By Daniel de los Dolores Paradinas, SIMULIA R&D Roles Portfolio Engineering Manager, Dassault Systèmes
There is increasing demand for industrial gear units with higher efficiency, lower noise and longer life. Suppliers are pushed to design equipment to reduce operational costs and capital expenditure.
The system efficiency of industrial gear units is estimated through the evaluation of power losses, which can be split into load-dependent and no-load-dependent losses. Whereas load-dependent gear power losses arise from gears and bearings when torque is transferred, no-load losses are a consequence of the gearbox components experiencing drag in the lubricant.
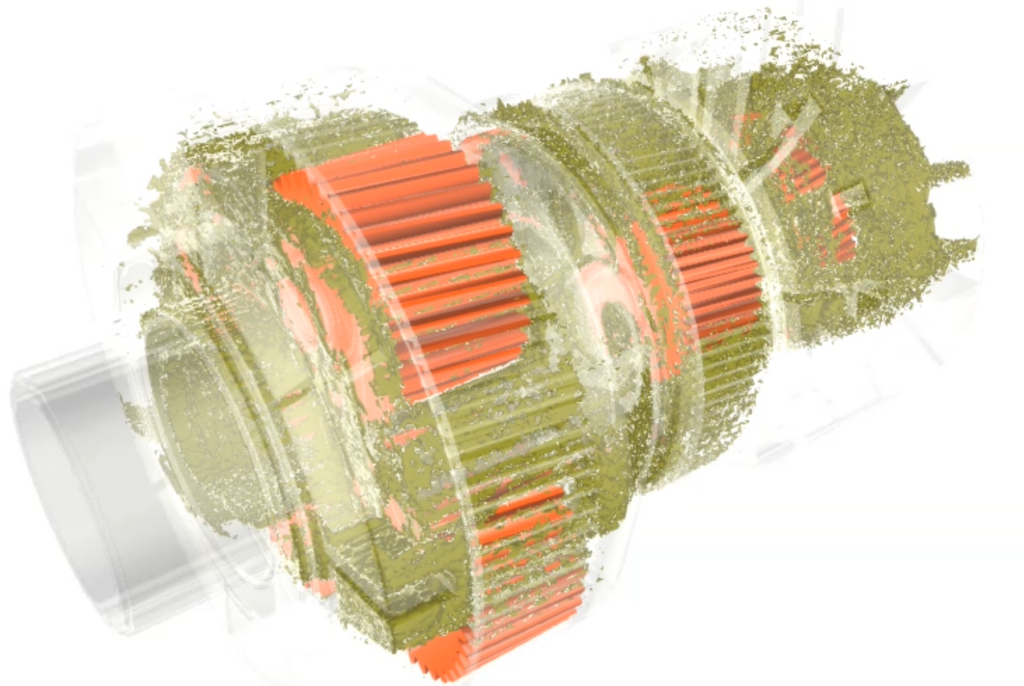
Reducing all losses while ensuring oil gets to critical locations for any operating condition is not a trivial balance for any gearbox designer. Dassault Systèmes offers powerful modeling and simulation tools integrated in a unified experience (MODSIM) to help designers tackle this challenge.
Challenges of Gearbox Lubrication Design
A theoretical prediction of the behavior of any industrial gearbox is complex to solve, since the fluid mechanics problem is related to a two-phase flow, its interface and their interaction with an arbitrary number of rotating components. Extensive experimental measurements for different operating conditions would be needed, but can lead to empirical or semi-empirical formulas that show large deviations even with small design changes.
Physical tests can give accurate information to achieve the final production design at high cost. Sometimes, however, they do not produce the appropriate data due to wrong assumptions, experimental design mistakes or simply because a key performance indicator (KPI) cannot be measured.
