In the T&M and IE industries, engine assembly simulation is the centerpiece of the Industry Process of Internal Combustion Engine (ICE) Engineering. Structural simulations are used for validating new designs to ensure that the structures of an ICE can sustain high thermal-mechanical loads during working cycles as well as predicting the fatigue life. In this blog post, we would like to introduce High-Fidelity Simulation with Large Models (HiFi Simulation), an out-of-the-box (OOTB) solution we recently developed based on the 3DEXEPERIENCE platform, and discuss its application to the ICE Engineering.
We are in the Age of EVs. Why should we still care about ICE?
With the rapid rise of Electric Vehicles (EVs), everybody is talking about BEV now, and even HEV and PHEV seem like yesterday’s news. You may wonder why we are still talking about ICE. The reality is there will still be a few years before EVs take over the market (see a 2017 FleetCarma market report).
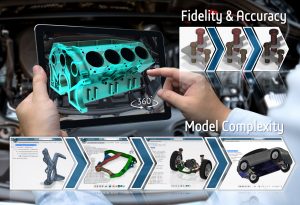
More importantly, because of the market entry of EVs, the competition of technology innovations to make ICE more fuel-efficient and environment-friendly is fiercer than ever. Some of the design and simulation technologies used for ICE can also be applied to developing EVs, as they both face challenges in heat management, durability, and NVH. Therefore, ICE engineering is still important and relevant today.
What is HiFi Simulation? And, what are the benefits?
HiFi Simulation is an End-to-End solution fully based on the 3DEXEPERIENCE platform. With this OOTB solution, engineers can start from CATIA Knowledge-based Design and skip the tedious and most time-consuming tasks of model abstraction and mesh editing. A design change can easily be validated using design geometry and refined mesh updated automatically to achieve High Fidelity, High Accuracy, and Low Costs. Light-weight 3DPlay and online 3DDashboard allow gigabytes of simulation results to be easily shared on computers and tablets with anyone from anywhere at any time. Including Design, Simulation, Manufacturing, and Collaboration on the Single Digital Platform of 3DEXPERIENCE, users will be able to best maintain the Digital Continuity and take the Model-based Data-driven approach to seek Single Source of Truth.
Who will benefit from adopting this new solution and how?
We think Product Engineers and Simulation Specialists can both benefit from this solution.
Today, for most automotive OEMs, engine assembly structural simulations are carried out mainly by Simulation Specialists, who often have to spend days or even weeks simplifying the model geometry (for example, manually removing holes, fillets, and draft angles) to reduce the model size. Model abstractions require a certain level of simulation knowledge and expertise that Design Engineers often lack and would also introduce inherited modeling errors, lowering the fidelity and accuracy of the simulation. In the To-Be process, because of HiFi Simulation, little or no model abstraction is necessary, and therefore, some simulation tasks can be transferred to Design Engineers. In addition, 3DEXPERIENCE provides OOTB tools such as Assistant, Vertical Applications, and Engineering Templates, which help democratize simulations and automate the development processes.
With HiFi Simulation, Simulation Specialists can not only focus on more expertise-demanding simulation tasks but also possibly increase the model size from 1 million degrees of freedom (DOFs) to approximately 100 million DOFs to include more components and larger assemblies in their simulations. (The number of DOFs is a numerical indication for model scales. A free node in the 3D space can have six DOFs — three translations and three rotations).
What are the unique values that HiFi Simulation can provide for the ICE Engineering?
HiFi Simulation is fully based on 3DEXEPERIENCE, offering the best industry experiences with High-Performance Modeling & Meshing, High-Performance Computing, and High-Performance Visualization capabilities. For ICE Engineering, structural simulations often include advanced modeling features, such as contact, gasket, and bolt pre-tension, which often pose challenges to numerical convergence. HiFi Simulation can effectively handle problems of large blocky structures with these advanced features and provide robust solutions with scalable performance and with relatively low costs.
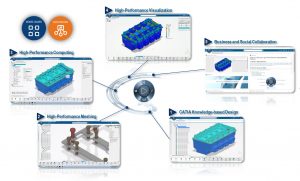
Can you elaborate on the High Performance aspect of this solution?
With this end-to-end solution, the time spent on modeling and meshing can be significantly reduced from a few days down to a few hours. For example, creating a finite-element mesh of 125 million DOFs on 3DEXPERIENCE takes only about an hour. The High-Performance Computing capability allows solving such a large problem with 192 cores in just 3.6 hours. The High-Performance Visualization capability provides a light-weight and fast display of 3D models. For a huge result file of 50 GB, it takes just a minute or two to display the contour plots for displacement and stress fields. Customer benchmarks have shown that HiFi Simulation is ready for production deployment.
Everything sounds great. What should I do to try it out?
Right now, we are looking for early adopters. If you have requests for POC and benchmarking, please contact Yunfei Shi (yunfei.SHI@3ds.com). We look forward to working with you!