This is Part 6 of our 12-part blog series based on the LNS Research eBook “Forging the Digital Twin in Discrete Manufacturing: A Vision for Unity in the Virtual and Real Worlds”.
Previously in Part 5 we investigated the top manufacturing use cases for Digital Twins. Now let’s take a look at the opportunities presented by Digital Twins in manufacturing.
Digital Twin Tech in Play
As we have seen, the advent of new technologies opens new opportunities for digital twins across many industries. When we look at the standard technologies used in IIoT systems, many are directly useful in both the real world and the virtual world. The traditional markets for digital twins, automotive, aerospace, and defense start the design process with 3D models of physical parts, then manage those in a product lifecycle management (PLM) platform. Creating all these models and making them “executable” requires a solid foundation.
INTERSECTION OF PLATFORMS ENABLES DIGITAL TWIN
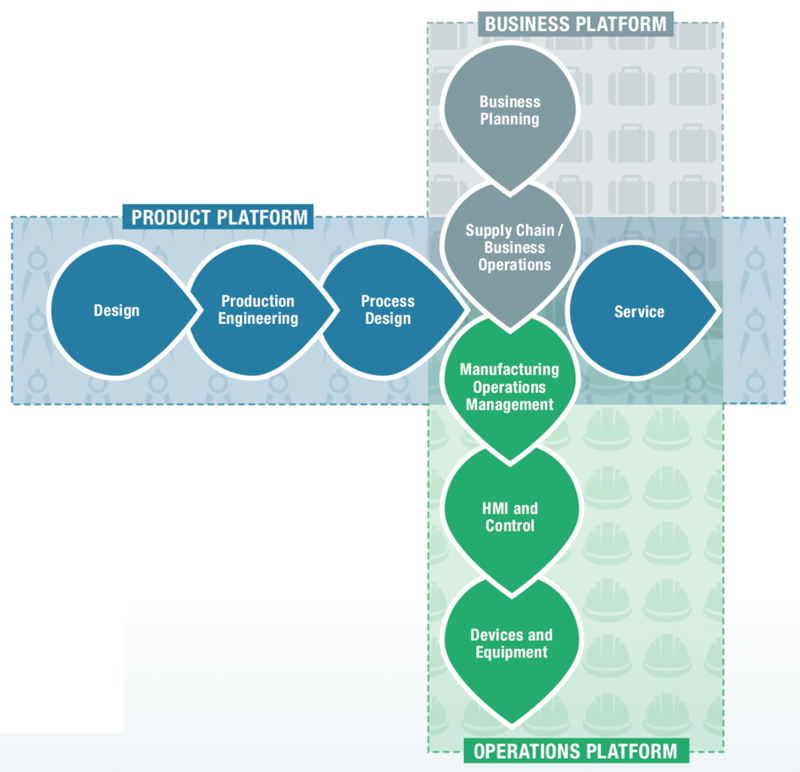
The key to finding a good starting point for a digital twin is to use a rigorous model-based systems engineering (MBSE) approach to product design. MBSE can be used at every level of detail of a system and helps engineers focus on the design rather than the traditional hierarchy complexity of documents and drawings. There are de facto standard MBSE design languages, such as UML and SysML; something that dramatically aids the acceptance and use of the technologies, and eases adoption across multiple teams working on large projects.
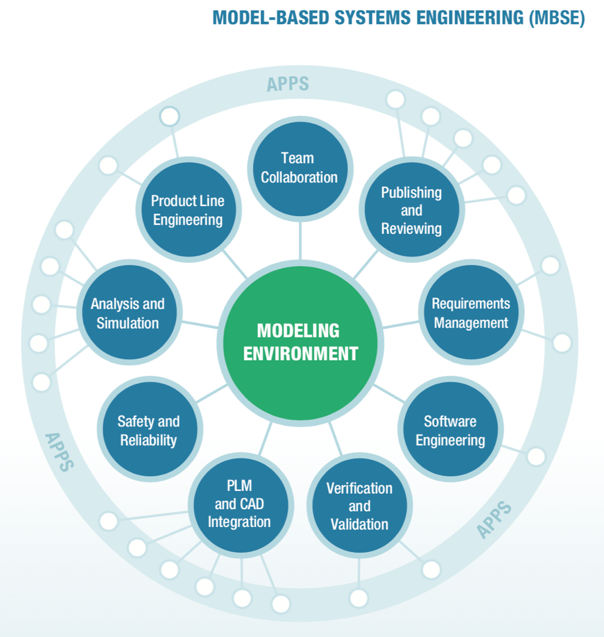
While MBSE is effective, it’s not enough. Models are a great way of using and sharing information about a complex product. Furthermore, engineers can build them hierarchically so that many different people can receive views of the same product or system with more or less detail. Traditional 3D models and hierarchical engineering bills of material (BOM) built in a model-based environment allow communication across the product development organization. When it comes to the more commercial side of development, such as costing and procurement, many manufacturing organizations will turn to the traditional ERP system. However, as leading manufacturers move to leverage IIoT-based approaches to advance Smart Manufacturing or Industry 4.0, in context of their business processes, the opportunity to integrate engineering models and business functions will increase, and will therefore drive ever more value from product data all the time.
