Want to learn more about conceptual structural optimization for urban air mobility? Don’t miss the upcoming webinar!
When it comes to the transportation of the future, a few technologies stand out in particular: electric vehicles, autonomous vehicles, and vertical take-off and landing vehicles (VTOL). The latter are frequently designed to be electrically powered (eVTOL). A great deal of excitement and interest has gathered around urban air mobility (UAM), which would involve using eVTOLs in urban airspaces for both passenger and cargo transport, thus reducing ground traffic.
While the UAM industry is still getting off the ground, multiple startups and OEMs are working to develop concept vehicles, creating an already competitive market. In order to stay ahead in this emerging industry, these manufacturers must take advantage of new tools and methods to streamline the design process
Since sufficient battery energy density may become the limiting factor for the success of the electric UAM industry, one of the primary aims in the conceptual design phase is to determine the most lightweight vehicle structure that meets requirements. Determining the appropriate configuration and sizing of airframe structure is a challenging task and to achieve this goal, we need to make the best use of optimization technologies. In the work presented at NAFEMS World Congress (NWC) 2021, we presented an efficient workflow for conceptual structural sizing by combining parametric and non-parametric optimization techniques.
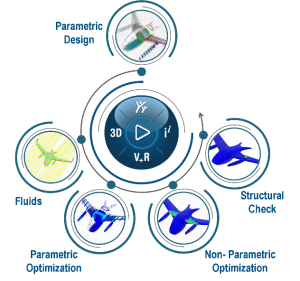
Parametric Design of the Airframe Structure
In a first step, a parametric model of the internal airframe structure is built in the browser-based, on-the-cloud CATIA xGenerative Design application on the 3DEXPERIENCE platform. Thanks to full associativity between simulation models and parametric design data, the time and effort required to design the airframe structure were greatly reduced. Considering external surfaces of previously developed eVTOL design as input, the parametric model is built. CATIA xGenerative Design application allows one to design the internal airframe structure using a combination of graphical visual scripting and the interactive 3D modeling interface.
Don’t miss the upcoming webinar to learn more about eVTOL conceptual development!
The left side below image shows the 3D modeling interface with different internal airframe components such as ribs, front and rear spar, pylon bulkheads, floor structure, front and rear bulkhead, center wing box, and stringers. The right image shows the graphical modeling interface where the parametric design graph can be quickly built by dragging and dropping existing components. With a graph, you get a global view of the dependencies between the collections of objects, parameters, and operators within your model.
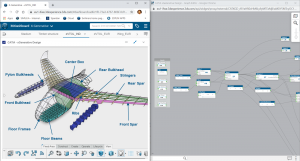
Flight loads equilibrium
External loads in critical flight conditions must be balanced for structural sizing. In any given flight condition, the vehicle is subjected to aerodynamic loads, rotor forces, gravity, and inertia loads. Thanks to the 3DEXPERIENCE platform, using the Fluid Dynamics application, a Computational Fluid Dynamics (CFD) simulation model can be fully associated with the design. CFD simulation was set up to determine the aerodynamic loads of the conceptual eVTOL vehicle as a function of angle of attack, Mach number, etc. Rotor forces, balancing aerodynamics, inertia, and gravity loads were then computed to ensure flight loads equilibrium. This external load database was used to feed the structural model of the eVTOL. Two limit loads were considered: positive limit load and negative limit load as indicated by the black circles in the plot below.
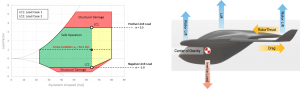
Aerodynamic Pressure Mapping
Fully associated with parametric design, a structural finite element model was built in Mechanical Scenario application on the 3DEXPERIENCE platform. Model meshed with shell and beam elements for different internal structures. The front and rear rotors, and battery, are idealized as point masses connected to the structure through distributed coupling constraints. It is assumed that the structure is made of standard carbon fiber reinforced polymer (CFRP) composite material. Along with inertia and rotor loads, the aerodynamic pressure distribution from the CFD mesh to the structural mesh was mapped for the structural sizing task.
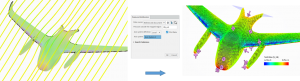
Parametric Design Study
For parametric simulation models built in the 3DEXPERIENCE platform, the new Parametric Design Study application provides an intuitive and easy-to-use interface for setting up design of experiment (DOE) studies. A parametric design study was performed for the eVTOL vehicle considering various design responses such as stresses, displacements and mass.
Parametric and Non-Parametric Structural Optimization
In this conceptual design study, parametric optimization and non-parametric sizing techniques were combined using the Process Composer application available on the 3DEXPERIENCE platform. A Pointer-2 optimization technique was applied directly to the parametric model.
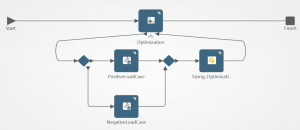
Under the optimization task both positive and negative load cases of structural model are executed in parallel for each iteration. The objective of the parametric optimization is to minimize the total structural mass subject to a stress constraint and a displacement constraint. Within each iteration of the optimization run, a non-parametric sizing task is performed in Tosca Structure to further reduce the mass by optimizing the distribution of outer skin thickness and stringer properties. The final optimized model was further checked for structural requirements like buckling and strength of the composite to validate the configuration.
Optimized vehicle configuration and sizing optimization history
Benefits of our Workflow to Urban Air Mobility
When it comes to the development of eVTOL vehicles, battery weight is one of the key limiting factors. The proposed workflow reduces conceptual vehicle weight by making best use of current structural optimization technologies. The tight integration of parametric design, simulation and optimization within the 3DEXPERIENCE platform greatly benefits conceptual structural sizing studies. The xGenerative Design application makes parametric design accessible to all designers without complex programming. Furthermore, as structural simulation models are fully associated with the parametric design, it becomes easy to automate the exploration of a large number of design configurations and perform optimization by combining parametric and non-parametric methods.
For more details, please refer to our full-length paper presented at NAFEMS World Congress 2021 in the SIMULIA Community, here.
SIMULIA offers an advanced simulation product portfolio, including Abaqus, Isight, fe-safe, Tosca, Simpoe-Mold, SIMPACK, CST Studio Suite, XFlow, PowerFLOW, and more. The SIMULIA Community is the place to find the latest resources for SIMULIA software and to collaborate with other users. The key that unlocks the door of innovative thinking and knowledge building, the SIMULIA Community provides you with the tools you need to expand your knowledge, whenever and wherever.