Challenge
Find a more efficient, accurate way to model the complex configurations and multibody dynamics of leaf spring vehicle suspension systems. Traditional approaches were intricate, challenging and resource-intensive, making it difficult to model tailor-made suspension for different vehicle programs.
Solution
Create a multibody dynamics modeling tool using the SIMULIA Simpack solution, with support from the Dassault Systèmes SIMULIA team.
Results
- Increased efficiency – simulations that used to take a day can now be done within an hour
- Fast, accurate simulation results delivered by Simpack’s robust solver
- Confidence in supporting future vehicle innovation
Sometimes old ideas are the best ones, but that doesn’t mean it’s simple to apply them to new designs. Take the leaf spring, for example. It’s one of the oldest forms of vehicle suspension, dating back to the horse-drawn carriages of 17th-century France, and it’s still in use today.
“Leaf spring is a super-old technology, but it is very cheap to make and provides a really good suspension system for vehicles,” said Ameya Apte, vehicle dynamics and load simulation engineer at General Motors (GM).
Essentially, leaf springs consist of long, flat steel plates that are curved into an arc and stacked together in a pack. A second and even a third pack might be added, each containing different shapes and quantities of leaves. That opens the door to endless configuration possibilities.
“Different leaf spring configurations provide different suspension rates for a vehicle,” Apte explained. “A smaller vehicle would need a smaller leaf pack with fewer leafs, while a larger vehicle would generally need a larger leaf pack with more leafs. Basically, the amount of load that the rear axle carries is what primarily affects the leaf design. It depends on what kind of ride and what kind of handling you want from the vehicle.”
Simulation is essential to fully analyze the different ways the leaves of each spring interact with each other.

“If you’re looking at the stresses inside a leaf, it’s practically impossible to do that in a test, but you can do it in simulation,” Apte said. “Similarly, if you want to measure the force between two leaves you can put in a load transducer, but that also modifies the model itself.”
But from a simulation modeling perspective, factoring in those multibody dynamics was a complex and resource-intensive task. As a result, modeling tailor-made leaf springs for each vehicle program could be time-consuming, error-prone and difficult to standardize as a process.
“Leaf springs have been around for hundreds of years, so people might think it’s a simple technology to model, but the opposite is true,” Apte said. “One challenge with leaf springs is that the leaves themselves articulate with the suspension, so there is friction between them that needs to be modeled. In addition, the bushings attached between the chassis and the leaf springs also have frequency-dependent properties that must be modeled.”
Carmakers typically use finite element analysis solutions to model and simulate the complex geometries, materials and physics involved in vehicle design. But for GM’s leaf springs, Apte wanted a multibody dynamics tool that would support the more efficient modeling of these complex systems. He and his team used SIMULIA technology to create the tool they needed.
“The tool that we developed allows us to make leaf springs that are standardized and tailor-made for different applications,” Apte said. “Users simply type in the parameters they want for the spring – such as the number of leaves in a pack, how they are distributed across the primary, secondary and auxiliary pack, their shapes, tapering and so on. With that information, the tool will create a model that can be used to predict vehicle dynamics performance and loads.”
Two key ingredients contributed to the tool’s success. One was the comprehensive support provided by SIMULIA’s technical, back-end and R&D teams. The other was SIMULIA Simpack – a technology for developing and simulating high-fidelity multibody systems.
Apte was particularly impressed with Simpack’s solver, which was miles ahead of other tools he had worked with.

“With Simpack, you practically do not have to modify solver parameters to get a model to run,” Apte said. “You might modify parameters to increase or reduce run times or get better fidelity in some part of the simulation, but you generally don’t need to do it to run a model. That robust solver is very useful because it allows us to look at the results, understand the physics happening behind them and then send the model out to our design engineers.”
As well as supporting more efficient leaf spring simulation, the tool also delivers accurate results, so Apte and his team can simulate with confidence. “If a simulation for leaf springs takes a day to do with FEA tools, with Simpack it can be done within an hour,” Apte said.
Looking ahead, Apte believes the solver he has in this tool will stand the test of time, even as the industry continues to evolve and new technologies emerge.
“I think the physics solvers that we have now will be supercharged, rather than eradicated, by disruptive technologies like artificial intelligence and blockchain,” Apte said. “The time it take to get a new vehicle to market has reduced significantly over the decades, and we see a potential to reduce it further with new tools. In the long term, learning these new tools and imagining a future where we can combine them to create the right applications will be a huge part of our job.”
Visit the SIMULIA Community to explore presentation replays from 2024 RUMs and more! Community to read the 2024
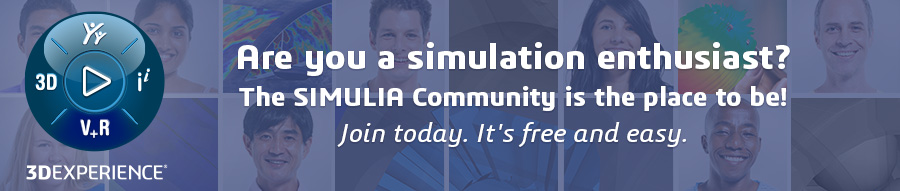
Interested in the latest in simulation? Looking for advice and best practices? Want to discuss simulation with fellow users and Dassault Systèmes experts? The SIMULIA Community is the place to find the latest resources for SIMULIA software and to collaborate with other users. The key that unlocks the door of innovative thinking and knowledge building, the SIMULIA Community provides you with the tools you need to expand your knowledge, whenever and wherever.