Whether it’s an automotive component or a medical device, reducing the weight of a manufactured tool or part can significantly improve its performance. In the past, there were only a limited number of approaches manufacturers could take to reduce the weight of a part without affecting its function, but with recent advancements in additive manufacturing or 3D printing, a new option has become available. Lattice structures are extremely lightweight designs that reduce the internal mass of a component, improving strength-to-weight ratio.
A lattice is a repeated arrangement of unit cells, which may be a variety of sizes or shapes. Lattice structures provide internal support while reducing material used, thus creating a much more lightweight part that is as robust as a traditionally manufactured, solid component. Additive manufacturing has the ability to create unconventional shapes that other manufacturing methods cannot manage, including lattice structures. Simulation allows the engineer to optimize the interior lattice structure of a component, without affecting the exterior functional structures.
In a Dassault Systèmes e-seminar entitled “Lattice Optimization and Process Simulation of a Turbine Blade,” a basic turbine blade was used to demonstrate how lattice structures can be incorporated to lightweight a part. In this case study, the 3DEXPERIENCE platform played a large role in the entire process, beginning with the Part Design app, which generated the internal cavity and lattice structure. From the lattice structure design, a representative Abaqus input file containing all of the beam element connectivity, plus the beam profile and beam section properties, was also created.
The unit cells of the lattice were designed in a star pattern, with beams that were 4mm long and 0.4mm in radius. The Mechanical Scenario app was used to generate the model of the turbine blade, and a Cobalt Chromium alloy material model was applied to the geometry. A static simulation was then run using the finite element model, to ensure proper connectivity and load transfer between the solid and lattice regions.
The lattice region was then optimized using the Tosca Structure sizing capability accessed from the Process Composer app. The workflow used a 3DEXPERIENCE utility adapter to first generate an Abaqus input file from the static simulation. Next, using the Tosca Structure sizing module, the beam radii in the model were optimized to redistribute the existing weight to maximize the stiffness of the structure. The optimization results were then converted to a new lattice structure geometry using a Python script, finally the Additive Manufacturing Scenario app was used to simulate the additive manufacturing process of the optimized structure.
The simulation revealed the residual stresses and distortions in the build setup after manufacturing, with higher distortions near the primary support region, indicating that more supports were needed. The stresses in the part and the supports were otherwise uniformly distributed, suggesting that there were no regions of high stress concentration that could cause build failure.
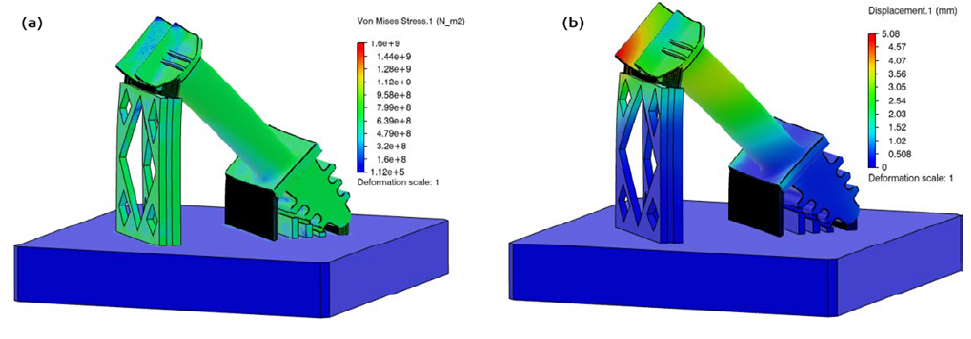
While future work is still needed, including experimentation with different lattice and support structures, the process demonstrated that Powder Bed Fusion additive manufacturing could feasibly be used to create a lattice-optimized turbine blade. If you’d like to learn more about the process in detail, the e-seminar is available here in the SIMULIA Community.
SIMULIA offers an advanced simulation product portfolio, including Abaqus, Isight, fe-safe, Tosca, Simpoe-Mold, SIMPACK, CST Studio Suite, XFlow, PowerFLOW and more. The SIMULIA Community is the place to find the latest resources for SIMULIA software and to collaborate with other users. The key that unlocks the door of innovative thinking and knowledge building, the SIMULIA Learning Community provides you with the tools you need to expand your knowledge, whenever and wherever.