During my last Academic Tour to the United Arab Emirates (UAE) in February 2019, I had the chance to meet a talented and passionate student team that participates to the Global Hybrid Electric Challenge in the UAE (GHEC-UAE). GHEC is a hands-on educational program for institutions of higher learning with engineering, science, technology and business management programs. Student teams use their engineering design skills to build full-size electric and hybrid cars.
I met Melad Fahed, a Mechanical Engineer (Master of Science) from Khalifa University in Abu Dhabi. He led a team of motivated students for several consecutive years to compete in the GHEC. His teammates Khaled Al Khoujah, Master of Science in Mechanical Engineering at Khalifa University, and Abdula Fawzy Saleem, Electrical and Computer Engineering undergraduate, have also been a part of the team for the last several years.
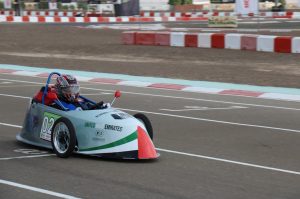
Please briefly introduce yourself and your education background?
Melad Fahed, completed B.Sc. and M.Sc. in Mechanical Engineering from Khalifa University, specializing in FE. Led a team of motivated students for several consecutive years to participate in the GHEC.
Khaled Al Khoujah, Graduate Student in KU, been a part of the team for the past 4 years, participated in several GHECs. B.Sc. in Mechanical Engineering and Currently M.Sc. in Mechanical Engineering.
Abdula Fawzy Saleem, a senior electrical and computer engineering undergraduate student at Khalifa University of Science and Technology. Abdula is interested in 3D printing and IoT devices as well as CAD modeling. Currently working on a senior year design project that involves the design and control of an electric system of a hybrid electric vehicle.
The main purpose of this student competition is to travel the longest distance in a fixed amount of time and with a fixed amount of fuel and stored electrical energy.
The car is a one person racing vehicle that runs on battery power in parallel with a petrol engine generator power when being charged. The GHEC organization offers a kit to all teams, composed of all major components (chassis, outer shell, motor, batteries). The engineering challenge is to assemble and integrate these parts to achieve the highest reliability and efficiency.
“My main motivation to take part of this team is that I wanted to experience being part of a racing team, as well as get hands-on experience with actual electromechanical systems,” said Melad.
The project has given the team an insight on a part of engineering that is not introduced through classroom lectures and theories, a part in which they had to relate the knowledge they had to real car racing issues and tasks.
It is not the first time the Khalifa University team competed in the Global Hybrid Electric Car Challenge. “We have always been the lead in the UAE in such competitions and we were always participating in automotive challenges and competitions.” The last race, which was held back in November 2018, is the third time the KU team has competed in the GHEC race held in UAE. The competition provides a very competitive environment for the university students to take part in, yet it still appeals to the students through their interest in racing vehicles. Through the support of Khalifa University, the team was able to participate in the competition for the previous year each time trying to make it more challenging by innovating more on the basic components and design of the vehicle. Hence, the competition never ceases to provide challenges to the KU team.
Do you collaborate with other schools?
Many teams from the UAE universities participate in the competition, including 3 teams from Khalifa University across the three different campuses. Since all three of the teams fall under one entity, the teams often find themselves in need of each other’s help, whether in terms of identifying missing components or just giving advice. Consequently, the teams usually cooperate with each other to help achieve the main goal, which is to win the competition for the name of the university. Also, it’s often a very similar situation when it comes to other universities’ teams, as there is always need of someone else’s’ spare parts or vice versa. So the team spirit and the spirit of competition never fade away, and some competitiveness still remains.