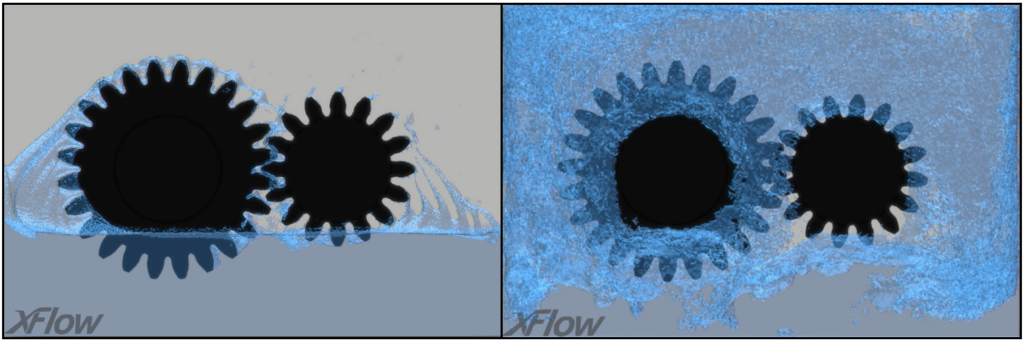
Numerical simulations can reduce the number of physical tests, providing quantitative predictions for KPIs like wetted area, churning losses or temperature distribution that can be very difficult or impossible to measure experimentally. This cuts development time and costs, and reduces the risk of failure at a late stage when design changes are more expensive.
Churning Losses in Gearboxes
Churning losses are a complex phenomenon and generate significant no-load losses when considering splash lubrication of gear units. In this kind of lubrication, the components dip into an oil bath and “splash” the oil into necessary chambers through their rotation.
The magnitude of the churning losses depends on the oil level, viscosity and rotational speed. The oil level is adjusted so that the gear teeth are not fully immersed in the bath in operating conditions. Otherwise, excessive losses will result due to the churning of the oil bath. On the other hand, churning losses decrease when the lubricant’s viscosity is reduced by the use of a different lubricant or increasing temperature. However, the viscosity must remain high enough to maintain the friction coefficient within safe limits. Finally, apart from the obvious change in splashing patterns, moderate rotational speed induces oil aeration which changes the effective oil viscosity and increases the volume of the fluid and therefore the oil level.
In the case of high-speed industrial gearboxes, using only splash lubrication would lead to extremely high churning losses due to the required oil level and the rotational speed. Therefore, they also include jet lubrication through nozzles pointed at the contacting surfaces. This is another design challenge as centrifugal forces deflect the stream of oil.
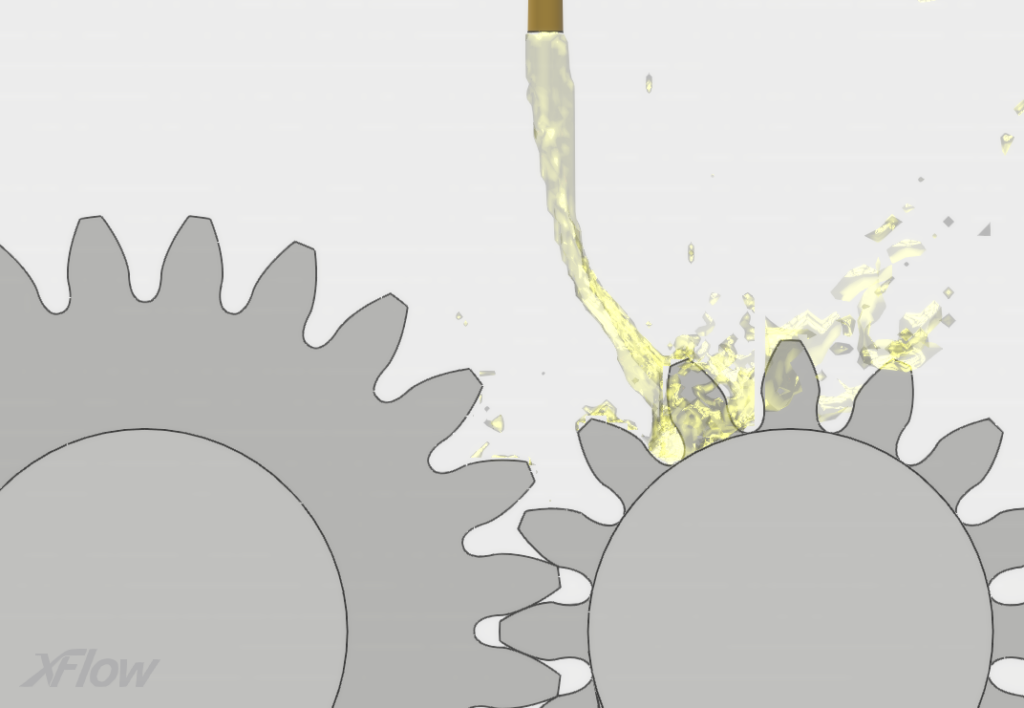
Wetted Regions and Splashing Patterns
A common KPI for any sort of lubrication method is the oil distribution in all operational conditions. This is needed for many reasons: Adjusting oil bath level, optimizing nozzle mass flow and orientation, analyzing thermal convection, etc.
