Industries of all kinds have seen considerable changes in recent years, but perhaps the most radical transformation is happening in transportation and mobility.
“We’re seeing two major revolutions in the auto industry: the electrification of vehicles using different propulsion systems and the development of autonomous driving, which uses sensors to enable cars to drive themselves,” said Scott Piper, electromagnetics engineer. “Both of these areas bring opportunities to do things better and to achieve things that have never been done before.”
To get these advanced technologies to market quickly, it’s vital for manufacturers to compress the engineering development cycle.
“The longer the engineering design cycle is, the less opportunity we have to put the latest technology on the road,” Piper said. “If it takes us ten years to develop a car, then that vehicle will have ten-year-old technology. Meanwhile, if a company is first to market with a particular technology, it offers customers something its competitors don’t have. Our goal is to shorten the design cycle so we can get the latest technology in people’s hands. To do that, we need to find a way to design vehicles and ensure they pass all requirements within a short time.”
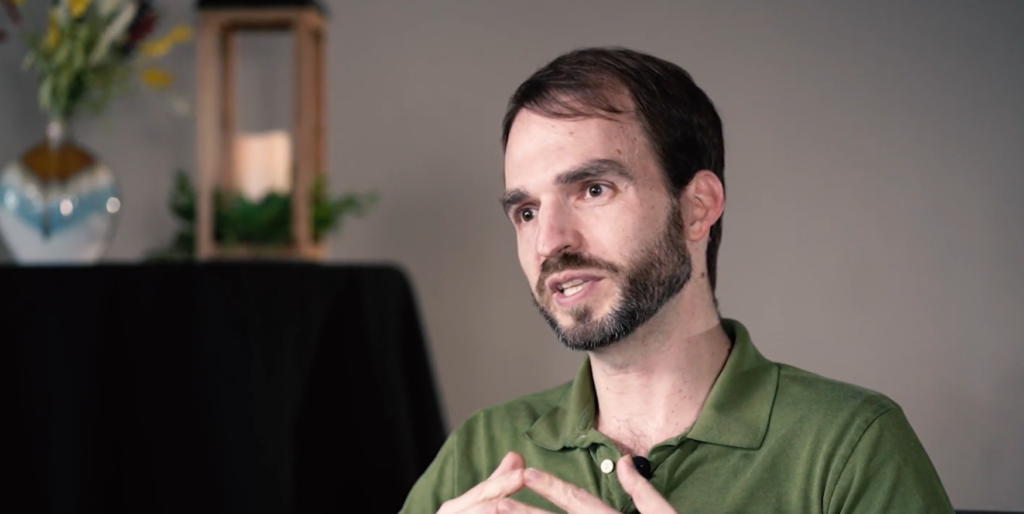
Left-shifting the Engineering Cycle
In many cases, one major obstacle stops manufacturers from achieving the speed they need.
“The current process for many automotive manufacturers is to build a test vehicle, usually by hand and with various levels of prototype parts,” Piper said. “Then they test this hand-built vehicle to make sure everything works OK. If it doesn’t, they must tweak things and figure out what went wrong. It’s a very lengthy and expensive process. But if engineers can determine a good design versus a bad one based on the design concept alone, without having to build it to see if it works, that will help get the product to market faster.”
Unified modeling and simulation (MODSIM) can empower vehicle design engineers to do just that. By testing, analyzing and amending vehicle designs in the virtual world, they can identify and resolve issues early in the design cycle. This process, known as left-shifting, can dramatically cut the time, cost and materials needed to get the design right.
But for Piper, left-shifting goes beyond modeling and simulating the visible components of a vehicle. When you specialize in a field like electromagnetics, you’re dealing with unseen and often unknown properties.
“Design always includes some unintentional aspects – things that you don’t really want, but which physics says have to be there,” Piper said. “That’s the major issue that we face.”
Everything is an Antenna
Electromagnetic compatibility (EMC) is a case in point. “If you design something electrical, it will emit some level of radio waves which can interfere with wireless technology inside cars,” Piper said. “EMC looks at the interactions between those electronic components and electromagnetic waves.”
For example, it’s essential to ensure that brake control or power steering electrics will work properly when exposed to high levels of radio frequency interference – such as when the vehicle is driving past a radio station. Among all the wires and conduits a vehicle contains, the possible EMC issues are complex and often unknown.
“When you think about it, everything is an antenna,” Piper said. “We might only call one of the car’s wires an antenna because we’ve designed it to play that role. But all the other wiring and even the shafts, coolant lines and the car itself, are potentially antennae. We don’t know what band these antennae pick up or whether they will bring in a bunch of noise or transmit it outward. Typically, we discover this through physical testing.”
In the past, that testing involved bombarding physical products with radio frequency interference to ensure they still work properly.
“There are design guidelines that can be followed to lessen the risk of EMC problems and we do that as much as possible upfront,” Piper said. “But without knowing everything about the physics of the situation, it’s hard to do it with certainty.”
Simulation to Silence Interference
Simulation brings a lot more knowledge to that picture. It gives engineers valuable information to create EMC-compliant designs before the product is built.
