This blog was originally published in April 2019.
Comfort is more than just physical. Ask any would-be electric vehicle owner who is still holding off on purchasing one because of range anxiety: that distinctly uncomfortable feeling that your new vehicle might not make it from point A to point B due to limited battery life.
These fears have a basis in truth. According to studies, extremely cold weather can reduce EV range by more than 50%. Why? Traditional internal combustion engines generate waste heat under the hood, which vehicles can partially recover and use to heat up the cabin. But EVs must rely almost entirely on the battery alone to provide the energy needed to warm the cabin and make occupants comfortable – and the colder it is outside, the greater the draw on the battery, which can dramatically reduce battery power and vehicle range. A similar impact is observed with EVs in warmer conditions when energy must be drawn from the battery to cool the cabin.
Range anxiety can chill not only potential EV buyers – it could chill EV drivers, literally, if they avoid cranking the heat on the coldest days to preserve vehicle range, or if the climate control system is built to automatically shut down to preserve range. In our last blog series, we discussed how simulation helps OEMs design for more efficient vehicle cool-down on hot summer days. This blog will explore vehicle warm-up, and how OEMs can design electric vehicles to preserve battery life even in the coldest weather, when the battery must take on the added burden of keeping passengers comfortable.
Global Trends Heating Up the EV Market
In the face of increasing global demand to reduce fleet-wide emissions, along with growing competition in the EV space from traditional players and new market entrants alike, passenger vehicle OEMs are seeking new design solutions to improve cabin comfort without compromising EV range – especially in extreme weather.
Digital simulation with SIMULIA PowerFLOW offers a new way to evaluate climate system design and energy consumption together – well before physical testing begins – to ensure that potential issues with battery range, passenger comfort, or both, are resolved without costly rework and launch delays. Three benefits of digital simulation with PowerFLOW offer significant advantages over both physical testing and other digital methods. PowerFLOW helps engineers to:
- Accurately capture the impact of cabin design on human thermal comfort,
- Evaluate energy balance to discover and improve sources of energy loss and inefficiency, and
- Simulate active climate systems: comfort-enhancing technologies that use less energy.
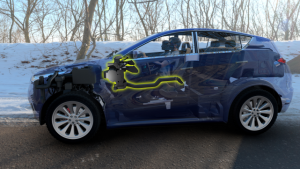
Let’s examine each of these three in turn:
1: Putting the Human in Human Comfort Simulations
Determining the right amount of energy needed to balance cabin comfort and battery life is a daunting task. It starts with determining what will make the driver and passengers attain and maintain thermal comfort. Thermal sensation and comfort measurements obtained from human test subjects can offer undeniable realism, but it’s neither cost-effective nor feasible to use human subjects during every climate control test.
Using digital simulation in PowerFLOW coupled with PowerTHERM solutions for cabin comfort, engineers can design a cabin that ensures passengers will be comfortable when entering a vehicle and driving away in cold weather. Simulation re-creates real-world conditions, wherein a human in a comfortable environment gets into a vehicle that has been parked outdoors in cold weather for several hours. The time it takes to heat up the cabin and provide comfort to the human model(s) can then be accurately predicted, giving engineers the ability to determine if a design performs as expected in terms of comfort. Human body parts like back, thigh, and hands, which are in contact with the cold seat, experience severe discomfort and coldness initially after the human enters the vehicle. Using simulation to understand how much time it takes to attain a comfortable state for such uncomfortable parts, engineers can fine-tune the design, including the HVAC system controls, ensuring overall as well as local comfort for passengers while maintaining vehicle efficiency.
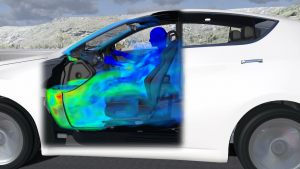
Digital simulation in PowerFLOW and PowerTHERM leverages a human comfort model that can simulate multiple humans together in different configurations within the vehicle geometry, along with many different body types – including gender and physiology. Thus, cabin designers can sample a pool of virtual humans for comfort: a task than just cannot be achieved realistically in experiment. The unique human comfort model accounts for all modes of heat transfer and the thermal response of the human body, including metabolic activities like blood flow, shivering, sweating, and more. By modeling the heat exchange happening between different humans, cabin walls, and the ambient environment, designers can consider thermal sensation and comfort for all different human body types, including percentile, physiology, and clothes, to more accurately predict how the design will perform under many different real-world conditions.