Throughout this project, the team had an initial understanding of the process of designing and building the vehicle through the ready-made available components that were purchased as a kit. That includes the vehicle chassis, electrical components, plastic shell and even the batteries. However, when further development was desired in terms of the car chassis for weight reduction, which will eventually help reduce the energy consumption, the team members knew that a better way of designing and testing was required before beginning the actual process of building the car. Hence the best way was found to be to design the chassis using a CAD software and to further simulate the possible situations of any collision through FEA. This allowed the members to carry on any necessary adjustments to the geometry on the spot whenever needed without the need of redoing any calculations again. That also meant that they could change the materials and their properties instantly and see how they would change the simulation results. The ability to do all these changes quickly helped greatly in the development and design of the new chassis. This resulted in adding reinforcements where it was found necessary as well as help understand any weakness points and potential points of failure. Furthermore, it also helped in understanding where solder joints were emphasized more and then indicating more attention required to them.
Please describe in a few sentences your simulations: the methods used, the physics, element selection etc. that helped to design the car for better performance.
The simulation conducted was an FE analysis using Abaqus to model the integrity and the strength of the chassis of the vehicle, especially since we have changed the material from carbon steel to aluminum alloy.
The basic purpose behind the simulations performed was to design and simulate the vehicle chassis to evaluate and study its geometry and strength when manufactured from different materials and alloys. Simulations were done using Abaqus (student version). The chassis simulations began with modelling the car chassis to scale using real dimensions built on a real previous version. The geometry was built using wire structure, and later profiles were assigned according to metal extrusion beams available in the market. Then meshing was done to produce sufficient results resolution, however this process was done using automatic meshing as the geometry wasn’t complex. Next, load cases where selected and simulated according to regulations listed for the race for different collision cases. The load cases include, and are not limited to side collisions, front collision and rollover.
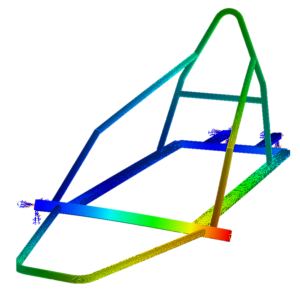
Carrying out Finite Element simulations is always challenging. Understanding the issue and the interpretation of the results of the analysis was limited to the team experience in this field.
At the first stage of the project, the team began with SolidWorks to model and simulate the chassis. Then as needs arose for more advanced structural simulation, the team decided to use Abaqus due to its availability at the Khalifa University campus and its capabilities to run all needed simulations on the chassis, as well as test any modifications made.
Do you feel that learning simulation skills in University will provide you with an advantage in your career?
Yes, it will, as all projects will be then based on science and on facts rather than trial and error, hence, an improved design, and all experimental work will be done for verification and validation purposes.
As proven by the use of FEA in this application, the same could be done for many other applications in the industry that require detailed analysis. Furthermore, the use of CAD is increasingly popular in many fields including additive manufacturing, vehicle design etc. Simulation skills and software is becoming essential for most fields of engineering and beyond. I think simulation and CAD software will become a vital skill for most engineering job positions.
What’s next for you and the team?
The team plans on taking the development of the car chassis a step further, where we are bound no more to the typical shape of the original chassis. We think that there is great potential left in developing the chassis to serve purposes of weight reduction, better weight distribution, better car handling and even customizability for wheel setup. With the help of CAD and simulation software like Abaqus and other system and topology optimization software, the team can achieve all the set goals in terms of design, as we require a precise way to develop and study the proposed design. Furthermore, CAD can also be used for other purposes on the car which include the design of all the 3D printed parts used in the vehicle (battery covers, air ducts, seat strap covers, etc.) as well as the design of the external shell of the vehicle. Also, a vital improvement for the current vehicle design will be to improve the aerodynamics of the vehicle by performing a detailed CFD analysis.
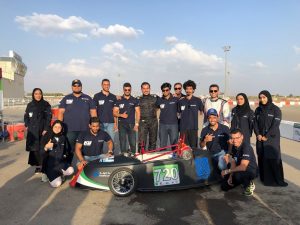
Interested in sponsoring a team like the University of Khalifa? Learn more about the Dassault Systèmes Sponsorship Program.