For hundreds of year, architects, designers and inventors have looked to nature as an abundant source of inspiration. Biomimicry, the study of emulating and mimicking natural systems to solve human problems was first popularized by biologist Janine Benyus. In her book Biomimicry: Innovation Inspired by Nature, she transforms the thought process of how we can learn and look to nature for inspiration. She suggests that we look to nature as a model and guide to creating to solutions.
Nature has been solving problems for over 3.8 billion years. Through Biomimicry we can learn how to apply these clever insights to solve the problems of humanity. Biomimicry allows designers to widen their perspectives and evaluate ideas with a more critical eye to developing solutions that integrate and flow with the surrounding ecosystem. With the rise of advanced computer technology and the digitalization of our environment, it has become much easier to analyze, understand, and mimic designs seen in nature. Through simulation, design can play a crucial role not only in how we understand our world but how we can learn from these experiences and innovate to solve human problems.
Interior design and architecture has increasingly been influenced more and more from bio-design over the years. Architectural structures from Zaha Hadid Architects and product designs from Ross Lovegrove are key examples of this design thinking. Designs are often influenced from microorganisms, diatoms, plant and animal skeletal structure. These designs incorporate inspirations from macro and micro-size to provide innovative design solutions from nature.
Light weighting structures has been increasing trend within the industrial manufacture space. Research has focused on the development light weighting structures using honeycomb, foam and tubular structural elements. However, nature optimizes structural elements by optimizing the form of the element only placing material where it is needed and removing it where it is not needed. A prominent example of this type of structure is the microstructure of bone. Bone is optimized to provide a high level of stiffness and the right amount of elasticity with minimal mass. The calcium carbonate lattice structure is only in places where applied on the bone. Taking cues from bone structure as well as other influences from diatoms, pollen, and leaves in this study a simple lounge chair was designed using various modeling tools and simulated using Abaqus.
Sitting we do every day. Whether in a car, at work, or at home, we are seated on average more than 10 hours a day. How do we go about designing better chairs that are designed with better industrial ergonomics software while minimizing materials? This is where simulation can play a key role in the design process. Specifically topology optimization and shape optimization techniques will be used to design the chair. According to Herman Miller, in a seated position, the body does not achieve the proper alignment of spine. The lower back is not supported and tends to straighten out or slump in an outward direction. To counter this, a good chair, provides the necessary support to cradle the sacral-pelvic area. In this furniture design the body is rotated back such that the pressure from the body is taken on the spine cradling the body along the surface of the chair.
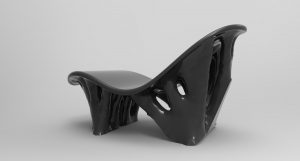
Using 3DEXPERIENCE, a general design volume was created using the functional generative design application. Within this application geometry can be created, and simulation parameters set using the integrated guided assistant. A simple static simulation was setup to simulate a person sitting on the chair. Using simulation the overall shape and structure of the design is optimized for stiffness and minimal mass. After re-topologizing and smoothing of the geometry, an optimized product is created.
New designs such as this are challenging to manufacture. However, with the advent of new manufacturing techniques in the additive manufacturing software space we can create forms in new and innovative ways. From conventional fused deposition modeling (FDM) printing, to selective laser sintering (SLS), to continuous liquid interface production (CLIP) printing, new materials and processes can be developed and explored in a digitally simulated framework.
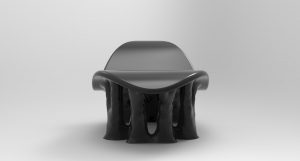
The relationship between the tools we use to investigate space and the way we understand space is constantly changing. Thus as designers we have to engage creative process of design with new and open perspectives. New generative and computational techniques allow for greater flexibility in a designers’ ability to discover form. Biomimic perspectives could lead to design solutions that were never previously considered. We use these computational tools not only to create the built environment around us but to create experiences that harmonize product, nature, and life.