This is Part 4 of our 5-part blog series based on the IoT World Today white paper, “Digital Manufacturing and the IIoT: Success with a Single Platform.”
Part 4: The Value of Single-Platform Collaboration
Effective use of IIoT deployments can help define business processes, workflow and coordination, data management, and product integrity and performance.
In general, it’s critical for manufacturing organizations to have a high degree of cooperation across their internal value chains. For example, by using one unified platform at the design level, concept ideas can be shared, tracked, and discussed with all stakeholders participating via one unified interface. By relying on one correct version of a prototype or product, all stakeholders can have accurate visibility of project status at all times.
That’s partly the concept behind digital twin technology. Using a complex array of software-based systems, companies can create digital twins to accurately duplicate and simulate the real-world properties and performance of individual products, manufacturing processes or entire plants. This digitally informed design approach eliminates the need for physical prototypes, reduces development time, improves overall quality and enables faster design iterations. It’s a revolutionary approach that enables manufacturers to capitalize on real-time data, making design changes as needed or in response to customer feedback.
In the same way, a unified IIoT platform enables manufacturers to access, monitor and control their production processes. It offers a consistent, uniform way to deal with all the data challenges that manufacturers face across their supply chains. Within the manufacturing environment, a single platform integrates a range of applications that rely on diverse data streams, whether they’re focused on design, operations, or testing and analysis.
By relying on one correct version of a prototype or product, all stakeholders can have accurate visibility of project status at all times.
In fact, that’s one of the driving principles behind the 3DEXPERIENCE® platform from Dassault Systèmes. The scalable, unified platform enables manufacturers to take concepts and prototypes all the way to sophisticated, final products. In addition to gaining valuable insights through real-time data, teams can leverage the information they gather to move into predictive maintenance as well as ensure overall optimization through scenario planning.
In contrast to standard IoT-based storage, connectivity, or device management platforms, 3DEXPERIENCE offers a very different type of platform approach.
It effectively coordinates all the applications that manufacturers rely on and enables them to function together through seamless integration of their individual data streams. Moreover, companies can leverage data to move into maintenance as well as scenario planning and optimization. Such an approach ensures that manufacturing insights based on accurate data are always available at the right time and place. It also guarantees that the most critical ROI for manufacturers—the customer experience—is front and center.
In the conclusion to this blog series, we will look at how to ensure customer satisfaction and prepare for the future.
Part 1: Moving Beyond Pilot Stage Purgatory
Part 2: Confronting Data Challenges
Part 3: IIoT Success: More than Just Connectivity
Part 4: The Value of Single-Platform Collaborations
Part 5: Ensuring Customer Satisfaction & Future Outlook
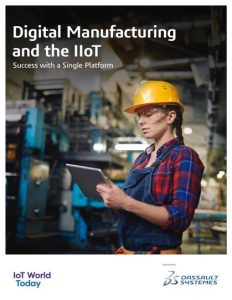
Download the IoT World Today white paper:
Discover more about Dassault Systèmes’ vision for the Factory of the Future.
Join our User Communities to stay on top of the latest industry news, ask questions and collaborate with peers: