To get the big picture on the overall autonomous mine, we caught up with Dassault Systèmes GEOVIA’s Gustavo Pilger, discussing everything from creating a cohesive ecosystem to virtual twins.
How does Dassault Systèmes’ 3DEXPERIENCE platform help to enable more automated mine sites in terms of cloud-based simulation, planning and digital twinning?
The 3DEXPERIENCE platform enables a more automated mine site by integrating cloud-based modeling, planning and simulation into a cohesive ecosystem. This integration provides visibility and control over mining operations, enhances collaboration, and leverages advanced analytics to optimize performance. By facilitating these capabilities, Dassault Systèmes helps mining companies move towards more efficient, safe, and sustainable mining practices.
- Cloud-based Simulation: The 3DEXPERIENCE platform leverages cloud infrastructure to enable real-time collaboration across various locations, significantly enhancing decision-making and efficiency in mining operations. This cloud-based approach ensures scalability and flexibility in simulations, overcoming local hardware limitations. It also provides users with access to advanced tools like geological modeling and mine planning without the need for extensive installations, crucial for optimizing operations and reducing downtime.
- Planning: The platform enhances mining operations through its integrated design, planning and scheduling tools, complemented by operational data integration for more accurate and efficient plans. Its scenario analysis feature allows planners to evaluate different strategies by running “what-if” scenarios, aiding in data-driven decision-making. Additionally, the platform’s resource management capabilities ensure optimal utilization of equipment, labour, and materials, leading to cost reductions and improved operational efficiency.
- Virtual Twinning: Virtual twin offers real-time monitoring and control over assets, significantly enhancing efficiency and reducing downtime through predictive maintenance. Simulations also play a crucial role in improving safety by enabling the rehearsal of emergency scenarios, ensuring better preparedness among mineworkers. Additionally, the continuous feedback provided by the virtual twins facilitates on-the-fly optimizations, further driving down costs and improving operational effectiveness. This technology marks a significant leap forward in mining operations, marrying safety with efficiency in unprecedented ways.
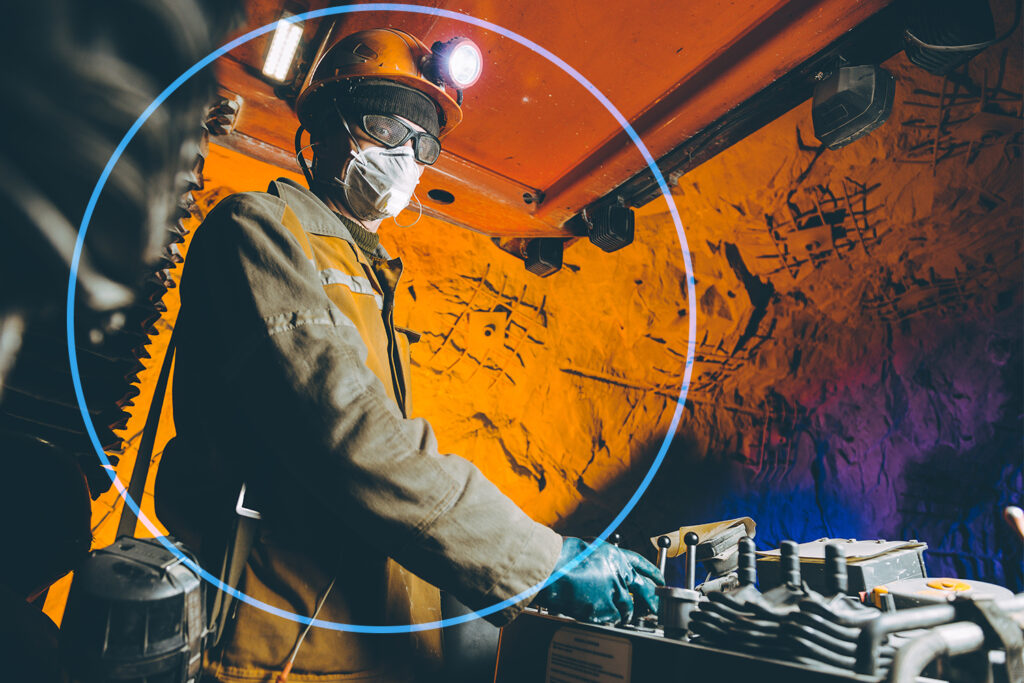
What are some of the major challenges mine sites face in becoming more automated? Is it less in areas like driverless trucks and more in areas like maintenance and monitoring?
The challenges mine sites face in becoming more automated are multifaceted, involving technological, infrastructural, workforce, and regulatory aspects. While areas like driverless mining equipment are challenging, these are more mature areas comparing to others like maintenance and monitoring, for example. These present specific challenges on their own such as the collection, integration and processing of data from IIoT devices across the site. Effective automation in mining requires addressing these challenges through comprehensive planning, investment in technology and infrastructure, workforce development, and continuous improvement of systems and processes. The GEOVIA perspective emphasizes the importance of integrated solutions that provide real-time data, advanced analytics, and seamless operation across all aspects of mining.
One key area for improvement is technological integration. Many mine sites operate with legacy systems that are not easily compatible with newer automated technologies. Upgrading these systems with modern solutions like GEOVIA is an important step in moving toward automation. Ensuring seamless data flow across different systems and departments is also a challenge. Data silos can hinder the effectiveness of automation by limiting access to comprehensive, real-time information. Remote mine locations also struggle with reliable and high-speed internet connectivity, which is essential for real-time data transmission and cloud-based operations.
The transition to more automated systems requires a workforce with new skills, including data analysis, programming, and managing automated equipment. Training and upskilling the existing workforce is a significant challenge. There can be resistance to change from employees who are accustomed to traditional mining practices. Gaining buy-in for new technologies and processes is essential for successful implementation.
Can you give any examples where Dassault Systèmes has partnered with a mining customer to deliver a virtual twin solution that was part of a more automated mine site?
A couple of practical examples come to mind: the first involving safety improvement practices with immersive visualization, and the second around mine operations orchestration and optimization. In the first example, immersive 3D mine visualization scenarios were able to deliver a realistic virtual 3D model of the as-built mining complex, providing a digital environment in which to experience the mine. This 3D virtual environment enabled the miner to review and improve their safety practices including realizing training scenarios on how to respond in case of emergencies.
In the second example, we helped a client to simulate in 4D an underground mining operation considering schedule, resources (machinery, workers), and design to orchestrate the plan and evaluate its practicality. This provided the client with actionable insights to optimize the operation. The solution provided an integrated environment that generated a robust plan, continuously tracking execution adherence to plan and capable to re-schedule it as and when required to respond to disturbances with predictable results.
Overall, this approach provides a virtual mine environment to fail fast and learn cheaply without any risk to workers safety and physical assets. In this way, optimal procedures and schedules can be confirmed and thoroughly validated in the full context of the environment before mine development activities are initiated. Furthermore, valuable know-how and intellectual property can be captured and retained in the 3D environment for future mine development (and production) initiatives. It becomes possible to accurately predict how people and machines will interact in a mine. Such capabilities to simulate and assess these scenarios in detail can help mining companies achieve significant improvements in safety and performance.
What role can Dassault Systèmes play in helping mines improve their planning and scheduling to allow for more autonomous operations?
Dassault Systèmes can play a crucial role in helping mines improve their planning and scheduling, thereby enabling more autonomous operations, thanks to several key capabilities provided by the 3DEXPERIENCE platform and their applications:
Centralized data management is a core feature of the 3DEXPERIENCE platform, offering a unified repository for geological, operational, and engineering information. This centralization facilitates access to the most up-to-date data for all stakeholders, thereby enhancing the accuracy and consistency of project planning and scheduling. Additionally, the adoption of advanced data analytics within this framework enables mining operations to unearth deeper insights into their processes. By analyzing this wealth of information, mines can pinpoint inefficiencies and identify areas where improvements can be made, driving better decision-making and optimizing overall performance.
The ability to run multiple what-if scenarios helps in understanding the potential impacts of different strategies. This is crucial for making informed decisions that optimize resource use and operational efficiency. The platform uses advanced optimization algorithms to refine mining schedules, taking into account factors such as equipment availability, workforce scheduling, and resource constraints.
By integrating real-time data from sensors and IoT devices, the 3DEXPERIENCE platform ensures that planning and scheduling are based on current operational conditions. This real-time feedback loop helps in making adjustments as needed to maintain efficiency and productivity. Predictive maintenance and operational analytics help anticipate potential issues before they occur, allowing for proactive adjustments in planning and scheduling.
The platform facilitates collaboration between different departments (e.g., geology, engineering, operations), ensuring that all aspects of planning and scheduling are aligned. This holistic approach is essential for effective autonomous operations. By providing a single source of truth, the platform enhances communication with all stakeholders, from on-site personnel to management and external partners.
It also provides tools for continuous monitoring and analysis of operational performance. By tracking key performance indicators (KPIs), mines can identify trends and areas for improvement. The ability to adapt plans based on real-time data and feedback ensures that mining operations remain flexible and responsive to changing conditions.
Community is a place for GEOVIA users – from beginners to experts and everyone in between – to get answers to your questions, learn from each other, and network. Join our community to know more:
GEOVIA User Community – Read about industry topics from GEOVIA experts, be the first to know about new product releases and product tips and tricks, and share information and questions with your peers. All industry professionals are welcome to learn, engage, discover and share knowledge to shape a sustainable future of mining.
New member? Create an account, it’s free! Learn more about this community HERE.