EXPANDED VIEW OF DATA: DIGITAL TWIN DEMANDS MORE THAN “JUST” PRODUCTION DATA
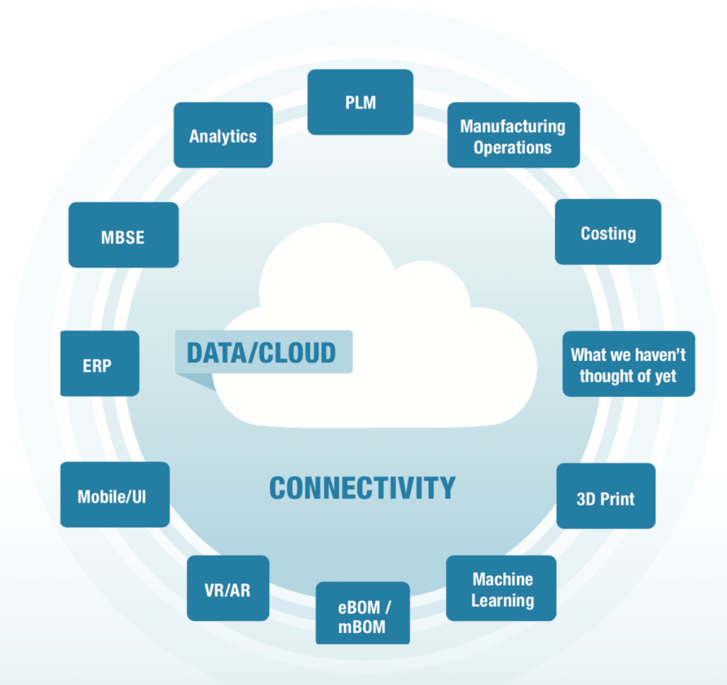
As we progress into the design detail, engineers combine components in the design world, and the digital representations are similarly brought together to deliver a view closer to reality. People can inspect and combine one digital twin with others, either developed for the current project or already in a library of existing twins. The goal for the Digital Twin is to keep on growing in parallel as the system develops; at each stage the Digital Twin receives more virtual information. This progression is fairly obvious when looking at purely mechanical parts of a product or system. However, opportunities to use the Digital Twin to aid development reach far beyond simple product design; a few include:
- Simulating product use in varying environments
- Simulating the manufacturing process
- Testing product software (that which is embedded in the product)
EXALEAD Commentary:
Dassault Systèmes’ 3DEXPERIENCE twin offers the opportunity to go beyond the Digital Twin in manufacturing by addressing all stakeholders through the full lifecycle of a product, from design to after-sales.
3DEXPERIENCE twin offers new opportunities for engineering companies:
Early in the process, EPC (Engineering Procurement & Construction) companies can project their customers into the immersive reality of their future plant, system or product. Later on, once construction has started, customers can conduct 3D planning reviews in the 3DEXPERIENCE twin and ensure that their requirements are correctly covered.
Sharing during the early stage reduces the risk of misunderstandings, saving costs and time by reducing rework.
3DEXPERIENCE twin offers new opportunities for manufacturers:
Manufacturing is probably the segment where the 3DEXPERIENCE twin will drive the most intensive business transformation. Manufactured products are first made available to the market in a virtual environment. Manufacturing lines are then fully designed virtually to validate that the future products can be produced according to plan. EXALEAD on the 3DEXPERIENCE platform provides analytics to optimize the design by reducing the number of new product parts or components to be produced. The application, OnePart Reduce, allows companies to rationalize the parts created, contributing to reduce the overall footprint of the products, reducing time-to-market and facilitating innovation and agility.