“Any particular wire in a car has been designed to serve a specific purpose without considering its electromagnetic properties,” Piper said. “Using electromagnetic simulation tools, you can quantify how these random structures behave within the vehicle. You can know exactly what frequency they tune up at or even how to tweak them so they’ll tune up at a different frequency.”
Piper uses SIMULIA’s CST Studio Suite technology to capture the geometrical aspects of the vehicle – all those hidden antennae – and figure out the electromagnetic characteristics of unintentional interactions. This helps ensure the vehicle will pass physical tests without time-consuming and costly redesign and rebuilds.
“I’ve been using CST products for quite a while,” Piper said. “For EMC work, it’s valuable to have a tool that is so easy to use for broadband problems. You run one simulation and get the full spectrum, whereas with other methods you might have to simulate every frequency individually. I really like the fact that CST has an integrated circuit solver. When you’re simulating wires, the loads at the end of the wire make a difference. With the integrated circuit solver, you can simulate the entire mechanical piece and then change the loads on the end of the wires using a post-processing design studio.”
Exposing the Unknown
Simulation enables Piper to try different scenarios and learn more about the electromagnetic properties in a vehicle. But with so many unknowns involved, a lot depends on asking the right questions. How does CST Studio Suite help Piper to decipher these unknown quantities?
“A lot of people say that simulating EMC is not possible because there are so many unknowns,” Piper said. “When you design an antenna to work at a particular frequency, you’re making everything intentional. With EMC, you get all these interactions you didn’t want and have to figure out whether they will cause a problem. It’s very open-ended and that’s something that simulation programs have trouble doing.”
Asking the right type of questions can help, even if you don’t know exactly the question you need to ask.
“It’s important to ask questions that can yield a specific answer,” Piper said. “Simulation is very good at validating an idea or finding the theoretical basis behind a specific problem. It’s not so good at answering general questions, such as whether there is a problem at all.”
Where more clarity is needed, bouncing ideas between people and technology can often sharpen the focus and lead to discovering the refinements required to get the desired outcomes.
Changing the Development Mindset
Condensing the engineering cycle is not simply about adding simulation to existing processes.
“Current design cycles are geared toward physical testing everything at the end because it’s easiest,” Piper said. “For instance, from an electrical point of view, you can’t have an engine controller just sitting there working on its own without the engine. You need something to represent the engine, spark plugs and everything else.”
This means that when somebody asks Piper to do a virtual test, they generally want him to run a simulation of a physical test. But while that’s perfectly possible, the strengths and weaknesses of physical testing are not the same as those of simulation.
“We need to ask ourselves how simulation can help us to know a good design from a bad one without worrying about being in the same situation we’ve always been in with physical tests,” Piper said. “Because simulating a whole car, with all those unknowns at once, may not be possible yet. But if you simulate one piece at a time and optimize them as you go, that is doable. That’s the mindset we need to grow.”
Towards an Intentional Design Cycle
Looking ahead, Piper sees a lot for the automotive industry to get excited about. And simulation is a key enabler.
“Electrification and autonomous vehicles will drive demand to get the latest technology on the road as soon as possible, instead of locking it in some design-build-test cycle for years,” Piper said. “In addition, software-defined vehicles, where companies build one hardware platform and then tweak it with software, will drive many changes that have to happen very quickly. All of this means that automakers will have less time to spend with a vehicle to make sure it works as intended.”
As a result, testing will be transformed, with physical testing moving toward the end of the engineering cycle and simulation taking its place earlier. As this happens, a shorter, more intentional design cycle will emerge.
“We’ll be able to design with more intention and understand more about what we’re doing,” Piper said. “Tools like CST Studio Suite can give us the information we didn’t have before. That’s the most important thing going forward – to have an intentional design cycle even for tough areas like EMC, where many inputs and elements are unintentional. Simulation will help us understand all these unknowns we’re trying to design for; to design a vehicle that will meet all the requirements we set for it. Then we will test it as a formality and confirm that everything happened as expected. If we understand everything, we will design vehicles that pass tests the first time.”
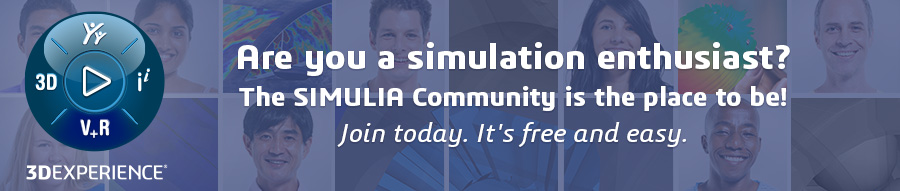
Interested in the latest in simulation? Looking for advice and best practices? Want to discuss simulation with fellow users and Dassault Systèmes experts? The SIMULIA Community is the place to find the latest resources for SIMULIA software and to collaborate with other users. The key that unlocks the door of innovative thinking and knowledge building, the SIMULIA Community provides you with the tools you need to expand your knowledge, whenever and wherever.