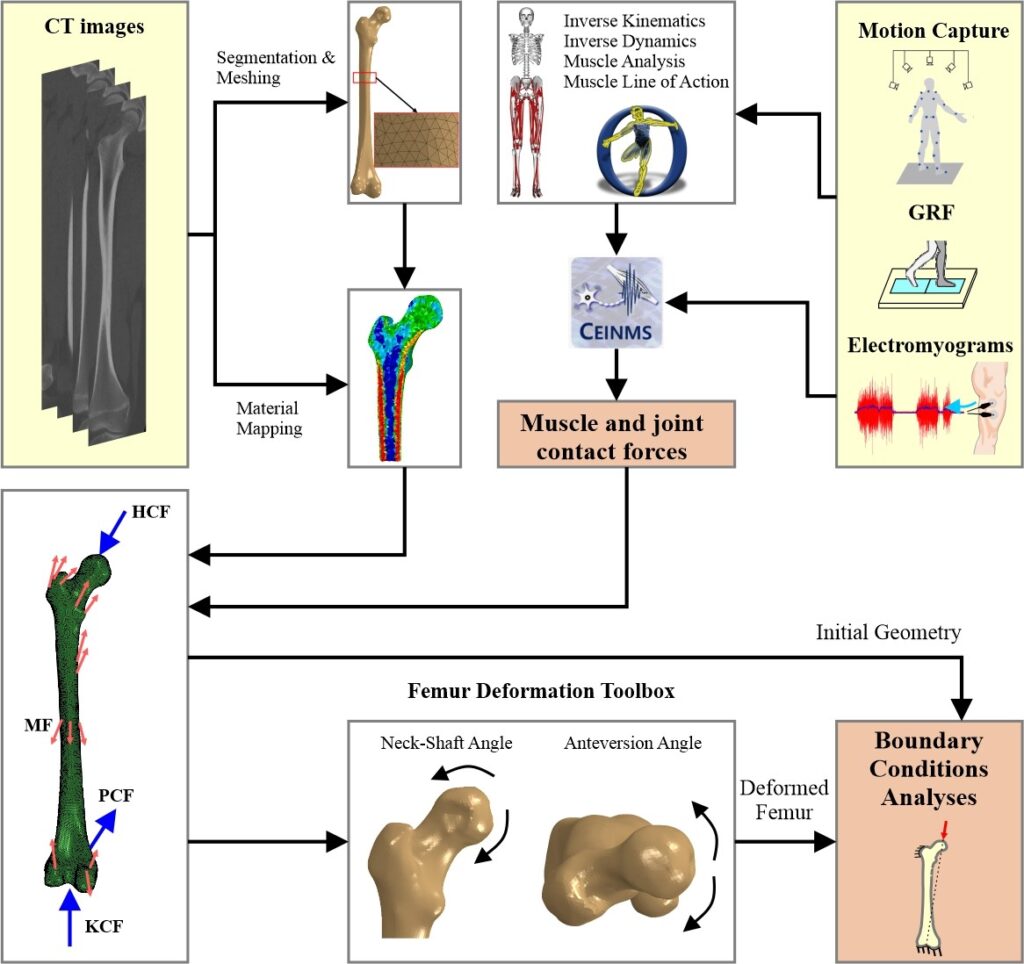
Introduction
The long-term success of orthopedic surgical interventions relies heavily on the mechanical integrity of both implants and host tissues. Failure or shifting of implants from their intended position within the bone can result in prolonged recovery times, necessitate revision surgery, and impact a patient’s overall quality of life. Consequently, numerical simulations, or so-called digital twins, are becoming increasingly crucial for informed surgical decision-making.
In this blog post, we present a workflow for patient-specific femur simulation that may be used for the assessment of orthopedic surgeries. Specifically, our digital twin employs a simulation workflow to create the required input data for the finite element analysis (FEA) to be performed in Dassault Systèmes SIMULIA Abaqus, to determine physiologically plausible localized stresses and strains in an isolated femur system. The patient-specific workflow may improve predictions of implant and host tissue mechanics, which will ultimately allow us to minimize the surgical risks due to improved implant selection, design, and placement during the surgical assessment planning phase.
How is numerical simulation used in the medical industry?
Medical regulation authorities, such as the US Food and Drug Administration (FDA), are currently creating and updating guidance documents to promote consistency, increase confidence and improve result interpretation when using computational modelling and simulation (CM&S) approaches, or digital twins, for medical device submissions. While many research groups are promoting numerical simulation approaches and outcomes, it is the authors’ opinion that the coordinated efforts of regulation, verification and validation of CM&S in the biomedical field are inferior in comparison to other engineering industry sectors, such as aerospace and automotive. The best approaches for orthopaedic biomedical industry CM&S remain to be carefully validated, including, but not limited to:
- Best practice in developing and applying patient-specific neuromusculoskeletal models to estimate muscle and joint contact forces (points/areas of application, magnitudes and directions) for use as tissue loading conditions;
- Constraining boundary condition (displacement and rotation) application and validation to ensure realistic deformations and stresses for isolated tissues and their complex assemblies;
- Mesh convergence studies to validate commonly employed tetrahedral meshing strategies for complex geometries;
- Contact validation studies for assemblies with complex geometry and significant differences in material stiffness properties; and
- Solution algorithm validation of implicit versus explicit solution schemes in the case of highly nonlinear contact and material properties.
