Manufacturing is changing fast.
Advances like 3D printing, virtual design technology, artificial intelligence (AI) and more integrated communication between the actors in the entire production chain are creating new opportunities.
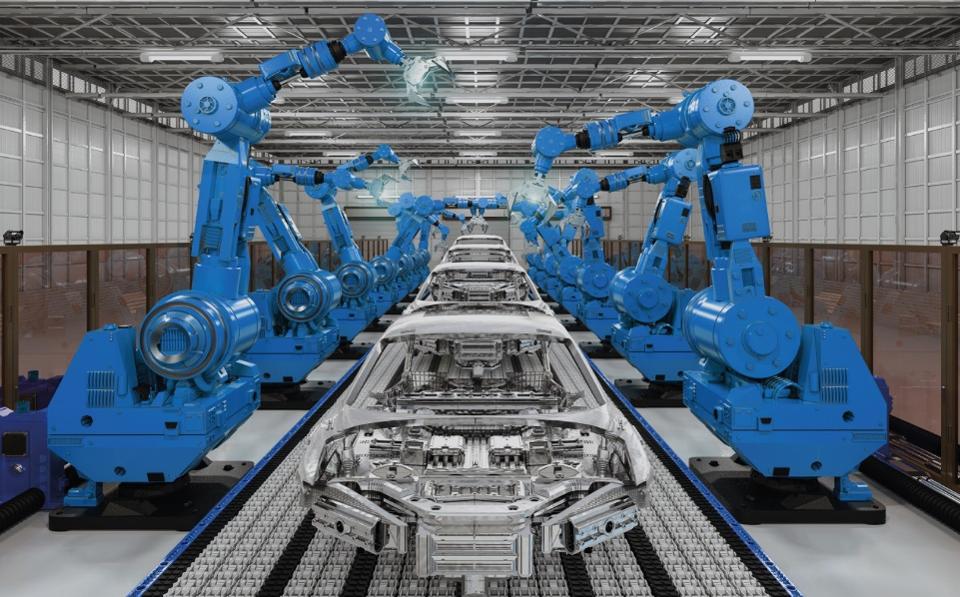
“In the past we’ve had mass production as a major manufacturing paradigm, and we’ve had lean manufacturing,” said Li Zheng, Professor, PhD Supervisor and Vice President at Tsinghua University in Beijing. “But now we’re seeing a new paradigm.”
In that paradigm, engineers, scientists, designers and everyone else involved in manufacturing can do things they could only dream about a decade ago.
The result is a brave new manufacturing world.
The New Labor Market Opportunities
For all the talk of new opportunities, there is a downside. As traditional logistics and manufacturing models phase out, there’s uncertainty about what the industrial future may hold.
A recent World Economic Forum report predicted machines will perform a significant portion of manufacturing tasks by 2025, eliminating some 75 million jobs. On the other hand, the new AI-enabled relationship between human labor and machines will create an extra 133 million jobs, according to the report.
The report also predicts the labor market will change as freelance and part-time labor become more prominent.
The new opportunities that do arise will accrue to those able to harness the new tech. The new technological reality will disrupt our educational system itself. In fact, it will have to, as the workforce is unprepared for the new reality, as one prominent academic in the field argues.
“We need to train and educate 21st century students for 21st century jobs with 21st century methods, and I think we fall some way short of that,” said Michael Grieves, Executive Director of the Center for Advanced Manufacturing and Innovative Design (CAMID) at the Florida Institute of Technology.
“We need to incorporate the technologies that the people coming into the workforce grew up with,” he added.
Tying Tech To Business Outcomes
One basic shift in manufacturing today is a shift of emphasis: from the product itself to its application. The sector is grappling with the advent of the “experience economy,” where consumers are less interested in owning something and more interested in the experience they gain or result they achieve by using it.
“People don’t want a drill,” said Grieves. “They want a hole.”
Li agrees that technology itself isn’t the important thing for companies, either. The goal, rather, is to achieve business objectives: Automation, for instance, can be used to boost productivity or quality or reduce costs.
“We need to know why we use a technology,” Li said. “If we know our objective, we can deploy our talent effectively and make use of new technology properly.”
That will mean tying technology to a business outcome.“It’s not only that you buy the software and you buy the hardware and you install it in the workshop,” Li said.
“It’s more related to people. You have to train the people. You have to change your mindset and change the way you work. It’s a transformation.”
Technology investment, he said, is merely a first step. After that businesses need to invest time, effort and leadership to be successful.
Still, the technology is driving the conversation.
“In the old days we could only solve an equation with 10 variables,” Li said. “But now we have more power, and by using this computing capability we’re realizing data-driven smart manufacturing and optimizing not only the factory, but the whole production network.”
How AR Will Change The Paradigm
One of the biggest developments in manufacturing is augmented reality (AR), in which a computer superimposes information—pictures, data, or anything else—over the user’s field of vision. A technician wearing smart glasses who’s looking at a turbine, for example, will “see” useful data about that turbine laid over the machine itself.
This can bring immense training and safety benefits.
Workers can use AR glasses to learn how to assemble equipment correctly: The glasses will superimpose instructions right over the gear, perhaps making clear with lines and arrows in what direction components should be installed. As a result, employees will learn faster, reducing the time and money required for training.
Using AR to deliver equipment usage instructions to workers at their stations will also improve occupational safety.
“Augmented reality is really a revolution,” said Laurent Champaney, President, École Nationale Supérieure d’Arts et Métiers, a French engineering graduate school. This revolution implies “a new way of communicating that touches everyone at every level of a company.” It can also, however, lead to “complex issues,” he said.
The Promise And Peril Of Big Data
The new communications technologies also let manufacturers create value by sharing information with their partner companies, Champaney said. But again, how to most effectively harness that big data remains a question.
In our era of high-profile hacks and anxiety about who’s doing what with our online data, security will be a huge issue for manufacturing.
“Data is everywhere, but protecting it is a major issue for companies,” Champaney said.
That will remain the case as the big-data era progresses.
Listen to the full academic panel discussion exploring the future trends of Manufacturing.
Cameron Wilson is a UK-trained journalist who for the last 13 years has been based in Shanghai, where he’s been charting the social and economic development of China.