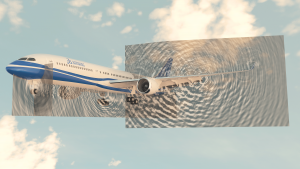
The noise produced by aircraft during take-off and landing is a significant obstacle to aviation growth and a cause of resistance from the communities around airports. Noise certification levels will become much stricter over the next decade and an increasing number of jurisdictions are placing even tougher noise constraints on airports effectively limiting the number of flights per hour, operating hours, and the size of aircraft that are allowed. Quieter aircraft will be less affected by these noise restrictions, opening up new opportunities for airlines while improving airports’ relationships with the surrounding community.
There are several sources of noise on aircraft, both tonal (around a single frequency) and broadband (filling the audible spectrum). Engine noise caused by the fan and jet are still the dominant source of noise during take-off, but turbulent airflow around deployed components such as the landing gear, slats and flaps are equally important, especially during landing.
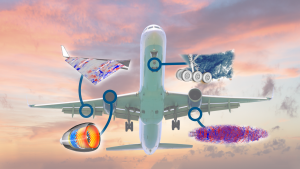
Because small geometry details make a difference to an aircraft’s sound signature, accurate noise prediction requires the full geometric details of all aircraft components. The combination of Dassault Systèmes software on the 3DEXPERIENCE® platform allows engineers to perform noise assessment of the virtual aircraft without a physical prototype, using the highest geometric fidelity to include all potential noise sources.
SIMULIA fluids solutions provide Lattice Boltzmann computational fluid dynamics (CFD) solvers that are able to simulate turbulence induced noise as well as the propagation of noise to the ground. This state-of-the-art solver technology, which has been validated in cooperation with NASA over the past 10 years, can simulate acoustic sources and noise signatures on the ground more accurately than traditional CFD technologies.
Engineers must first prepare the geometry, which can be done using SIMULIA PowerCASE. PowerCASE includes templates that can set up the simulation to mimic certification requirements based on targets. SIMULIA PowerFLOW, a computational fluid dynamics tool, then calculates the airflow and resulting noise around the aircraft model. Next, during post processing, engineers calculate far field noise analysis and Effective Perceived Noise Level (EPNL), and produce beamforming maps that can identify and localize noise sources. The engineers can then develop mitigation concepts and modify geometry if needed.
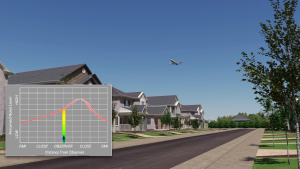
SIMULIA solutions allow the users to identify the exact location of noise sources and provide insight into how design adjustments affect noise output and how to best optimize prototypes already at design stage and before a physical model is built. In addition to simulating individual components responsible for noise generation users can analyze the interactions of these components on the aircraft, and generate the community noise signature of the entire aircraft. Customers using SIMULIA fluid solutions to improve the noise characteristics of landing gears and flaps have been able to achieve a 3 dB reduction over a wide frequency range, equivalent to a 50 % decrease in noise intensity.
In combination with SIMULIA’s Aircraft Aerodynamic Performance offering, noise abatement strategies can also be analyzed from an aerodynamic perspective to ensure that the aircraft performance is not compromised.
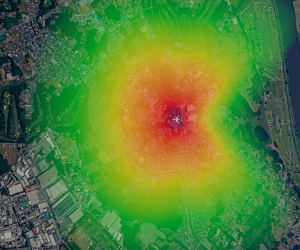
With tougher noise certification levels and airport restrictions due to noise, aircraft manufacturers will need simulation methods that are able to reliably assess noise metrics early in the design process. By using SIMULIA’s unique CFD tools for aeroacoustic simulations, engineers can pinpoint potential noise sources and make design changes before building a physical prototype. This can reduce the risk of noise problems emerging during flight test and certification, avoiding potential delays and reducing overall costs. This is a major assistance for airframe manufacturers looking to produce quieter aircraft that are more attractive to both airlines and the communities surrounding the airports. Learn more about SIMULIA’s Aircraft Community Noise solutions here.
Want to learn more about SIMULIA’s simulation solutions? Visit our website.