Registration is now open for the 3DEXPERIENCE Modeling and Simulation Virtual Conference (ModSim) on November 17-18, 2020. This global conference will inspire users to design and innovate the next generation of products by offering learning opportunities through user presentations on industry applications, product and technology updates. Below is an interview with one of the academic speakers, Mohd Nasir Tamin, giving insight on what he will present at the conference. A link to the full presentation can be found here.
What is the title of your presentation?
Our presentation is on Damage Mechanics Approach to Fatigue Life Prediction of Steel Wire Ropes under Fretting Fatigue Conditions.
We propose a new damage-based approach to reliability prediction of the steel wire ropes. The methodology is based on two aspects. One is the computed local stress field in the critical trellis contact zone of a stranded wire rope, by the Abaqus/Standard. The other is the measured degradation of the Young’s modulus of the drawn steel wires, due to the fatigue cycles. This approach allows for addressing the different damage mechanisms, namely, fretting fatigue, fretting wear, and corrosion fatigue, dominating the fracture scene of the stranded wire ropes.
The model features:
- The computed incremental fretting fatigue damage using Lemitaire’s damage equations for quasi-brittle material, introduced through Subroutine UMAT.
- Input material properties and damage model parameters are extracted from the test data on drawn steel wire specimens.
- The fretting fatigue damage mechanism is captured through the initiation and subsequent damage evolution at the critical / damaged integration points. The collection of separated material points is treated as the propagating fretting fatigue crack in the drawn steel wires of the wire rope.
- The load-cycle block method is designed to address the associated computational efficiency of the fatigue life calculations.
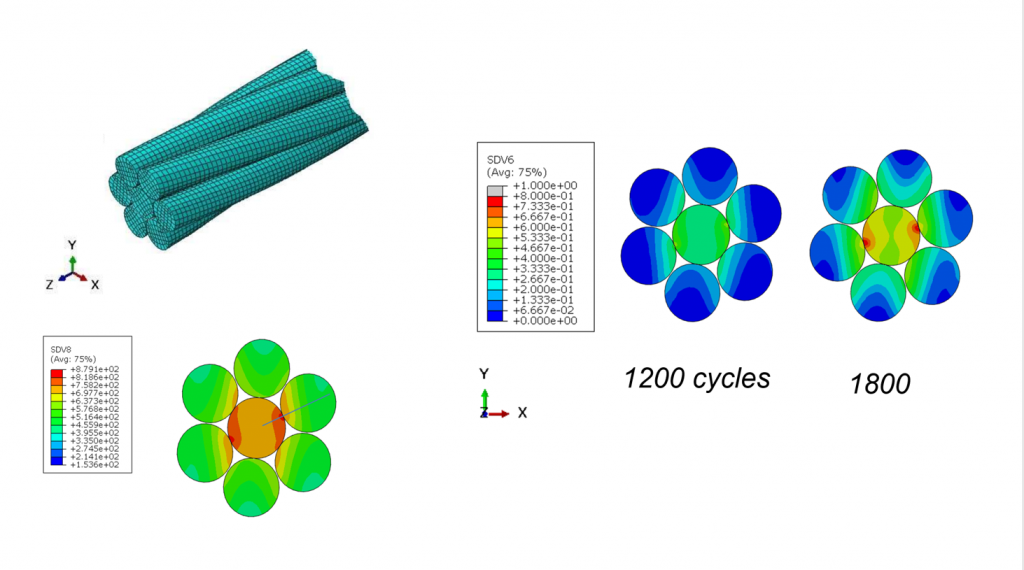
Please describe why you chose this topic for your project. Why does this workflow need to be analyzed?
The topic is based on industry (Kiswire R&D) quest for an accurate predictive tool for the reliability assessment and generating the much-needed reliability data of their newly-designed steel wire ropes. The conventional S-N approach, coupled with the classical Modified Goodman’s equations and/or SWT parameters to account for the mean stress effect are phenomenological, and require extensive fatigue test data set for each steel wire rope design. Yet, the approach does not account for the different operating damage and/or failure mechanisms.
Why is your presentation relevant to this event’s audience? What are three main takeaways the audience can expect at the conclusion of your presentation?
We illustrate, through our proposed approach on how to capitalize the availability of the FEA code, such as Abaqus/Standard, with appropriate physical-based material damage model, and at a reasonable computing resources, to adequately capture the mechanics of the deformation and the fracture processes of the steel wire ropes.
The takeaways include:
- Damage mechanics-based modeling of materials enable us to simulate the continuous deformation-to-fracture processes of materials, with integrated failure mechanisms.
- The cycle block method, based on the material property degradation curve, is an alternate approach in addressing the computational efficiency when predicting the structural reliability with the large number of fatigue cycles.
- The FE simulation is an excellent thinking tool in the understanding of the mechanics of the materials and the mechanism of fracture.
What do you see are the benefits of someone listening to your presentation?
The subject are of structural fatigue remains complex and increasingly challenging, particularly in the reliability assessment of the material and/or structure. This presentation describes a structured working framework, capitalizing the (Abaqus) FEA software, available computing resources, analytical (damage and constitutive) models, and material data requirements to address such challenge. The framework could be repeated or duplicated for other design of engineering structures.
What were the advantages of using simulation in your project?
FE simulation is treated as the primary driver in pushing the available theoretical models for addressing numerous practical issues. In our case, Lemaitre’s damage equations to quantify the reliability of the newly-designed steel wire ropes.
Why did you choose SIMULIA over other simulation products?
SIMULIA (in particular, the Abaqus Unified FEA software) is a large and general purpose FEA tool, with excellent interactive facilities for users. Subroutine UMAT is a well-structured interface for introducing new constitutive and damage-based material models.
Do you feel that learning simulation skills in University will provide you with an advantage in your career? Please explain.
Certainly. Engineering simulation, in particular the FEA, is a much-needed tool for basic (elastic) structural and component design works. However, this advanced tool requires understanding of the underlying physical phenomenon being simulated. The simulation skills (especially the programming skill) is an essential requirement when addressing the complex, multi-physics system within the Industrial Revolution (IR4.0) framework.
Prof. Mohd Nasir Tamin earned his doctoral degree in Mechanical Engineering and Applied Mechanics from the University of Rhode Island, USA in 1997. He has been with the Faculty of Mechanical Engineering, Universiti Teknologi Malaysia since 1984. Prof. Tamin’s research team activities focus on the development of constitutive and damage models for ductile metals and fibrous composite laminates. He leads his research team on few successful research collaborations with industries including Intel Technology on the development of a validated methodology for reliability prediction of microelectronic BGA packages and through-silicon via (TSV) interconnects, with Kiswire (Korea) for fatigue life improvement of steel wire ropes, and with Airbus and Aerospace Malaysia Innovation Center (AMIC) for damage detection in FRP composite laminates using the digital image correlation technique (DIC).
SIMULIA offers an advanced simulation product portfolio, including Abaqus, Isight, fe-safe, Tosca, Simpoe-Mold, SIMPACK, CST Studio Suite, XFlow, PowerFLOW and more. The SIMULIA Community is the place to find the latest resources for SIMULIA software and to collaborate with other users. The key that unlocks the door of innovative thinking and knowledge building, the SIMULIA Community provides you with the tools you need to expand your knowledge, whenever and wherever.