2: Calculating Energy Balance to Reduce Energy Loss
Physical tests can’t detect sources of energy losses. While thermal cameras can sometimes be used for this purpose, they lack the robustness and repeatability of digital simulation. By evaluating the energy consumption and energy losses experienced throughout the cabin, digital simulation can help engineers target areas to reduce losses and curb consumption – helping to achieve the levels of energy efficiency necessary to improve electric vehicle range.
Energy management to preserve EV range is a high priority for OEMs. But waiting for physical testing to understand energy performance severely limits the design iterations that can be tested to meet these critical new consumer and regulatory targets. Identifying these critical design changes earlier in design and development – when the vehicle is still just a 3D model – reduces the number of costly iterations and rework that must be performed with physical prototypes, accelerating design and eliminating cost overruns for product development teams. Relying on physical testing alone limits new, energy-saving design innovations at just the time when they should be unleashed.
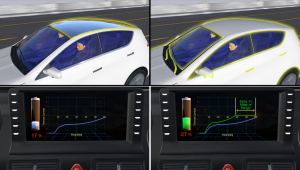
New design solutions like different insulation options and different glass materials can easily be simulated and explored with PowerFLOW so engineers can introduce the right design solutions that help to better maintain passenger comfort while conserving energy. When less energy in the form of heat escapes the vehicle, passengers warm up more quickly and maintain comfort longer – so that the vehicle uses less energy, saving on battery power and adding to range.
3: Evaluating the Impact of Active Climate Systems
As relatively new advancements in vehicle comfort solutions, active climate systems– that is, cooling/heated and ventilated seats, steering wheel warmers, etc – do more than offer personalized comfort that each passenger can control to their own liking. Active climate systems actually use less energy because they can quickly heat up (or cool down) more localized areas like hands, arms and legs, thighs, and back – sensitive regions that react quickly to cold and warmth, providing comfort sensations sooner while using less energy than traditional heating and cooling systems do. When used together with traditional methods, these solutions can augment human comfort, helping drivers and passengers rely less on solutions that spend more energy while attaining the same levels of comfort – ultimately improving battery life and range.
Using PowerFLOW solutions, active climate systems can be added to the digital cabin and designers can assess passenger comfort gained from these systems to design a cabin with the same level of comfort while relying less on the HVAC system to provide the energy needed to achieve that comfort. Placement and sizing of the active climate systems can then be optimized so that time-to-comfort targets are achieved with minimum energy consumption. In this way, PowerFLOW solutions offer a method to design cabins and HVAC systems that improve overall vehicle efficiency.
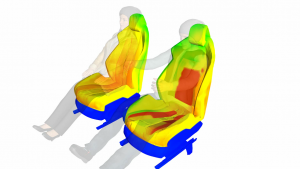
Together, these three key advantages introduce a highly differentiated approach to cabin comfort simulation and design available only in SIMULIA PowerFLOW. Engineers and designers can design and innovate more efficient, more effective human comfort solutions that achieve and maintain warmth more quickly, expend less energy from the battery, and maximize EV range. And reducing range anxiety can only add to driver and passenger comfort – helping consumers and OEMs alike get more comfortable with our undeniable electric vehicle future.
Want to learn more about Dassault Systèmes’ simulation solutions for electric vehicles? Visit: go.3ds.com/TrustTheDrive
Want to connect with other Electric Vehicle experts and access our relevant resources? Visit the dedicated Electric Vehicles page in our SIMULIA Community to start exploring.
References:
Nagarajan, V., Bhambare, K., Han, J. “Cabin Heat-up Simulation with Human Comfort Evaluation for Multiple Humans.” JSAE, 2017.
Mukutmoni, D., Han, J., Alajbegovic, A., Famibelle, S., Colibert, L. “Automotive Windshield Defrost Performance Evaluation Using a Simulation-Based Approach.” SAE-TMSS. October, 2013.
Bhambare, K., Nagarajan, V., Han, J., Filippova, O., Konstantinov, A., Kelly, J., Wang, K., Gu, X. “Defrosting Simulation of Front Windshield and Side Window Interior Surfaces in an Extreme Cold Climate.” 2015 SAE Thermal Management Systems Symposium, September 29 – October 1, 2015
SIMULIA offers an advanced simulation product portfolio, including Abaqus, Isight, fe-safe, Tosca, Simpoe-Mold, SIMPACK, CST Studio Suite, XFlow, PowerFLOW and more. The SIMULIA Community is the place to find the latest resources for SIMULIA software and to collaborate with other users. The key that unlocks the door of innovative thinking and knowledge building, the SIMULIA Community provides you with the tools you need to expand your knowledge, whenever and wherever.