This post originally appeared in the 3D Perspectives Blog.
Early product failures and product recalls are very costly. They result in loss of revenue, litigation, and brand devaluation among others. Hardware recalls are often costlier than software recalls as software patches can be easily downloaded and installed once flaws come to light.
Recalls and early product failures tend to happen over and over again. Why?
The answer is because engineering teams are constantly under the gun to improve product performance, reduce form factors, and reduce time to market, all while cutting costs. In order to mitigate risk, engineers need to develop a deeper understanding of the product behavior under real operating conditions and quickly evaluate design trade-offs based on overall system behavior.
Physical tests provide an excellent means to understand product behavior. However, physical testing is expensive and time-consuming. Simulation provides a cheaper and faster alternative to physical tests. It is critical to strike the right balance between physical tests and simulation during product development. In order to get the maximum bang for your buck, simulations should be deployed starting early in the design cycle when physical prototypes are not available and the design is not fully developed. The earlier you find flaws, the earlier you can fix them.
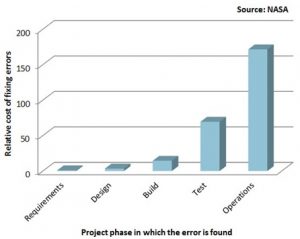
Graph: Relative cost of fixing errors in embedded systems
Since the cost of fixing flaws grows exponentially through the design cycle, identifying and fixing design flaws early in the design cycle is super critical. Not all simulation tools are created equal. You don’t need any answer. You need the right answer. For that, you need simulation tools that most closely depict reality. And you need answers fast. Hence you need product testing and validation tools with industry leading physics and solver technology. Those will make you obtain accurate solutions faster in order to help you improve product design, ensure product reliability and reduce time to market. Accurate depiction of material behavior and physics of failure are essential to obtaining realistic results. Such capabilities are critical in predicting the behavior of materials such as glass, adhesives, and polymers that have a high propensity for damage.
Consumer electronic products, especially mobile and portable devices such as smartphones, tablets and laptops, are subjected to a variety of operating conditions. The devices need to be designed to protect them from damage. Engineers need to ensure that “portable” doesn’t mean “breakable.” The challenge is to design a light-weight product that can withstand not just the loading cycles associated with regular usage, but also abusive loading scenarios that are encountered less frequently (According to surveys and insurance claim statistics, drop and water damage constitute the two most frequent causes of damage for mobile devices).
Simulation should be employed at the ideation, product development, and failure analysis stages in order to improve product quality and reduce time to market. Refer to the case study is this e-book to learn how a leading manufacturer of consumer electronics used simulation to improve the keystroke feel and enhance frame rigidity while reducing weight.
While drop during daily usage is a concern for mobile devices, transportation drops are the main concern for office equipment. Engineers are faced with the challenge of identifying the structural members that are most susceptible to damage and then improve their damage resistance while reducing the overall weight of the structure. Here’s how a leading manufacturer of office equipment designed a low cost printer that can withstand a series of transportation drop tests.
The examples above provide a snapshot of applications leveraging realistic simulation technology to successfully improve product durability while satisfying other constraints such as weight and cost. Learn more about how you can leverage this technology to improve your electronic product design. Read our e-Book, “Improving Product Performance and Reliability through Multiphysics Simulation.”