Advanced driver assistance systems in automobiles utilize various technologies, such as cameras, lidar, and radar, to ensure a safe and comfortable driving experience. Among these technologies, radar plays a crucial role in detecting and tracking objects. However, when integrated into the vehicle, the radar’s performance is affected by the vehicle’s body and other components in its vicinity, including the bumper, chassis, and cables etc. The material, shape, and thickness of the bumper and the scattering components surrounding the sensor significantly influence the radar’s performance. Thus, investigating the sensor’s performance degradation when integrated into the vehicle presents a valuable opportunity. Validating the radar in a virtual environment, simulating realistic conditions before the actual prototype is ready, facilitates the early incorporation of design changes in the product development stages and save costs as illustrated below:
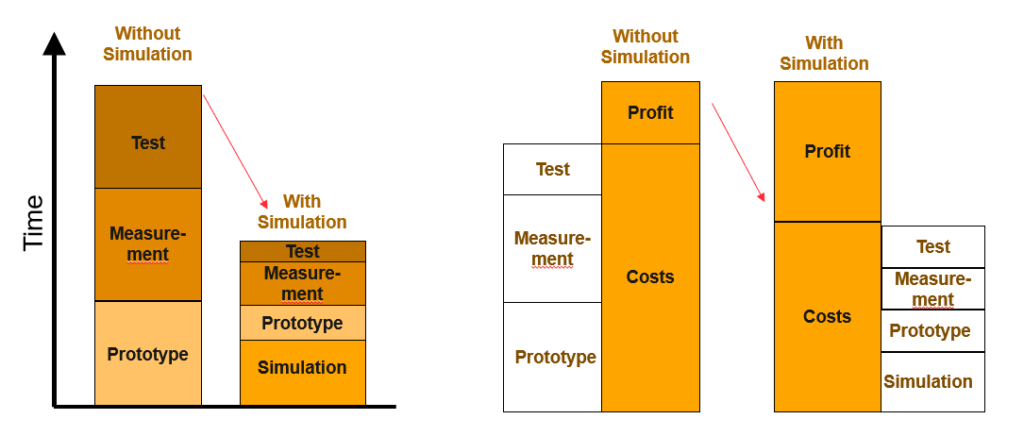
Simulations for integrating radar into vehicles can be segmented into various stages, each delving deeper into the investigation. The initial stage involves optimizing the antenna and sensor components. CST Studio Suite empowers us to meticulously scrutinize the radiation characteristics of antenna elements, thereby curtailing the necessity for constructing and testing numerous prototypes in a laboratory setting. Various facets of sensor development, encompass the following :
- Crafting the layout of the feeding structure and radiating elements on a multi-layer RF board.
- Establishing a matching radome, while navigating through the intricacies of a comprehensive sensor model, which includes the RF board, radome, packaging, data connector, case, and other components.
The Time Domain – FIT technique in CST is a powerful and versatile solver that simulates the broadband applications in a single run and thus is a remarkably efficient in addressing the aforementioned challenges in sensor development.
The next stage focuses on optimization of bumper in front of the sensor. Bumpers exhibit a complex, multi-layered structure, featuring plastic as the base layer, followed by primer and paint coating. With thicknesses in the order of millimeters, comparable to the operating wavelength of the radar sensor, these bumpers become pivotal in shaping the sensor’s performance. The presence of the bumper introduces challenges as radio waves undergo reflection, refraction, and scattering, resulting in the degradation of radar sensor performance. Effectively mitigating the impact of the bumper on the radar sensor presents a significant challenge. The optimization of the shape, material, and position of the bumper represents the primary parameters targeted to attain optimal mounting performance. The impact of these variables on radar performance is elucidated below:
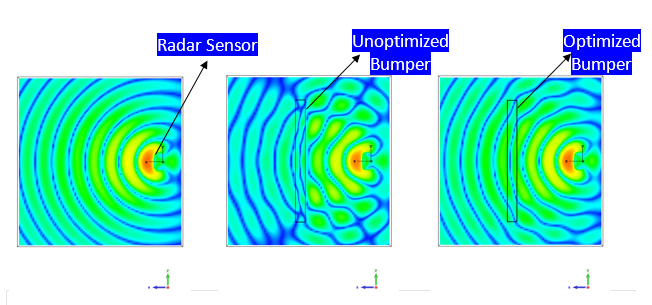
In the subsequent stage, attention is directed towards the chassis parts surrounding the sensor, aiming to discern their impact on radar performance, in conjunction with the bumper. The illustration below demonstrates that at steeper angles, the interaction between the electromagnetic waves emitted from the sensor and the chassis becomes more pronounced.
