This article was originally published in the June 2019 issue of SIMULIA Community News magazine .
Cracks in metal components affect many industries including aerospace, power, chemical process, petroleum, pipelines, and heavy equipment. When cracks are found, two common questions are: will it break, and how soon will it break? When considering potential cracks, how large of a crack will cause failure? These questions are addressed using fracture mechanics analysis, (refer to the API 579/ASME FFS-1 standard [1]). Aerospace structures can be made from a variety of materials, and being able to assess cracks in the metal components helps engineers ensure safe and reliable structures.
CRACK MODELS For some geometry and crack shapes, solutions may already exist, or custom crack models can be created for finite element analysis, such as the turbine model shown in the first image [2]. Several crack locations were examined using a symmetric model of the turbine shaft. An important feature of a crack model is the focused mesh region, shown in the second image. Abaqus uses the concentric contours of brick elements to compute the J-integral values along the crack front, and allows comparison of each contour’s value, helping to assure accurate results.
CRACK ASSESSMENT To assess cracks for failure, several approaches are available, including the Failure Assessment Diagram (FAD), crack driving force, and ductile tearing instability. The FAD method was used for the turbine assessment, and the third image shows an FAD plot comparing the assessment points for two crack sizes. The 10 mm crack is stable (below the FAD curve), and the 12 mm crack is unstable (above the FAD curve) and predicts failure.
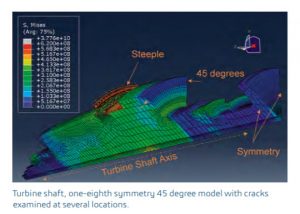
A typical workflow to obtain the FAD is to create the overall geometry and mesh using Abaqus/CAE, then partition the model where the crack mesh will be added. The next step is to import the partitioned region into FEACrack, select crack mesh refinement, apply material and boundary conditions, and generate the crack mesh. The crack mesh is either combined with the larger model or run as a sub-model. To obtain the needed J-integral results for the crack assessment, increase the loading magnitude over several analysis steps in an elasticplastic analysis to allow crack front plasticity to develop. Use enough mesh refinement to capture the crack front blunting. Use the J-integral results to determine the reference stress, which gives the FAD Lr assessment point value. Also run an elastic analysis of the crack model to obtain the stress intensity K values, and determine the FAD Kr assessment point value.
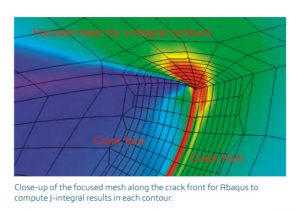
A limiting crack analysis varies the crack size until the assessment point is on the FAD curve at the limit of stability. Knowing the limiting flaw sizes helps to plan for inspections and the minimum size of a crack that needs to be detected.
SOFTWARE FEATURES Using the combination of Abaqus and FEACrack benefits engineers by addressing the challenges of creating crack models and quickly generating the numerous crack meshes needed for assessments. The fatigue module computes crack growth due to cyclic loading. Abaqus provides important features for cracking analysis, such as tied contact to connect the crack mesh to the larger model, general contact to model crack face closure, non-linear material, sub-model, and J-integral calculation.
Videos of cracking analysis examples are available on the SIMULIA Learning Community. If you are interested in knowing more about cracking analysis, please contact G.Thorwald@QuestIntegrity.com.
REFERENCES 1. API 579-1/ASME FFS-1, June 2016 “Fitness-For-Service”, The American Society of Mechanical Engineers and the American Petroleum Institute, API Publishing Services, 1220 L Street, N.W., Washington, D.C. 20005 2. G. Thorwald, V. Garcia, R. Bentley, and O. Kwon, “Steam Turbine Critical Crack Evaluation and Ranking Cracks to Prioritize Inspection”, SIMULIA User Meeting at Science in the Age of Experience conference, June 18-21, 2018, Boston.
For More Information, visit Quest Integrity.
SIMULIA offers an advanced simulation product portfolio, including Abaqus, Isight, fe-safe, Tosca, Simpoe-Mold, SIMPACK, CST Studio Suite, XFlow, PowerFLOW and more. The SIMULIA Learning Community is the place to find the latest resources for SIMULIA software and to collaborate with other users. The key that unlocks the door of innovative thinking and knowledge building, the SIMULIA Learning Community provides you with the tools you need to expand your knowledge, whenever and wherever.