The following is an excerpt from an article that was originally published in the June 2018 issue of SIMULIA Community News magazine. To read the entire article, visit the online copy of the magazine.
As electronic systems become smarter and more embedded, users need intuitive interfaces to let them control their devices easily. TactoTek uses patented injection molded structural electronics (IMSE) technology to transform ordinary plastics into smart surfaces and produce sensors and control panels that are durable, compact—and look great too. We went to TactoTek’s headquarters in Oulu, Finland, and spoke to Sini Rytky, Vice President of Product Management, and Anne Isohätälä, Antenna Specialist, about the latest advances in smart surfaces, and how they use SIMULIA simulation tools to design their unique products.
What are injection molded structural electronics?
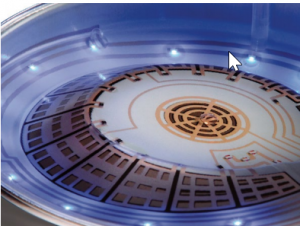
Injection Molded Structural Electronics (IMSE) is a combination of printed electronics and discrete electronic components printed and placed on a film, thermoformed to 3D geometry, and finally injection molded to a fully-sealed part structure. What applications does the technology have—some specific examples would be good (e.g. in automotive). IMSE is a perfect match when creating seamless surfaces inside cars or appliances. IMSE part thickness is usually 2–3mm, which makes it ideal for space-limited locations such as door trims. Typical use cases in car interiors include overhead control panels, door trims and seat control units. For appliances such as washing machines, this could be front panels, light switches and other similar control panels.
What are the benefits of IMSE, for users and for OEMs?
1. Technology • Creating electronic functionality on 3D seamless surfaces made out of plastics, wood, leather. Industrial designers are not limited or restricted by traditional form factors but they can create intuitive user experiences by placing electronic functionality to locations that are not accessible with traditional electronics and mechanics • 90% less depth for products • 50-70% less weight for products • Excellent touch response and antenna performance since we are able to print very close to the product surface (NFC performance improved 40% in one of our use cases)
2. Total Cost of Ownership • +30% savings in assembly costs due to “single-part assembly” • Reduced amount of tooling needed due to fewer parts (for example typical overhead control panel has some 50–80 different parts, whereas IMSE less than 10) • Service time reduced by up to 40% due to single part assembly • Faster product updates due to “single-component customization”
3. Durability and reliability • Shock and impact resistant • Protected from moisture and debris due to fully encapsulated structure • Operating temperature range Celsius −40°–+80°, we have even tested our products in boiling water (>100) and they are still functional afterwards
What are some of the design challenges of IMSE?
Typical design challenges (that TactoTek has solved and has the design guidelines on) include: • Optimization and behavior of the material stack to achieve optimal performance for different geometries (selecting the right film-ink-adhesive-component-resin combination). This is something that we would like to highlight the most, and which is one of the most important elements based on our own research • Geometrical properties for in-molded illumination • In electronics design, we are currently facing some limitations from the design tool point-of-view. We are forced to manipulate the traditional PCB layer stack whereas in film we are not able to create different layers the same way as with PCBs. This creates a lot of manual work and extensive need for manual checking • Component placement and component-to-component distance for LEDs to achieve needed brightness and uniformity, still eliminating the light leakage
What new opportunities prompted your team to start using simulation?
Our team is developing a new processes and technology where traditional design rules do not apply anymore. Simulation was seen as a solution to both verify the operation of electrical functions before building real parts and to speed up the design and time for fine-tuning.