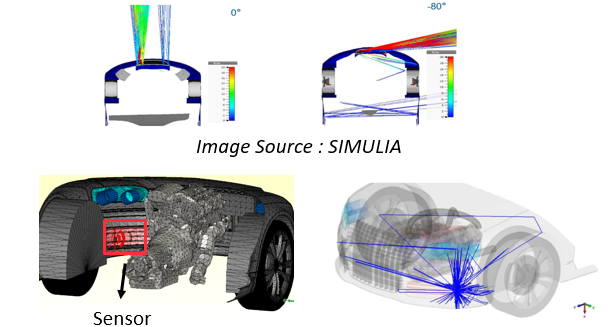
The multiple reflections occurring among the sensor, chassis, and bumper result in inaccurate target estimations, leading to false alarms:
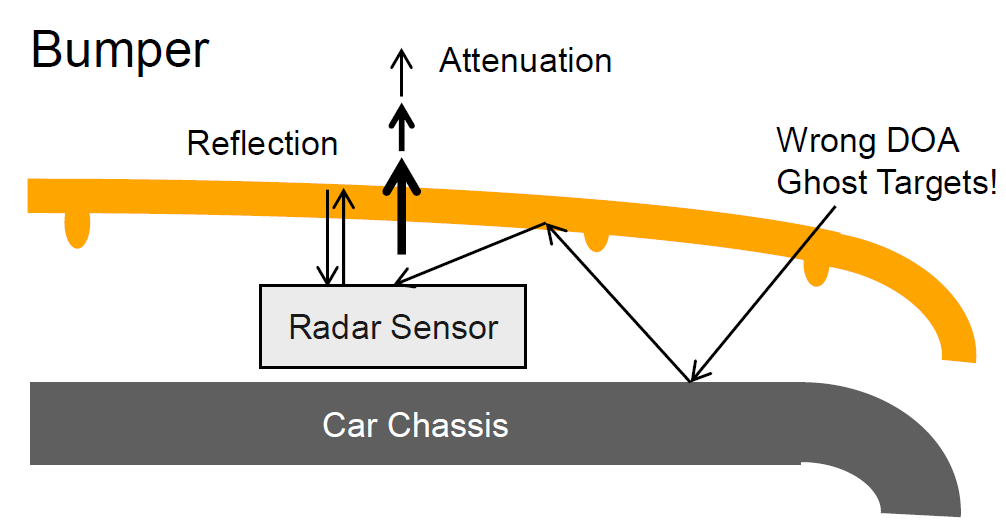
The primary challenge lies in establishing a tool chain for simulations at this high frequency for an enormous model (of sensor + chassis) and achieving the optimal balance between simulation accuracy and speed. This is illustrated by means of the following example:
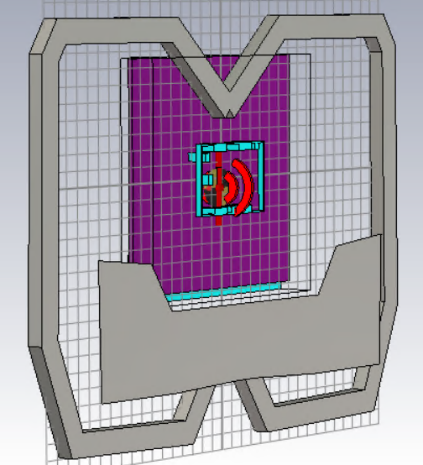
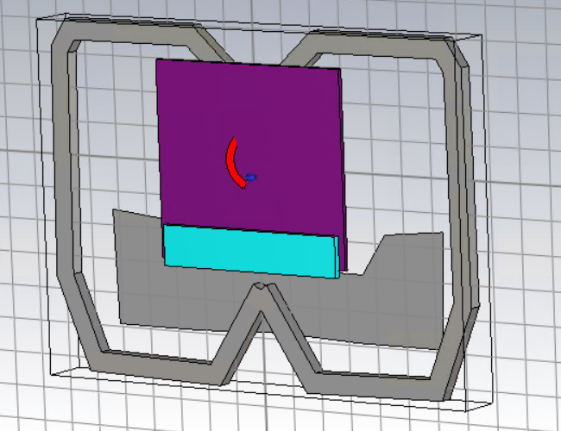
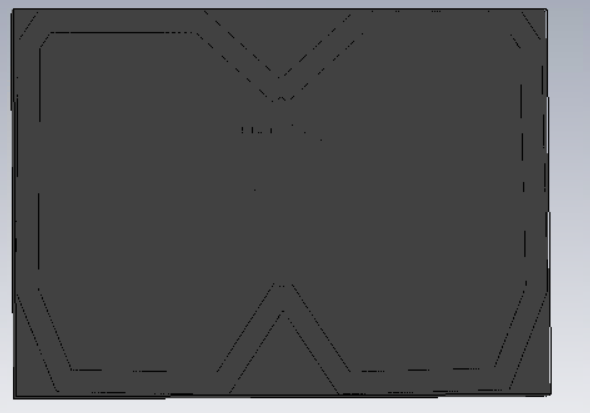
The sensor and chassis model are discretized using the Time Domain solver in CST. While the Full physics solver offers high accuracy, the mesh elements reach approximately 3 billion, resulting in excessively high computational demands. Consequently, simulation times extend drastically, averaging around 14 days per project. CST’s hybridization feature facilitates the efficient analysis of such challenges by amalgamating the strengths of various solvers to strike a balance between accuracy and computational resources within the time constraints. For the current problem, the optimal approach entails hybridizing the Time Domain solver and the A solver, as illustrated below:
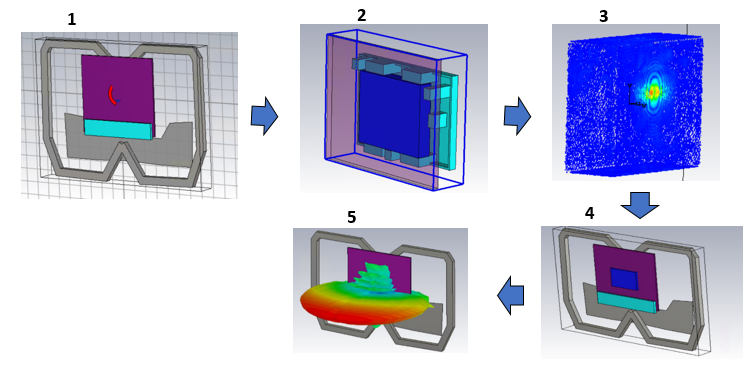
In this approach, the sensor and adjacent components are analyzed using the Full Physics solver (Time domain), given the high accuracy required due to resonant effects inherent in the physics. Step 3 involves extracting the near fields