Our partner, the Simpleware™ Product Group at Synopsys, provide software solutions for Abaqus customers. In this project, Hadass Jessel of Bar-Ilan University and Augmanity Nano, Ltd. looked at how avian nests contain design strengths that can be applied to Additive Manufacturing.
This post was written by Jessica James, Business Process Analyst at Synopsys’ Simpleware Product Group.
Avian nests offer some unexpected design insights, sharing similarities with Additive Manufacturing technology. Research carried out by Hadass Jessel at Bar-Ilan University and Augmanity Nano, Ltd. used µCT data, Synopsys Simpleware™ software, and SIMULIA Abaqus to better understand how birds’ nest material properties integrate with design choices. Focusing particularly on edible-nest swiftlet nests and their use of saliva as a material, Jessel generated Finite Element (FE) models in Simpleware software. When analyzed in Abaqus, these models show remarkable consistency between macro and micro-scale structural patterns, as well as an overdesign strategy to protect eggs.
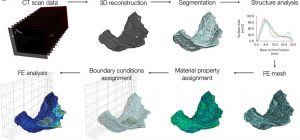
Generating Accurate Models from Scan Data
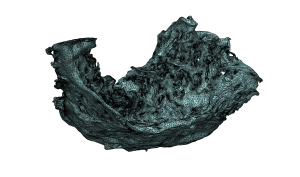
Swiftlet nests were obtained from a commercial farm and scanned using a SkyScan 1176 high-resolution µCT machine. The data was then imported to Simpleware ScanIP to visualize and segment regions of interest. The image data was resampled for efficiency and artifacts and noise from the scan corrected, with thresholding tools segmenting the mask from background noise. In addition, a flood-fill tool was applied to remove non-connected parts of the scan, and a recursive Gaussian filter used to reduce the effect of image noise. To achieve a high-quality simulation, closed pores with fewer than 125 voxels were selected to cut down on simulation time whilst maintaining a high-quality model.
The morphometric parameters of the whole nest were calculated in Simpleware software, including pore analysis. Measurements were taken and a script used to slicing the different image masks in yz, xz and xy coordinate planes. The goal of this step was to interactively visualize and analyze the pore mask in the model, for example to understand scattered pores between saliva strands.
Simulating Stress and Strain in Abaqus
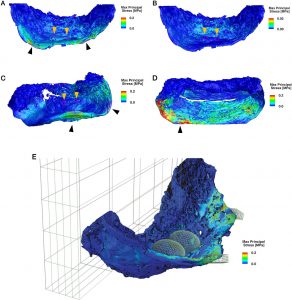
Simpleware software generated high-quality FE meshes showing microstructure for analysis in SIMULIA Abaqus. A high level of geometric accuracy was obtained for the detailed nest microstructure and porosity. Contact entities and nodes were defined in Simpleware software before being exported in a dedicated Abaqus solver format. The material properties used for simulating stress and strain were obtained from in-situ uniaxial tensile testing using scanning electron microscopy.
In Abaqus (version 6.14), the FE meshes were set up following the nominal stress-strain curve, and a linear elastic model to account for small deformations. The material used was assumed to be isotropic at the fiber level, with simulations assuming a worst-case scenario with two birds and two eggs applying gravity under different loading conditions. The loading areas predefined in Simpleware software contained a certain number of nodes to realistically model stress and strain. The results in Abaqus showed maximum principal stress at the end of each linear static loading scenario, where effectively the design means that the central ‘egg-region’ of the nest experiences lower values of stress than the outside rim, protecting the eggs.
Conclusions
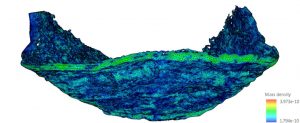
The simulations of the edible nests created from saliva demonstrate a remarkable similarity in terms of macroscopic (weight, shape) and microscopic (pore area and distribution) properties. This suggests that the nests are constructed with specific design principles to support a load of two birds and two eggs. The management of peak stresses means that an optimal nest structure can bear a load without fracturing the nest.
The study shows how a single material, properly distributed for a specific structure, can be made sustainable and resilient. The design principles of this method, involving layering of materials, offers parallels with Additive Manufacturing software techniques, and insights into biomaterials and overdesign strategies in nature.
How Simpleware software can help
Simpleware software provides software solutions for 3D image data (MRI, CT, micro-CT…) processing for multiple industries, including the Life Sciences and Materials and Manufacturing. The software exports simulation-ready models directly to Abaqus and is widely used by customers of both software to connect 3D scanning with simulation.
You can learn more about what Simpleware software offers here: https://www.synopsys.com/simpleware.html
References: H.R. Jessel, S. Chen, S. Osovski, S. Efroni, D. Rittel, I. Bachelt. Design principles of biologically fabricated avian nests. Nature: Scientific Reports, 2019, 9:4792.