Rigorous development of benchmarking case studies and established training pathways are required for the industry sector.
How does simulation help in medical device design?
The use and evaluation of patient-specific data is crucial in the medical technology sector. Nevertheless, the tailoring of medical implants to specific patient characteristics remains in its infancy, with the importance of considering and incorporating individual patient musculoskeletal anatomy, physiology, and function still poorly understood.
A systematic evaluation of a range of patient-specific characteristics, including implant choices during surgery, can help to identify key parameters for surgery success. Our integrated simulation workflow utilizes external and internal biomechanics informed by full gait analysis, motion capture, EMG, and X-ray computed tomography data to estimate joint contact and muscle force input via inverse kinematics and inverse dynamics. The simulation highlights the differences of isolated bone stresses and deformations from femur FEA (based on patient-specific femur geometry and best practice joint and muscle force input) under different constraining boundary condition approaches. Importantly, we highlight the impact of the constraining boundary condition selection in the isolated tissue (femur) system. We consider inertia relief to be the best approach for solving such an isolated dynamic system problem, which is commonly interpreted as a static load equilibrium problem. By benchmarking our results against the inertia relief method, we establish best boundary condition approaches for both normal and pathological femur systems to avoid unrealistic over- and under-constraining of the isolated part. We most importantly also show that many boundary condition approaches commonly utilized in the existing literature do not provide realistic results but are nevertheless considered adequate and accepted by the community.
Conclusions
Our outcomes and comparisons highlight opportunities, but also challenges to be overcome, for orthopedic devices simulations (i.e., digital twins) in the biomedical industry. While commercial software providers such as Dassault Systèmes SIMULIA have over the past years provided major solution improvements for the biomedical industry via improved contact algorithms and more accurate tetrahedral element stress solutions, more work remains to establish scientific community consensus for best practice as evident from the divergent approaches in published studies.
The following authors also contributed to this post:
is an internationally recognized Professor of Biomechanical Engineering at Griffith University, Australia, ranking among the top 0.2% of published scientists worldwide. David’s research focuses on biomechanics, biophysics, and sports medicine, with a strong track record of publications, PhD supervisions, and attracting significant research funding. Collaborating with hospitals and industry partners, his work leverages cutting-edge technology like AI and digital twins to develop innovative medical diagnostics, devices, and personalized treatments.
Emmanuel Eghan-Acquah holds a bachelor’s and master’s degree in Biomedical Engineering and has over five years of experience as an R&D engineer specialising in orthopaedic implant design, testing, and manufacturing. Emmanuel is nearing the completion of his PhD at the Griffith Centre of Biomedical and Rehabilitation Engineering (GCORE) at Griffith University, Australia. His doctoral research focuses on paediatric biomechanics and optimising post-surgical biomechanical outcomes following proximal femoral osteotomy through personalised neuromusculoskeletal finite element analysis.
Alireza Y. Bavil is a Biomedical Engineer specializing in biomechanics and currently a PhD candidate in the field. Alireza’s expertise in biomechanics, and in particular clinical and orthopaedic applications, is complemented by a solid foundation in practical and theoretical knowledge in mechanical engineering, providing a unique perspective on the challenges and innovations within the field. As a PhD candidate, he continues his research in biomedical engineering, striving to connect intricate biomechanical concepts with real-world clinical applications.
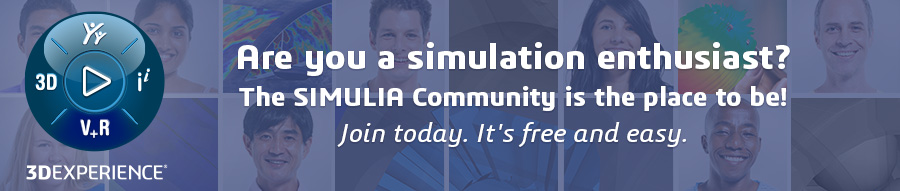
Interested in the latest in simulation? Looking for advice and best practices? Want to discuss simulation with fellow users and Dassault Systèmes experts? The SIMULIA Community is the place to find the latest resources for SIMULIA software and to collaborate with other users. The key that unlocks the door of innovative thinking and knowledge building, the SIMULIA Community provides you with the tools you need to expand your knowledge, whenever and wherever.