of the sensor and adjacent setup, which are then utilized as sources in step 4. The remaining portions of the chassis are solved using the A solver, prioritizing speed over accuracy. This hybrid method effectively combines the advantages of both approaches, offering the best of both worlds. As demonstrated below, this approach significantly reduces simulation resources and time:
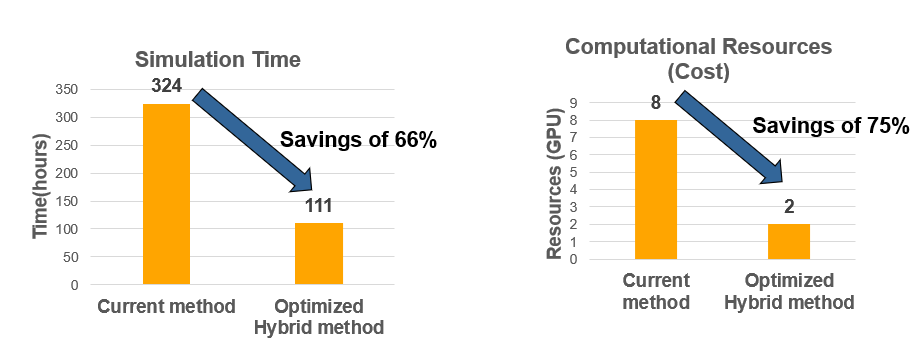
The accuracy of various simulation methods compared to measurements is depicted below. It’s evident that the hybrid method closely aligns with Full-wave methods and measurements, rendering it well-suited for vehicle integration applications:
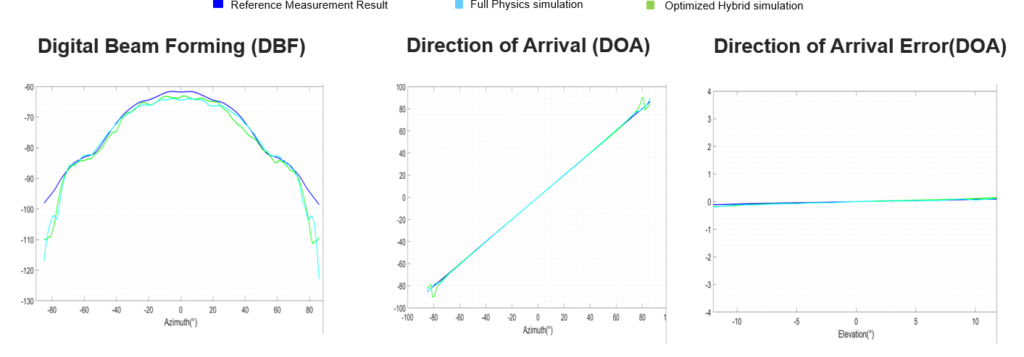
Future strategies in vehicle integration simulation entail leveraging the 3DEXPERIENCE platform to seamlessly integrate modeling and simulation processes. A unified platform integrates various aspects of product development, enabling users to develop and validate product designs collaboratively. In the realm of vehicle integration simulation, CAD optimization plays a critical role in the workflow. Currently, CATIA is employed for CAD optimization, which is conducted independently of radar RF simulation. The primary challenge lies in the time and effort required for optimizing and converting CAD data from CATIA into a compatible format suitable for CST Studio.

A unified modelling and simulation platform like 3DEXPERIENCE platform could integrate the CAD optimization process in CATIA with the radar placement workflow performed in CST Studio to massively cut down the simulation, modelling efforts and time thus optimizing the radar integration simulation process further.