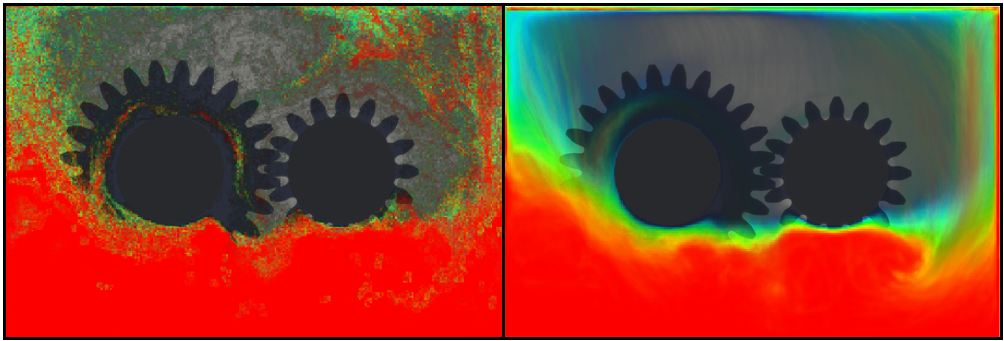
Even for moderate rotational speed, an experimental measurement of oil distribution requires high-speed cameras and image post-processing due to the high-speed oil splashing. Numerical simulations remove the constraint of fixed camera positions during the experiment, giving more analysis flexibility.
Thermal Analysis of Gearbox Oil Temperature
Gearbox power losses are chiefly transformed into heat, making the use of an appropriate cooling system essential. Otherwise the oil temperature would increase, losing its ideal properties and leading into system failure.
In order to get accurate data under controlled conditions, lubrication experimental tests keep the oil at a constant temperature through oil cooler systems.
Using a similar approach for numerical simulations, it is possible to solve the complex flow field under the assumption of constant temperature in both the flow and the solid rotating and fixed geometries. Once the flow has converged in a matter of seconds, it is possible to use the convective Heat Transfer Coefficients (HTC) to analyze the heating of components.
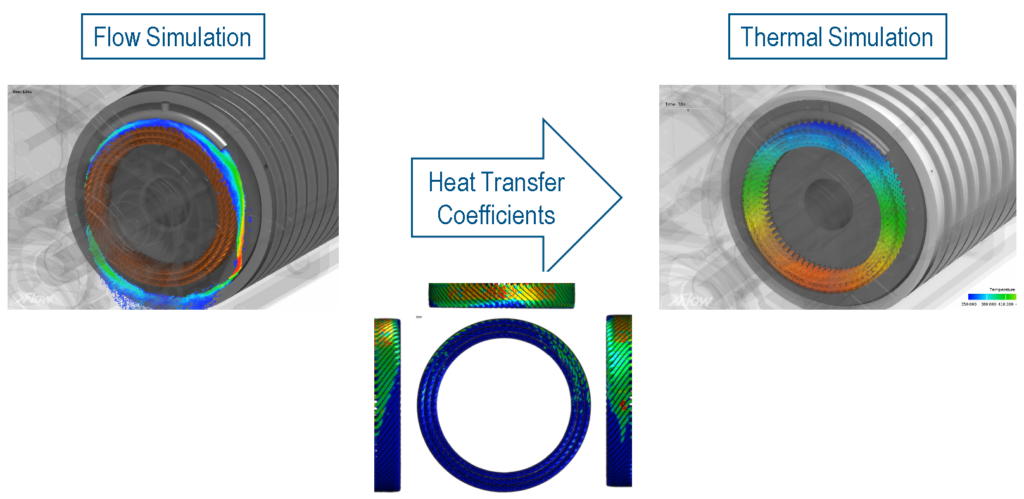
Numerical Simulations of Gearbox Lubrication
Considering the complexity of designing gearboxes and their lubrication systems, it is understandablethat a large amount of design iterations are needed. Physical testing requires investment and can only provide a limited amount of information – computer-aided engineering (CAE) tools provide the possibility of reducing operational costs and capital expenditure.