Machine makers will be able to deliver more and more automated machines that will be much more autonomous than today. Operators will not need to be posted close to the machines throughout the full shift. Machines will transform the production mode from push to pull. Operators equipped with mobile devices and mounted headsets will be notified by the machines when a problem is encountered that can’t be solved automatically. Thanks to the interactivity fieldworkers will have with the 3DEXPERIENCE twin, they will get access to all necessary information in augmented reality to know how to solve the issues reported by the machines.
Simulating the products and the way to manufacture them is reducing the risk of errors in production. Doing it right the first time will accelerate innovation.
3DEXPERIENCE twin offers new opportunities for owners/operators:
3DEXPERIENCE twin empowers manufacturers to access, from anywhere, operational data of production plants through navigation into the 3D representation of the installations without having to go onsite or open multiple IT systems to get access to any relevant information. Engineers can navigate in the virtual plant through different views (by plant, geographical , or work breakdown, etc.). They can perform advanced searches for 1D, 2D and 3D documents related to assets and systems, displaying the content of multiple documents or sources in the context of the 3D data. All engineering changes can be prepared in the virtual environment, including fieldworkers’ training and rehearsal, reducing planned downtime and securing onsite activities.
Preparing the activities in early stage reduces the risk of errors.
3DEXPERIENCE twin offers new opportunities for after-sales services:
The challenge for the coming years is to manage the transition between old and new technology. People close to retirement have the knowledge of the installed base (based on old technologies), whereas millennials are familiar with new technologies but have less experience with legacy systems.
Today a huge amount of written information, such as maintenance reports, operating procedures, repair memos, log and shift books, is stored in the data center of industrials companies. These unstructured documents contain a mine of useful information for those who know where to find them and how to link them together in order to establish relationships between issues and resolutions.
EXALEAD’s Asset Quality Intelligence application is providing smart analytics to help exploit this information and make it available to users for root cause investigations. An advanced search engine allows users to enter key words and expressions to describe the symptoms for which the user would like to retrieve relevant information from past situations. Content of past reports, memos, documents, and logs are analyzed and automatically classified into relevant groups, tying correlations between events. Results are revealed on a set of analytical dashboards on which users can collaborate and interact with the data. From the analytics, the user can deep dive into details refining his diagnosis, drill down to the root causes of similar situations, retrieve resolution reports to analyze which would be the most relevant for the given issue to solve, and initiate a change process including all necessary findings to resolve the issue.
Supporting service organizations for digital continuity will reduce the risk of losing knowledge and expertise and improve services quality.
3DEXPERIENCE twin offers new opportunities for consumers:
End-users and consumers can virtually evaluate, compare, and test a product before buying it.
Having the ability to test the user experience reduces the risk of making a bad choice.
In the next blog installment, we will explore simulating product use with Digital Twins in manufacturing.
Part 1: What is a 3DEXPERIENCE Twin?
Part 2: Digital Twins and Manufacturing: Today’s Possibilities
Part 3: Who is Using Digital Twin Technology?
Part 4: Growth Expectations for Digital Twins in Manufacturing
Part 5: Digital Twin Use Cases in Manufacturing
Part 6: Exploring Digital Twin Opportunities in Manufacturing
Part 7: Simulating Product Use with Digital Twins in Manufacturing
Part 8: Simulating the Manufacturing Process with Digital Twins
Part 9: Software in Digital Twin
Part 10: Real Data Versus Virtual Data
Part 11: Digital Twin: Pragmatic Considerations
Part 12: Recommendations for Getting Started with Digital Twin
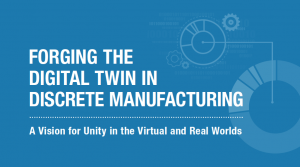
Read LNS eBook on Forging the Digital Twin in Discrete Manufacturing
Join our User Communities to stay on top of the latest industry news, ask questions and collaborate with peers:
- EXALEAD Sourcing & Standardization Intelligence User Community
- 3DEXPERIENCE Marketplace | PartSupply User Community
- NETVIBES Public Community
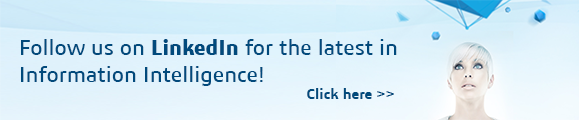