This is Part 4 of our 6-part blog series based on our white paper, “The Top Five Reasons for Manufacturers to Improve Data Management.”
Reason #4: Increase Agility and Flexibility
By improving data management, manufacturing organizations will be able to support increased organizational agility and flexibility by doing the following:
- Shortening Engineered-to-Order Lead-Times – Shortening development and delivery leadtimes is a critical success factor for many manufacturers of engineered-to-order products. The automated workflows supported by an integrated PDM (product data management) system can dramatically shorten both proposal and product development, giving engineered-to-order manufacturers the agility and flexibility required to compete successfully in a global competitive market.
- Incorporating Concurrent Product Development and long-term Manufacturing Planning software – With the agility and flexibility afforded by an integrated PDM system, manufacturing planning can begin concurrently with the final stages of product development. Because both product development and manufacturing personnel can collaborate more effectively during the latter stages of development prior to a product’s release to production, they’ll need less time to plan for production and have the flexibility to collaborate on and make changes through a product’s release to manufacturing.
- Developing Products and Documentation Simultaneously – Instead of waiting until a product is manufactured to develop content for user manuals, service manuals, parts lists, and other forms of product documentation, manufacturers can leverage a PDM system to establish a concurrent workflow through which products and accompanying documentation are developed at the same time, with design changes reflected in auto-updating design data that is used for both purposes.
A Case in Point: Increasing Agility and Flexibility at Automatic Handling International
The 3DEXPERIENCE platform has enabled Automatic Handling to further automate workflows and processes, achieving natural synergies and resulting in a completely paperless, more efficient model-based definition (MBD) approach to production.
“We’re an engineered-to-order business with over a dozen mechanical engineers, all working on overlapping projects,” explains Media Group Manager Nathan Pienta. “The structure and control… enable us to work more accurately and productively, using virtual documents to develop, manufacture, and assemble machines, instead of pushing paper.”
As a result, Automatic Handling has cut manufacturing release times by 80 percent, replaced paper drawings with digital 3D models for production, empowered machinists and fabricators as part of the development process, and eliminated printing, paper, and administrative costs.
To read the full Automatic Handling Case Study, download the white paper.
Part 1: Reason #1 – Boost Productivity
Part 2: Reason #2 – Improve Product Quality
Part 3: Reason #3 – Facilitate Collaboration
Part 4: Reason #4 – Increase Agility & Flexibility
Part 5: Reason #5 – Inspire Innovation
Part 6: Make Data Management a Competitive Strength with NETVIBES on the 3DEXPERIENCE platform
Download the “Top Five Reasons for Manufacturers to Improve Data Management” white paper
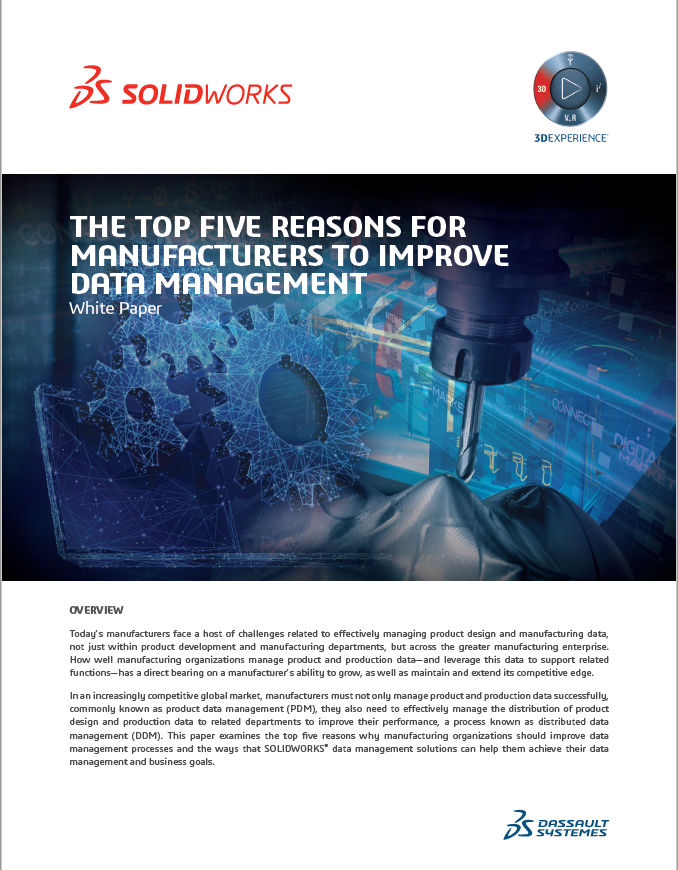
Join our User Communities to stay on top of the latest industry news, ask questions and collaborate with peers:
- EXALEAD Sourcing & Standardization Intelligence User Community
- 3DEXPERIENCE Marketplace | PartSupply User Community
- NETVIBES Public Community
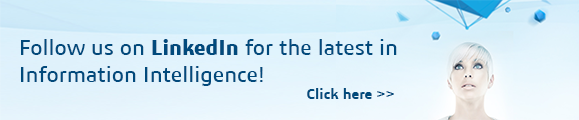