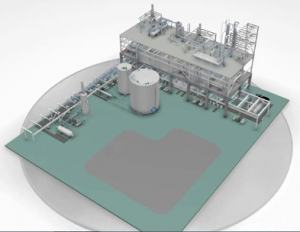
Organizations in the Energy & Materials industry invest significant money and other resources in capital projects with highly uncertain outcomes. They build plants, vessels, pipelines where costly problems can occur. It is essential to account for these problems during every stage of the plant lifecycle, from design to decommissioning. Simulation provides valuable solutions by giving clear insights into these complex systems. However, the transformation happens when simulation is used to build and maintain plant models that are driven by real world data.
In a new podcast series, Digitally Transforming Capital Projects, Dassault Systèmes discusses digitally transforming capital projects in the Energy Process and Utilities industry. The following is one in the series, interviewing Dale Berry, Senior Technical Director, Dassault Systèmes on how simulation driven design, construction and operation could help manage the complexity of a capital project. Below we’ve included an excerpt from the interview.
You can find the podcast it its entirety, here.
Also, don’t miss out on the other podcasts in this series, Digitally Transforming Capital Projects, here.
Howie: Hi, welcome to Dassault Systèmes podcast series on Digitally Transforming Capital Projects in the Energy, Process and Utilities Industries. In this podcast entitled Simulation-Driven Plant Design and Operations. We discuss the role of simulation and improving the design and operation phases of capital projects. I am your host, Howie Markson, and with me is my colleague Dale Berry, senior technical director for Dassault Systèmes’ SIMULIA brand. Dale has over 30 years’ experience with simulation in the application of simulation to solve industry challenges. Welcome Dale.
Dale: Hi, Howie. Thanks for having me.
Howie: All right, let’s get started. Dale, can you define what is simulation and how does simulation apply in the EPU industry?
Dale: Sure, and that’s a great first question, Howie. Simulation is the ability to predict realistic behavior of how a plant or a system operates fully in the computer. So I think your audience is very familiar with the benefits of testing. You build a prototype, you go into a test lab and conduct a series of tests and you learn something about the behavior of that system. Simulation lets you do that fully in a computational environment. It’s based on software that contains physics and response, stress, thermal, heat, loads. So really what you have with simulation is the ability 24/7 without an expensive test lab to build an operational behavioral model of your system, whether it’s a part or even a full plant and learn how it’s going to behave under various scenarios. I think a lot of organizations in the energy process and utilities industry already have a lot of activity going on in the simulation area, and it’s growing. Today, simulation is being used at the plant level and many of our customers are employing it, especially for things that cannot be otherwise tested. This is especially where the benefit of simulation and learning and knowledge that you get out of simulation can be valuable in this industry.
Howie: Okay, so you’re saying, so more people are using simulation sounds like it’s a good way to maybe reduce different kinds of risks. Maybe cost, safety. What are the main benefits of using simulation?
Dale: Right, so you hit on the key ones there that are owner operators and others in the industry are particularly interested in safety, reliability, uptime, quality. And simulation has immediate bearing on all of those topics. You know, for example, it’s hard or really impossible to test some of these complicated systems at the fringes of their operating environment, you know, during overload scenarios or accidents. And so simulation gives you the ability to go in and understand how your system is going to behave, not just when it’s operating normally, but when it’s operating off nominal, so to speak. The other thing that is important is from a reliability perspective, it’s important for these complicated and expensive plants to be up, operating as much as possible. And so simulation is very important then is used heavily to try to help keep the plants going, try to help understand when accidents might occur, you know, little things that occur in the course of ordinary business. And so those topics are really the economic drivers compared with the expense of testing. Simulation is a much more viable and less expensive alternative.