The automotive industry is in a state of flux due to the trend towards “CASE” vehicles – Connected, Autonomous, Shared and Electric vehicles. In this rapidly changing environment, manufacturers need to accelerate vehicle development and bring new products to market faster to beat both their competitors and regulatory deadlines.
Why CAD and CAE Belong Together
CAD and CAE have both been used in the automotive industry for decades – CAD tools such as CATIA to design components and assemble them into a full vehicle, and CAE tools such as SIMULIA Abaqus, CST Studio Suite, PowerFLOW and Simpack to analyze and optimize important aspects such as crashworthiness, antenna performance, aerodynamics and handling. Traditionally, CAD and CAE are used by different teams, with limited communication and collaboration. Bringing CAD and CAE together with a Unified Modeling & Simulation (MODSIM) approach breaks down the silos between teams and accelerates development.
MODSIM on the 3DEXPERIENCE® platform is a unique concept that unifies modeling and simulation data models on a single platform so that they become completely interoperable. This single-platform, multi-physics approach substantially accelerates design and validation, reduces the need for physical testing, eliminates errors, and democratizes modeling and simulation processes so that both designers and analysts can use them with confidence. It also brings opportunities to automate workflows and complex tasks and make them accessible through a simple user experience.
For designers and analysts, 3DEXPERIENCE provides all the information they need to develop the best product in one place. CAD data, requirements and specifications, simulation results and measured data are all stored in one place as common data models – as a single source of truth – where they are accessible to any team members who need them. Communication and collaboration are improved, and the risk of different designers using conflicting information or working from different versions is greatly reduced.
CAE is often used for virtual testing, using simulation models instead of physical prototypes to certify vehicle performance and compliance without the time and monetary costs of building vehicle prototypes. For users to be able to trust simulated test results, there needs to be certainty that the simulation model accurately reflects the design intent – MODSIM on 3DEXPERIENCE can provide that certainty, by ensuring that the CAE model is a direct representation of the design CAD and that changes to the design are automatically updated across all simulation models. Regulators demand traceability to prove that the simulation results are drawn from the real CAD data. MODSIM helps make traceability easy, maintaining a direct link between each part of the simulation model and the original design.
Accelerate Electric Vehicle Development
By 2030, the sale of new internal-combustion-only cars will be banned in the United Kingdom, by 2035 that will be extended to many other territories including the European Union, Japan and several U.S. states. Companies face a rapidly approaching deadline to convert their entire product lines to zero-emissions technology, and in most cases that means electrification.
Electric drive systems behave very differently to internal combustion engines, with different torque and efficiency profiles, noise spectra, vibration behavior and cooling needs. This means the entire vehicle needs to be designed to accommodate the batteries, motors and other systems. MODSIM allows designers and engineers to see the impact of design changes on all aspects of performance as soon as the change is made. Electric vehicles can be developed with fewer design iterations and fewer prototypes.
In particular, a holistic approach – considering and optimizing all aspects at once – offers considerable time savings. Trade-offs can be made from the earliest stages of development, helping to ensure that an improvement in one area doesn’t cause unacceptable deterioration in another. A five-year study by one leading EV maker found that optimizing all the elements of an electric drivetrain separately brought efficiency savings of between 15% and 25%. In contrast, when the company approached the e-drive as a single, integrated system, those efficiency savings reached 40%.
Early Concept Development
A car is a complex system with numerous subsystems all integrated in one tight space. There are hundreds of components and thousands of connections between them – bolts, welds, electrical connections and more. This means that a full-system model of a vehicle is incredibly detailed and massively interconnected – a change to one small component can have knock-on effects through the rest of the vehicle.
Concept Structure Engineering on the 3DEXPERIENCE platform uses the power of CATIA to accelerate the process of designing and creating a simulation-ready model of a full vehicle. Geometry creation time can be reduced by as much as 90% by automating many of the tedious processes – for example, aligning the connections between components, identifying and fixing surface errors, and creating a mesh for simulation.
Not only does this speed up design, it creates a ‘virtuous cycle’ where the simulation engineers can also work faster, as the geometry they receive is already simulation ready. They can return analysis results to the designers faster, allowing them to make any changes needed rapidly. The entire process is accelerated, meaning that engineers can explore more of the design space and evaluate more concepts to find the best one while still bringing the product to market faster.
Speed Up Development by ‘Left-shifting’ Testing and Analysis
In typical product development, most testing occurs near the end – on the right-hand side of a conventional timeline diagram. This is when the design is almost finished, and is final enough that it is worth the significant investment required to build a prototype car. If a problem is discovered at this stage, fixing it is expensive and risks jeopardizing the entire project schedule. Identifying issues earlier means they can be resolved faster and with less cost.
To enable this, automotive companies are ‘left-shifting’ their analysis using simulation and virtual testing. At any stage in development, the CAD data can be quickly converted into a simulation model and analyzed through virtual tests that accurately replicate real ones. The effect of a design change can be studied before the change is implemented, and different variations can be compared to find the best trade-off between competing design requirements.
By moving analysis as early as possible in the design cycle, manufacturers are accelerating product development and reducing the risk of problems emerging during testing. If an issue is identified, it is much easier to resolve if it is caught early, with less re-work needed. Using simulation and virtual testing also reduces the reliance on physical tests. This not only saves time and money, but it also increases flexibility, as there is less need to wait for prototypes to be built and test facilities to become available.
Conclusion
Rapid transition will be needed if the automotive industry is to meet the legal deadlines to phase out ICE vehicles. Unifying modeling and simulation with MODSIM on the 3DEXPERIENCE platform can significantly accelerate electric vehicle design and development. Bringing together all data on a single platform ensures all team members are working with the same up-to-date information, on a common data model, and democratizes the use of modeling and simulation.
At the concept stage, the use of MODSIM, Concept Structure Engineering and other simulation-powered design tools on the 3DEXPERIENCE platform can speed up geometry creation by up to 90%, allowing new projects to get started much faster. As soon as the first design is ready, MODSIM can ‘left-shift’ analysis – bring it forward in the development using virtual testing instead of waiting for physical prototypes. This speeds up design cycles and reduces the risk of expensive and time-consuming rework later.
Implementing MODSIM in the design process can help manufacturers bring EVs and other innovative vehicles to market faster and give them a head start in a very competitive environment.
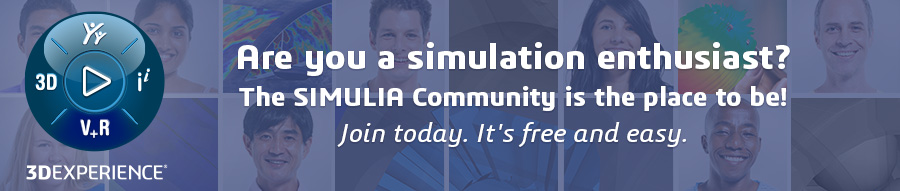
Interested in the latest in simulation? Looking for advice and best practices? Want to discuss simulation with fellow users and Dassault Systèmes experts? The SIMULIA Community is the place to find the latest resources for SIMULIA software and to collaborate with other users. The key that unlocks the door of innovative thinking and knowledge building, the SIMULIA Community provides you with the tools you need to expand your knowledge, whenever and wherever.