We’re getting to know Exa’s PowerFLOW suite and welcoming content about simulation technologies that go beyond materials to discuss fluids, electromagnetics, etc. Learn how simulation-driven design will power tomorrow’s technologies.
Whether it’s the latest driver-assist technology, the most comfortable cabin, or the best fuel economy, consumers crave the experience vehicles can offer as much as their practicality, style and value. Recent trends in electrification and automation heighten the competition among OEMs, who must advance these new technologies faster than the competition – and with the highest degree of quality and reliability – or risk being left behind.
This means OEMs can’t rely on traditional methods of building and testing physical prototypes. Not only is the time and expense of physical testing too great to risk on every new idea, the level of maturity required in a product’s development to advance to physical testing means that most of the design is too difficult to change without even more time and expense. The competitive demands to launch the best innovations first simply outstrip the ability of physical prototype testing to keep up.
Digital simulation in Exa’s PowerFLOW suite uniquely applies a complete range of real-world conditions to 3D geometry by leveraging cutting edge, proprietary physics-based methodologies. Simulation is used early in the product’s lifecycle when designs are still in work and changes are easier to make. Highly visual simulation results in PowerFLOW are easily accessible to a number of multidisciplinary engineering teams and stakeholders – even those not skilled in CFD or simulation. Engineering teams can predict the potential of even the most dramatic new design ideas sooner, gather key insights to improve their performance, and communicate across disciplines to integrate new designs with other improvements on a systems level, to be sure all program targets are met.
The latest advancements in PowerFLOW – released this February with version 5.5 – advance the way automotive OEMs power innovations in autonomous systems, cabin comfort, and vehicle efficiency, while further improving the way multidisciplinary engineering teams leverage key simulation results. Let’s look at each of these features in turn:
Powering Innovations in Autonomy
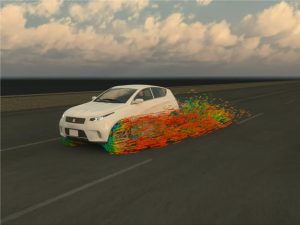
Today’s autonomous vehicle systems – which help drivers do everything from parking, to avoiding collisions, to safeguarding pedestrians – rely on cameras and sensors to function properly. If these devices are obscured by dirt, dust or water, they won’t work. And tomorrow’s fully autonomous vehicles will rely even more heavily on them, which is why engineering teams that can solve the challenge of keeping driver-assist cameras and sensors clean will lead the race to tomorrow’s fully driverless vehicles.
Building on past features in PowerFLOW that simulate the effects of on-road dirt, dust, and water on vehicles, PowerFLOW 5.5 introduces new tracking features to visualize the interactions between particles and airflow. This helps to identify upstream sources of vehicle soiling – especially in places critical to cameras and sensors – helping engineers to improve their placement and to make subtle or significant changes to the vehicle’s shape that can help prevent the upstream effects causing soiling there in the first place. And with support for a new post-processing capability that can visualize and track particles using already-completed aerodynamics simulations, PowerFLOW 5.5 enables even earlier, lower-cost predictions of these effects to help engineers predict the outcome of a full soiling simulation.
Powering Innovations in Efficiency
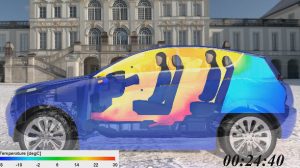
With the drive to a greener future, many of the world’s governments are adding regulations and penalties for vehicle fuel economy across fleets – and many automakers are vowing to follow suit and reducing or outright eliminating internal combustion engines (ICEs) over the course of the next several decades. But ICEs generate so much of the warmth that keeps cabins tolerable in the winter that removing them increases demands on HVAC system energy consumption – increasing the load on batteries and potentially reducing vehicle range in the winter months.
While OEMs must balance the contradictory demands of consumer comfort and vehicle range today, tomorrow’s driverless future will only increase the focus on HVAC design. The potential to re-imagine cabins for a driverless experience promises a newly blank canvas for HVAC system design while simultaneously increasing passengers’ focus on vehicle comfort, as the need to focus on the road slowly but surely disappears.
PowerFLOW 5.5 offers new technologies to understand the experience of human passengers during a cabin comfort simulation, while solving for both time-to-comfort and HVAC system efficiency. By helping to ensure that optimal human thermal sensation is achieved in the target timeframe during cool-down or warm-up, while calculating for any potential energy losses throughout the system, simulation in PowerFLOW 5.5 is supporting OEMs who seek to identify new opportunities for vehicle efficiency by reducing the energy expenditure of the HVAC system while offering the same – or better – thermal experience for the vehicle’s occupants.
Equipping Today’s Teams for Tomorrow’s Innovations
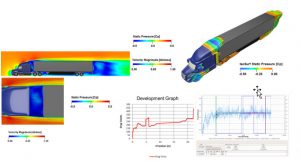
High-performing teams that can innovate quickly – and confidently – require simulation solutions that offer timely, easy-to-understand results predicting the performance of their new designs. That’s why advances in PowerFLOW 5.5 focus on improving the speed, accuracy, and efficiency of teams, while reducing hardware requirements to solve larger, more complex problems. And, it’s why PowerFLOW 5.5 now supports a comprehensive library of templates to accelerate simulation set-up and results post-processing across all mature solutions throughout aerodynamics, thermal, and aeroacoustics applications – including brake cooling, underhood cooling, greenhouse wind noise, realistic wind, treaded tires, and wheel spray soiling.
With a more intuitive, automated process, faster performance predictions, and more efficient and standardized results visualization, the user experience is improved from case set-up through post-processing. Organizations can better standardize the way they compare performance across designs, more easily ramp up new teams in the use of simulation, and even equip stakeholders and non-engineers with the results of CFD simulations to better understand the performance of their newest design innovations.