How do composite materials relate to you and me?
A composite material is made of two or more materials. One is a binder material that holds everything together. The others are stronger materials that act as reinforcement such as woven fiber. Composite materials have many advantages compared to traditional homogeneous materials such as metal: they have higher strength to weight ratio, which is desirable in aircraft design for fuel cost saving, they have better corrosion resistance and durability. They are also easier for engineers to tailor and optimize.
Composite materials are widely used in industries such as aerospace, automobile, construction, sports, and wind energy. Commercial aircraft such as Boeing 787 and Airbus 350 are more than 50% composite, by weight. Composites also play a big role in popular sports such as Formula 1 racing and America’s cup.
How does Simulation come into play?
Simulation allows us to understand composite material behavior with less physical testing. We can create a finite element model of a composite material with detailed microstructure. By performing simulation with these FE models, we can predict local constituent failure, delamination, and other small-scale behaviors that cannot be easily measured in physical tests.
On a larger scale, we can use simulation combined with efficient multiscale modeling to study how manufacturing processes can affect the quality of the final product. For example, for injection molded thermoplastic parts, we can simulate the flow of the fibers during the injection process. The predicted fiber orientation can be incorporated into the material model, and the weakest locations of the part under a service load can be detected through a structural simulation. Simulation can also be used to compute the residual strain and stress from the curing process, and to predict the resulting warpage.
For composite laminates used in large structures such as aircraft wings, we can also use simulation to design ply sequence and orientations. The design can be evaluated through simulation of different loading conditions, and the final optimized design can be used directly for manufacturing.
How will this continue to impact us in the future?
With the development of composites taking a major role in the world material market, there is a growing demand on software companies to provide accurate and easy-to-use simulation tools. We are very excited about this opportunity and look forward to the future challenges.
Check out Huidi’s video on LinkedIn!
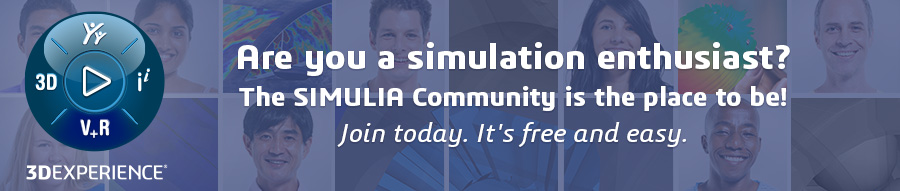
Interested in the latest in simulation? Looking for advice and best practices? Want to discuss simulation with fellow users and Dassault Systèmes experts? The SIMULIA Community is the place to find the latest resources for SIMULIA software and to collaborate with other users. The key that unlocks the door of innovative thinking and knowledge building, the SIMULIA Community provides you with the tools you need to expand your knowledge, whenever and wherever.