Vehicle-Tire Simulation: why do it? As we know, vehicles are quite complex and require a significant amount of design, engineering and testing to get right. State-of-the-Art development methodologies have adopted the Verification and Validation construct. Validation is expressed by the query “Are you building the right thing?” and Verification by “Are you building it right?” For vehicle design, one way to accelerate the development process, and reduce late-stage design changes, is to execute system level virtual testing (Validation) early in the design process. System Level Virtual Testing is fully realized once a reasonably accurate reduced order tire model is generated. One of the primary challenges in realizing this has always been getting a detailed virtual tire early in the vehicle design process. Essentially, this can come from two (2) sources. The diagram below details the source and three (3) potential workflows derived therein. For the purposes of this article, we will focus on Workflow-1.
The following workflows can be categorized into three (3) generalized processes:
- Co-Simulation with reduced DOF tire model to predict, real time, the response of the vehicle
- Co-Simulation with a fully-detailed tire model to predict the detailed response of vehicle sub-systems
- NVH simulation for Full-Vehicle Durability prediction
As you can see, the Detailed Tire Model can come from either the Tire OE, or a Reverse Tire Engineering activity. Again, we will focus on Workflow-1, which is System Level Virtual Testing.
For both sources (Reverse Tire Engineering or Tire OE), Tire modeling in Abaqus has matured to the point that physical testing is not required to calibrate the reduced order model. See https://www.youtube.com/watch?v=lAKymk1O8YM&feature=youtu.be for details. Therefore, if requested, the Tire OE should be able to supply virtual test results for calibration.
For this article, we will focus on the Tire Reverse Engineering workflow as the source of the Detailed Tire Model. The workflow is as follows:
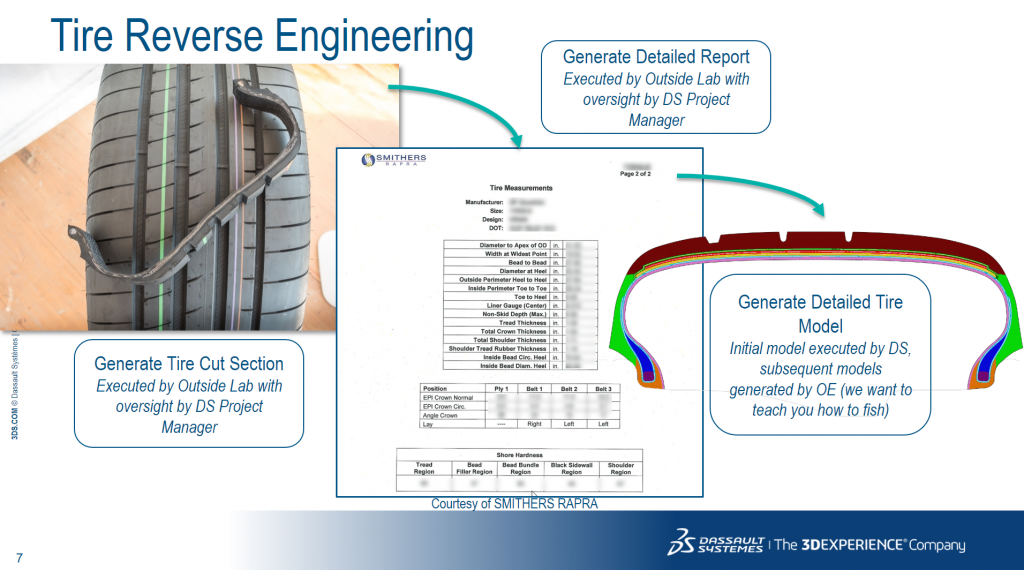
Essentially, the external test lab will capture the profile of the tire via a CSA (Cut Section Analysis). Additionally, they will 1) measure the ShoreA Durometer for each compound and 2) the details of the reinforcements, including diameter, spacing and angle. For metallic belts, the angle can be determined with a voltmeter.
At Dassault Systèmes, we have the expertise to manage this aspect of the project and subsequently train this technique to anyone interested. Moreover, we have the expertise to consume this data and create an accurate Detailed Tire Model; of which is the basis for creation of the reduced order tire model and enables the realization of System Level Virtual Testing.