There are many models and discretization approaches. The main ones for these applications are Navier-Stokes (NS) equations with Finite Volume Method (FVM) or Smooth Particle Hydrodynamics (SPH) discretization methods, and Lattice Boltzmann equation/method (LBM).
Navier-Stokes with Finite Volume Method (FVM) gives the user the possibility to accurately capture the flow separation due to the possibility to adapt the discretization to the geometry curvature. However, topological changes to the computational domain or large elements deformations, such as where the fluid is squeezed between gear teeth, necessitate problem simplifications and sequential simulations.
Smooth Particle Hydrodynamics (SPH) is especially suited for both interactive applications and transient applications with large motions. Although it might be a good choice for lubrication applications, it is constrained to solving just one phase at competitive computational cost and accuracy.
SIMULIA XFlow follows the LBM approach that excels in tracking arbitrary moving parts and low preprocessing effort due to automatic Cartesian discretization of the computational domain. Unlike SPH, LBM makes it possible to obtain the multiphase solution without any loss in performance or accuracy. With XFlow, the behavior of both air and oil at any speed can be simulated and visualized, revealing effects that cannot be seen by the eye due to speed.
Conclusion
A precise distribution of lubrication within a gearbox is essential to ensure efficient performance and long-term reliability. Oil flow has complex behavior that is hard to analyze using physical testing. Unified modeling and simulation (MODSIM) reveals the properties of gearbox lubrication and allows engineers to analyze and optimize performance.
Losses can be minimized by finding the best viscosity tradeoff between churning and safe operation. Crucial lubrication KPIs quickly calculated with simulation ensure correct oil bath level and nozzle placement, as well as thermal performance. SIMULIA XFlow offers a powerful and accurate lubrication simulation workflow. Powered by the Lattice Boltzmann Method, it can model the flow of oil even in the narrow spaces between gears efficiently for a realistic analysis of gearbox efficiency.
XFlow simulations accelerate gearbox efficiency analysis and reduce the risk of issues discovered late in testing or while in use. MODSIM cuts development costs and time to market, allowing manufacturers to stay ahead in a competitive market.
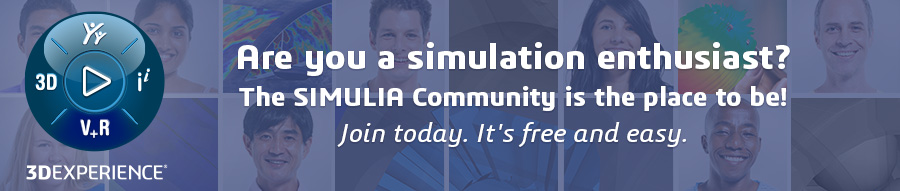
Interested in the latest in simulation? Looking for advice and best practices? Want to discuss simulation with fellow users and Dassault Systèmes experts? The SIMULIA Community is the place to find the latest resources for SIMULIA software and to collaborate with other users. The key that unlocks the door of innovative thinking and knowledge building, the SIMULIA Community provides you with the tools you need to expand your knowledge, whenever and wherever.