The automotive industry is in the middle of a metamorphosis. The industry is being challenged and pushed towards redefinition, to not only reduce the carbon footprint of its products but also to redefine the role of the driver, who can either sit and relax or drive.
450 electric vehicle (EV) models with varying levels of driver assistance will hit the road by 2025. EV sales are going to grow from 4 million in 2020 to 21 million in 2030.
All of this is happening at a frenetic pace, where the product development timeline is shrinking fast. Go-To-Market timelines for Automotive OEMs have been reduced by 71%. The reduction of the product development timeline is putting tremendous pressure on the engineering teams at OEMs and innovative startups to convert their current ideas to vehicle programs, in a very short time frame.
As a result, more than ever, automotive companies are relying heavily on the Concept phase to make the right decisions. The industry is looking for machine learning techniques to automate the methods/processes involved in the Concept Design and development process. In this blog, we explain how we reduced modeling time and made the process efficient using the machine learning language/automated approaches.
In the previous blog, Yangwook Choi, Portfolio Engineering Director – SIMULIA has clearly explained how he used reversed lumped mass-spring method and parametric optimization to make the 1D model find the optimum load-balanced structure for crash load cases. He also showed how to create and use the metamodel of correspondence between the load-carrying capacity and the cross section geometry of the structural components. The next step is to enhance the level of details, generate a 3D geometry model and increase the level of fidelity within the analysis.
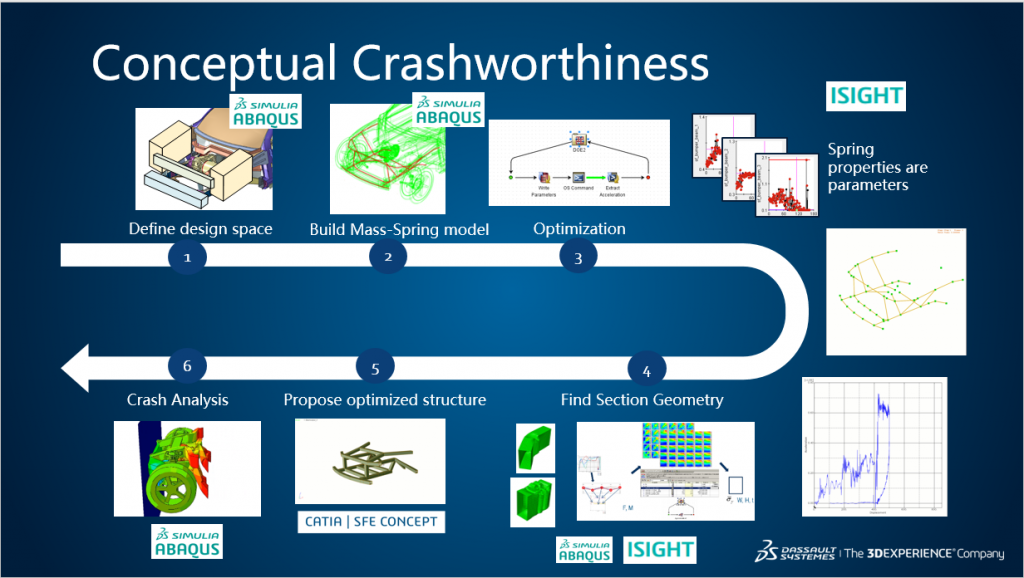
The geometry in SFE CONCEPT is implicitly parametric, which allows the user to access complex design changes with ease and fully explore the available design space. SFE CONCEPT also drastically reduces the time required for a finite element model, as all of the simulation requirements such as material & physical properties, along with connections that are assigned directly on geometric surface, are converted to a finite element model at push of a button. SFE seamlessly integrates into Isight and can generate finite element models which can be simulated in Abaqus/Standard and Abaqus/Explicit for linear static and nonlinear crash analysis.
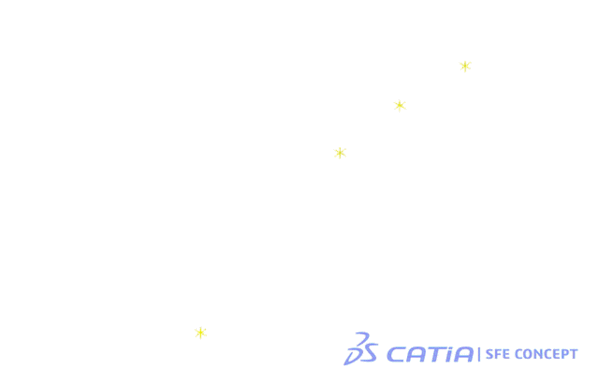
We are leveraging the optimum cross section geometry, gage and material to create a full-scale 3D parametric model in SFE CONCEPT. We developed a semi-automated process for building this 3D model; this process eliminated 70% of the manual work and reduced the overall model building time from 10 days to 3 days.
We have also created advanced automated methods wherein we can initiate an optimization process on this model; the resulting point locations, gage and section information can be easily updated into the model without investing time into model recreation process.
For more detail regarding SFE CONCEPT click here, and click here for more information about SIMULIA’s crashworthiness solutions.
SIMULIA offers an advanced simulation product portfolio, including Abaqus, Isight, fe-safe, Tosca, Simpoe-Mold, SIMPACK, CST Studio Suite, XFlow, PowerFLOW and more. The SIMULIA Community is the place to find the latest resources for SIMULIA software and to collaborate with other users. The key that unlocks the door of innovative thinking and knowledge building, the SIMULIA Community provides you with the tools you need to expand your knowledge, whenever and wherever.