The virtual tire tests take the following form:
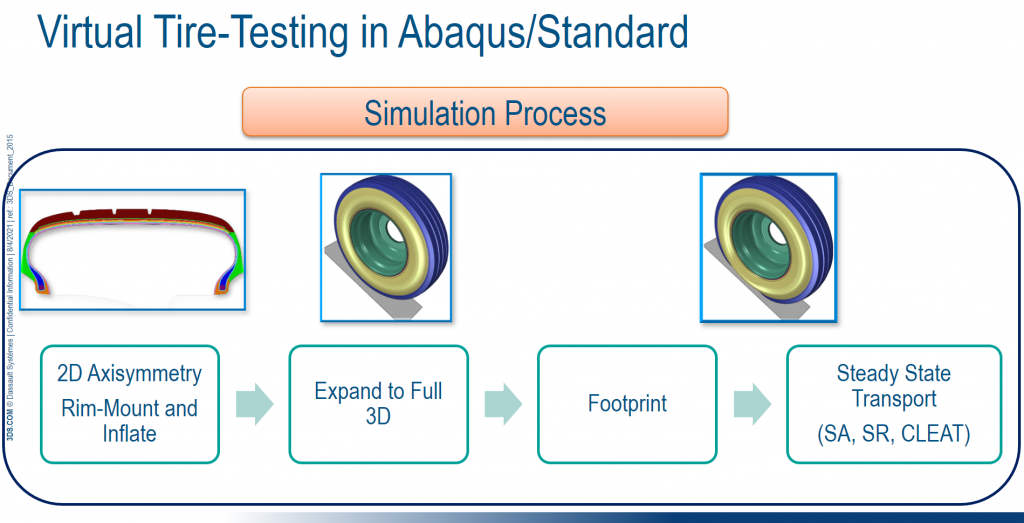
Where the following definitions apply: (1x and 2x TRA Radial Load, Tire and Rim Association)
- SA → Slip Angle (with our without IA, Inclination Angle)
- SR → Slip Ratio (with our without IA, Inclination Angle)
- Cleat → Cleat Test, to be done in either Abaqus Standard or Abaqus Explicit. We will create a separate blog for this topic.
The first virtual test is Slip Angle. We must remember; the primary goal of the virtual test is to accurately replicate the physical test. Now, for these types of tests, the build-up of force will saturate and then decay based on the interface flash temperature that arises from frictional heat dissipation. With Abaqus, this behavior can be easily captured via the use of a 3-Dimensional friction surface. An example is of the form μ=f(slipVelocity,P). Where, slipVelocity is the relative slip velocity at the tread-road interface and P is the normal contact stress. Since we are talking about the steady state response, the flash temperature can be captured in the slipVelocity parameter via a calibration of slip velocity to surface temperature. Essentially, one would carry-out a simple block-test at varying velocities and normal pressures to calibrate this frictional model. Once complete, each unique road-tread interface has its own 3-Dimensional friction model; much like a fingerprint for road surface (fractal length scales represented) – tread compound (stiffness and viscoelasticity) interaction. An example response of this test is as follows:
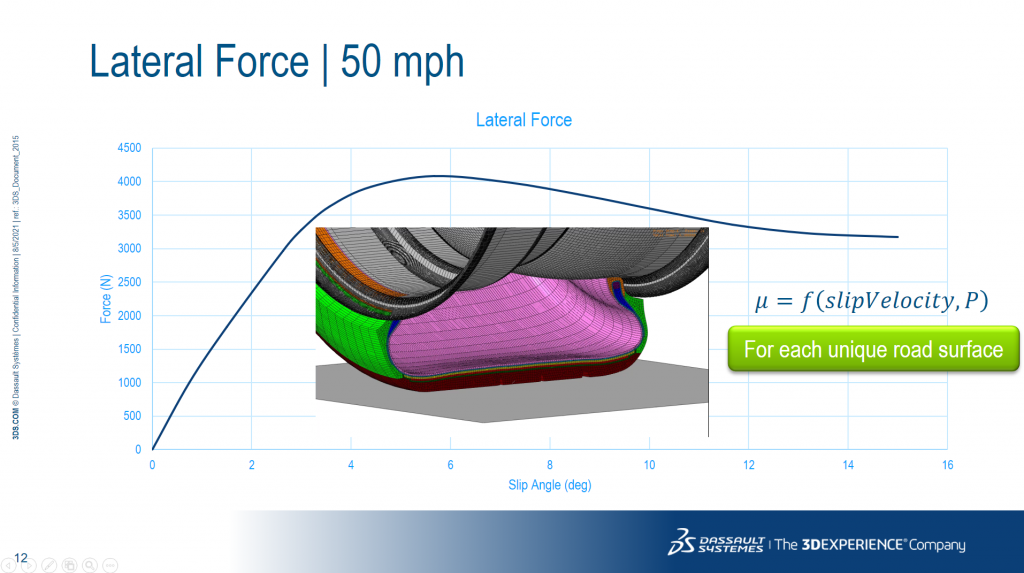
And… an example of the Slip Ratio test is as follows:
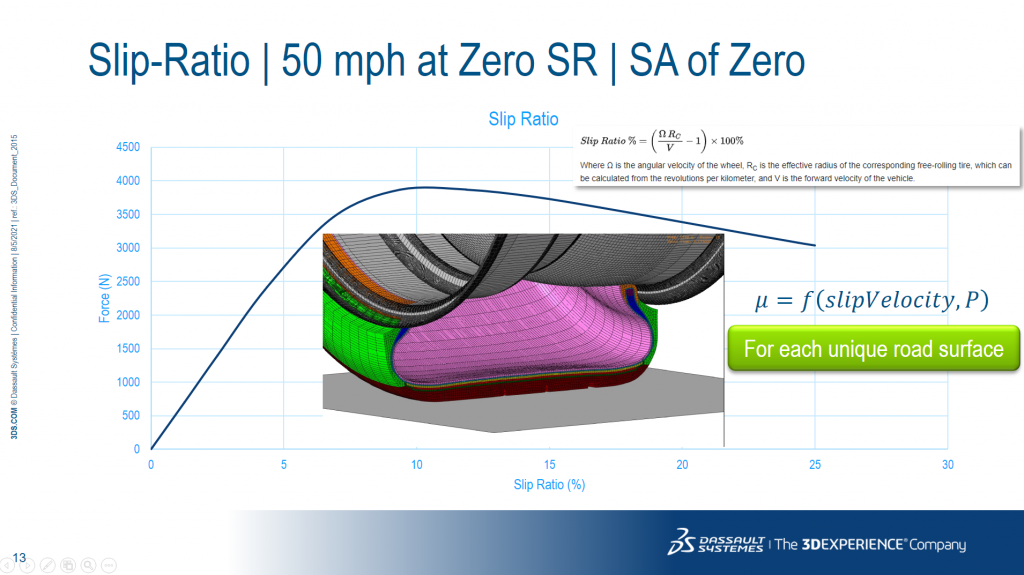
Historically, these two tests were done physically as the simulation tools were not sufficiently robust and rich to handle this complex behavior; however, with the recent improvements (over the past four years or so) in Abaqus this response can be done virtually, in lieu of physical testing. This is a game-changer as it brings forward the generation of the tire reduced order model into the early stages of the vehicle design process. Moreover, Abaqus is so robust it can generate the same response at 2X-TRA (Tire and Rim Association) radial loads. This is quite impressive given the level of Sidewall flexure and contact stress involved. An example video is shown below:
Once all the required virtual test results are generated, we can move on to the calibration. For this example we will be showing the path to the TM-Easy model in Simpack. For TM-Easy, the following parameters need calibrated, in addition to the SA and SR response shown above:
- CLONG_1 and CLONG_2 → Longitudinal stiffness @ both 1xTRA and 2xTRA radial load, respectively
- CLAT_1 and CLAT_2 → Lateral stiffness @ both 1xTRA and 2xTRA radial load, respectively
- CVERT_1 and CVERT_2 → Vertical stiffness @ both 1xTRA and 2xTRA radial load, respectively
- CTORS → Torsional Stiffness of the form:
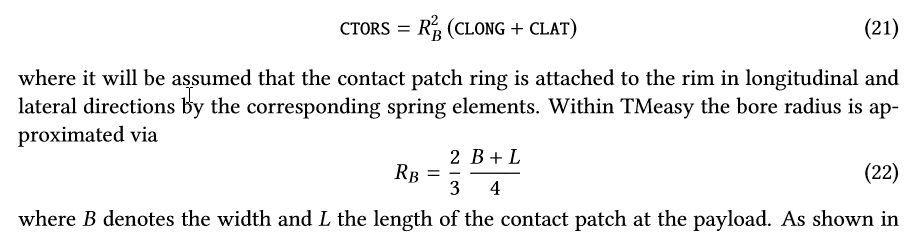
An example of the data looks like this…
The next step is to use this calibrated TM-Easy tire model in Simpack MBS. This affords the Vehicle Engineer the opportunity to the exercise the vehicle in any course excursion they see fit, with the end-goal of assess the Ride and Handling and Durability of the vehicle.
…and usage in Simpack will look something like this:
In general, the motivation is multi-faceted:
- Obstacle Impact and aggressive vehicle maneuvers are extremely complex
- The construction and response of the tire is extremely complex
- The event is highly dynamic and nonlinear
- The integrity of the vehicle, wheels and suspension is of the utmost importance and recalls are costly to the bottom-line and Company image
- Vehicle weight impacts performance, manufacturing and cost, and can be reduced through design and optimization
..Thus enabling the following:
- Running full vehicle simulations, real time, with reduced DOF models enables rapid development. Abaqus can run the virtual-tests needed to calibrate these models!
- Thus, eliminating late-stage design changes due to lack of (or late from Tire OEM) reduced order models
- Feel free to reach out to us, anytime!
SIMULIA offers an advanced simulation product portfolio, including Abaqus, Isight, fe-safe, Tosca, Simpoe-Mold, SIMPACK, CST Studio Suite, XFlow, PowerFLOW and more. The SIMULIA Community is the place to find the latest resources for SIMULIA software and to collaborate with other users. The key that unlocks the door of innovative thinking and knowledge building, the SIMULIA Community provides you with the tools you need to expand your knowledge, whenever and wherever.