This is Part 10 of our 12-part blog series based on the LNS Research eBook,“Forging the Digital Twin in Discrete Manufacturing: A Vision for Unity In the Virtual and Real Worlds”.
Previously in Part 9 we examined the software in Digital Twin for manufacturing. Now let’s look at real data versus virtual data in the Digital Twin.
Real Data Versus Virtual Data
The majority of digital twins today are based on a simple concept—collect real data and use it in the virtual system to model behavior, or simulate virtual data to test the actual system’s expected behavior. The goal is to determine system outcomes without direct access to the real system or parts thereof.
For example, operators at a simple assembly station might do everything manually. It’s a straightforward exercise to define tools and stations needed, the system parts and the people. The as-designed model from CAD or PLM is also usually available; it is the system output. Applying all these elements in the Digital Twin, we can run what-if scenarios to understand if adding a robot would improve manufacturing by:
- Easing the load on the people involved,
- Increasing production,
- Reducing defects, or
- Removing some people.
Engineers could even design the manufacturing cell to do more than one job, some using a robot and others just people. The objective with a digital twin isn’t to replace people but rather enhance their capabilities and create new processes to which the people can add value, especially in improving customer relations.
As companies move from basic use of a digital twin like the one above, to more complex applications like testing a finished product while still in the production environment, they compound the value of twin technology. Product testing is a much more common use case in discrete manufacturing. The workforce can use the product digital twin in many ways including designing the manufacturing process and managing the delivered product. In the short term, the most likely scenario is product enhancement and refresh—applying a digital twin to an existing product to improve it. While we mentioned software updates, there are far more opportunities to update a product in service than just code refreshes.
Imagine using a digital twin to test physical upgrades for implementation in the field. Large industrial machinery is one example where the life of a product can involve many upgrades, improvements and maintenance changes. By recording all changes in the virtual asset history, we achieve a digital twin with accuracy that matches the “as maintained” status of the actual equipment. This level of detail allows the organization to consider improvements before it incurs expensive parts and time.
Although this report zeros in on discrete manufactured products, it’s important to consider the digital twin in a broader context. A digital twin can model the environment where a product exists; virtual cities with ever-increasing fidelity is the perfect environment to test and develop virtual products. Ultimately, manufacturers should apply imagination and creativity to come up with new ways to exploit virtual environments and enhance digital twins.
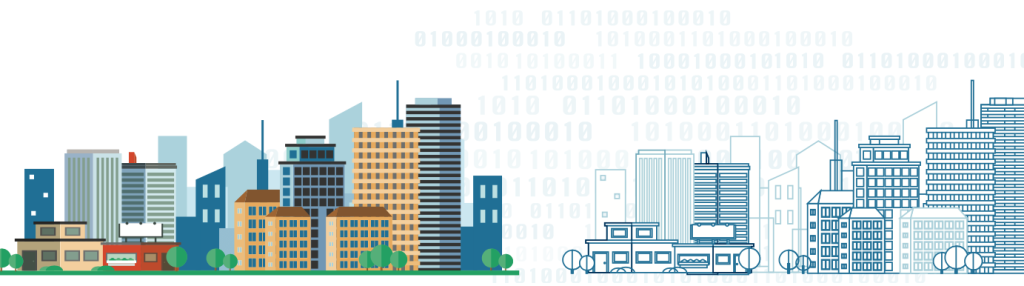
EXALEAD Commentary
Why do we need real data? Feedback from real systems is required to understand the behavior of a system and detect any deviations as compared to the plan.
If only systems would behave exactly as they should, it wouldn’t be necessary to take such measures. In that case, it would be sufficient to be informed when the system has achieved the mission it was asked to perform.
This is the way Enterprise Resource Planning (ERP) systems have been designed. Production orders describe the production process as a sequence of operations that should be performed in a given time, with given resources, with standard rates. The processes are planned to happen according to a “happy path” without integrating unexpected issues or delays that might occur during production. Manufacturing Execution Systems (MES) /Manufacturing Operations Management Systems (MOM) software [here I left the abbreviation] are designed to manage shop floor operational data and activities by acting as an abstraction layer between ERP systems and manufacturing plants.
As soon as planned production orders (in the ERP) are put into production (in the MES), all required resources, including people, machines, products and tools, are allocated. Even if the MES is reporting back progress in real-time to the ERP, this feedback loop doesn’t take into consideration any exception handling. How can manufacturers react efficiently if one operation on a given work order is not in adherence with the plan? How can we analyze the problem, and is it possible to replay the sequence? Which decisions should be made to manage the issue? Is it an exception or is it recurring, and did similar Issues happen in other plants? How can we prevent them in the future?
EXALEAD Asset Quality Intelligence on the 3DEXPERIENCE platform is a decision-making analytics application that enables manufacturers to engage in continuous improvement through the implementation of a short interval control loop—from issues reported in operations by final users, back to manufacturing, and back to engineering and product design.
In the next blog installment, we will explore simulating the manufacturing process with Digital Twins.
Part 1: What is a 3DEXPERIENCE Twin?
Part 2: Digital Twins and Manufacturing: Today’s Possibilities
Part 3: Who is Using Digital Twin Technology?
Part 4: Growth Expectations for Digital Twins in Manufacturing
Part 5: Digital Twin Use Cases in Manufacturing
Part 6: Exploring Digital Twin Opportunities in Manufacturing
Part 7: Simulating Product Use with Digital Twins in Manufacturing
Part 8: Simulating the Manufacturing Process with Digital Twins
Part 9: Software in Digital Twin
Part 10: Real Data Versus Virtual Data
Part 11: Digital Twin: Pragmatic Considerations
Part 12: Recommendations for Getting Started with Digital Twin
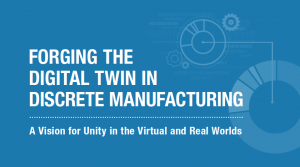
Read LNS eBook on Forging the Digital Twin in Discrete Manufacturing
Join our User Communities to stay on top of the latest industry news, ask questions and collaborate with peers: