Neat and Clean Rims
It was a sunny Sunday. After lunch, I was doing my regular Sunday activities like lawn mowing, pruning trees, and taking care of my favorite plants in the garden. Suddenly, I noticed my new car in the garage and I realized that I bought it exactly one month ago. With great affection, I started walking towards my new car, but suddenly I noticed something and stopped. The wheels were muddy and dirty. No one wants their car to have dirty wheels after just a month when the rest of it is shining new. I walked near the wheels and noticed dark reddish black flecks on them. Hey, how did these nasty flecks get on my rims? Is it dirt from the road? Or did my car have ugly wheel syndrome? These were all the questions running through my mind.
Well, I am sure that everyone has seen car wheels like this; perhaps you have just not noticed it. I used to think that it might be just dust from the road. However, when I noticed it on my car I researched it and came to know that it is not just because of road dirt, but it is also due to brake dust from the brake pads. Now you might be wondering, what is this brake dust? Where does it come from? Do new brake pads erode that fast? Well, no need to worry! Fortunately, brake dust is not a sign that your car brakes are failing. It is a result of different materials being used on the brake pads and rotors and their wear is a normal consequence of the braking action. However, none of us would like the wheels of our new car to look old and dirty.
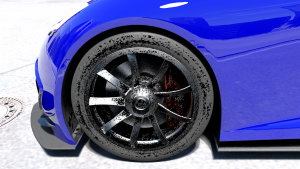
What causes brake dust?
Over the years, the formulation of brake pad materials has changed as vehicle manufacturers try to build vehicles that are lighter and environmentally friendly. Getting maximum brake pad life with enhanced brake performance is always a challenge for a brake manufacturer. Unfortunately, brake dust is unavoidable, and it is a by-product of brake wear. In the braking action, because of friction, the brake pads heat up and the pad material wears off the surface of the pads. In modern vehicles, most brake pads are composed of semi-metallic compounds consisting of steel fiber mixed with other additives to bind the brake pad material together. Friction during braking produces a complex composition of brake dust which can be of environmental concern.
The dust deposition pattern depends on the mass, density, and diameter of the dust particles. In addition, deposition is highly dependent on the flow field around the brake assembly and wheel; the different sizes of the brake dust particles produce different deposition patterns. The larger diameter particles can be more damaging to the wheel rims that are in close proximity. If they are hot enough, the larger particles can stick to the rim paint. They are hard to clean up and can cause rust on the fender. On the other hand, lighter particles can spread over a larger area of the car beyond the wheel rims.
How can we prevent this dust from soiling the rim and wheel?
There are several different ways to mitigate this problem: you can use brake spray cleaning solution to clean off the brake dust, or you can install shields that divert or collect the brake dust, or you can use alternative braking systems or pad materials that produces less brake dust. Depending on the solution that you adopt, you might need to pay a lot for extremely pricey brake pad materials that contain synthetic fiber and Kevlar alternatives. For normal passenger cars, that is probably not a good option on which to spend your hard-earned money.
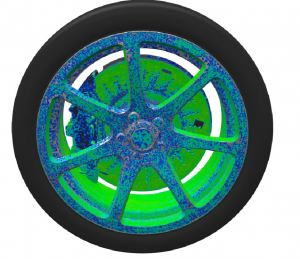
Therefore, the question remains – how do I avoid brake dust soiling, or at least how can I reduce it? Many car manufacturers are now trying to use aerodynamics to enhance brake cooling, which also reduces the amount of brake pad wear. However, this does not necessarily reduce the brake dust problem because dust deposition is highly dependent on the transport of the particles, although improved cooling is likely to ensure that fewer particles will be produced by friction on the brake pads. The airflow on the brakes can be adjusted so that it redirects the brake dust away from the rim and ensures that the brake shield collects more dust. A brake dust soiling workflow can provide a better understanding of the deposition rate and deposition pattern, which can help in the early-stage design of brake cooling ducts and avoid the necessity of expensive changes at a later stage.
Objective
The primary aim of this solution is to design a brake system with better particle control performance and dust shields to collect the brake dust without affecting the thermal performance of the brakes. Hotter brakes wear faster and they start to exhibit brake fade faster. Faded brakes cannot generate enough friction to produce adequate braking action. Therefore, the solution needs to be integrated with brake cooling performance. In addition, it helps to identify the deposition rate and pattern, so that remedies can be found early in the design phase.
Solution
The solution in this post shows how the brake system can be designed for better control over the brake dust particles, which is important especially for undesirable rim paint, body, or environmental contamination which can potentially lead to maintenance issues. This solution is also ideal as it dramatically reduces the need to build expensive prototypes and perform extensive physical testing. The simulation driven design process evaluates the brakes integrated with the vehicle in realistic operating conditions by considering the overall aerodynamic interactions. The simulation process can accurately predict the behavior of the particles during the braking process and show how these particles are deposited on critical parts like wheels, rims, and body panels. In addition, our solution allows the user to assess brake soiling and brake cooling in a single simulation. It provides engineering insight into the complete flow field, and the transport and deposition of particles are available as a result of the simulation. This detailed information is very difficult to determine by experimental methods. The impact of different design changes and flow parameters can be studied quickly to accelerate the product design and optimization process. The results of design iterations can be studied thoroughly in post processing to find the most effective and cleanest brake system. This allows the user to design a flawless braking system in the early design stages and helps to comprehensively evaluate multiple design goals simultaneously, such as brake cooling, weight reduction, and fuel efficiency.
Solution steps
The first step is to prepare the model for simulation. In this stage, the brake geometry is cleaned up and the assembly is meshed taking into account the feature details. This helps to ensure an accurate fluid flow analysis through all the parts.
Once the model is ready, the simulation scenario template is set up using the brake-cooling template, which is part of our product library. The brake-cooling template is enhanced for the brake soiling workflow – simple scripts enable us to model brake dust particles.
The solution can be run on a HPC cluster or the SIMULIA cloud with parallel processing enabled – this helps to reduce the simulation turnaround time. Also, a coarse-to-fine simulation seeding option is available for accelerating the solution convergence.
Automated post processing templates help us to produce results in the desired format, thereby reducing manual post-processing effort and time.
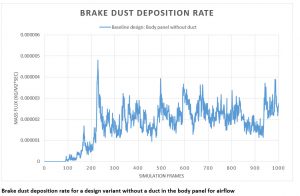
Brake dust deposition rate for a design variant without a duct in the body panel for airflow
We also studied a design variant with a duct in the body panel for airflow – this design allows air to pass through the brake assembly, which results in faster brake cooling compared to the baseline design. This resulted in a positive impact in terms of reducing the brake soiling issue.
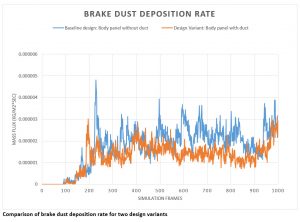
Comparison of brake dust deposition rate for two design variants
With the added duct for airflow, the brake dust deposition rate has been reduced by 50%, which is a huge improvement. This solution has provided two major advantages – better brake cooling and simultaneously keeping the rim and wheels clean. Early stage insight into the problem can help you design an efficient and effective brake system.
Interesting fact
While we were working onsite at an OEM on a vehicle program, we found that the customer had a problem with its current product line in that the wheel rims were rusting. With a little research, we discovered that the issue was due to brake dust. This launched us down the path to develop this solution to address the issue. Ever since, it has helped the OEM to analyze the brake dust flow behavior and to design clean brake systems.
See all our Transportation & Mobility solutions by visiting: https://www.3ds.com/products-services/simulia/solutions/transportation-mobility/