About the Author
Yadhukrishnan M K3, Technical Lead – RF simulation has been working in Continental AG since 2020. He is responsible for leading the planning and execution of major RF Simulation activities (focused on autonomous driving) according to customer/internal milestones with required scope and quality. He is involved in key projects covering aspects of – Vehicle Integration Simulation, EMI/EMC, Antenna/sensor development, radar-based autonomous driving functions & scenario simulation.
He has quite a wide experience in RF modeling and simulation approaches/tools. During his career of 7+ years, he has been involved in mitigating RF & EMI/EMC challenges in product development & working with clients across Electronics, aerospace, automotive, defense, research, etc. industry domains. He holds a Master of Engineering Degree in the domain of Electromagnetics and RF/Antenna Engineering.
Yadhu is also a 2023 SIMULIA Champion.
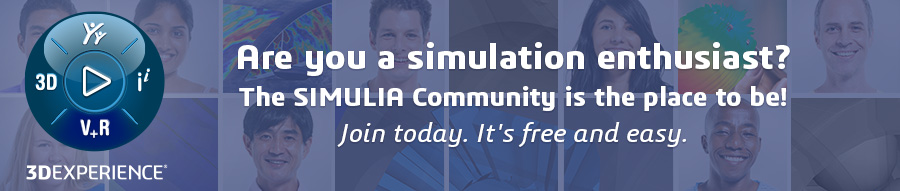
Interested in the latest in simulation? Looking for advice and best practices? Want to discuss simulation with fellow users and Dassault Systèmes experts? The SIMULIA Community is the place to find the latest resources for SIMULIA software and to collaborate with other users. The key that unlocks the door of innovative thinking and knowledge building, the SIMULIA Community provides you with the tools you need to expand your knowledge, whenever and wherever.