The goal of a Digital Twin is to have a software copy that behaves as closely as possible to its real-world twin, capturing every single attribute of that physical thing. We are often focused on Digital Twin of a product – because as products evolve their Digital Twin can be updated to reflect the new product, it can also predate the new product. But what about the benefits of having a Digital Twin in discrete manufacturing, for assets? Consider a manufacturing plant, we can start with small pieces of equipment that are vital to the production – the more critical that equipment is, the more likely is it that a Digital Twin will deliver benefits. The component, of course, must be significant enough to warrant the (high) cost of developing a Digital Twin or have enough pre-existing models available to construct a first-generation Digital Twin. The key for executives is to understand that Digital Twins can bring immediate benefit to a manufacturing plant (and the products it produces), but they are a long-term play rather than a quick fix.
Not Just The Industrial Internet of Things (IIoT)
When considering Industrial Transformation programs, many companies start with asset performance management (APM) owing to broad data collection and advanced analytics in supply chain to improve maintenance and general asset performance. Digital Twins can go far beyond operational aspects such as APM. Rather than analyzing past performance only, the Digital Twin can also investigate the future and consider many what-if scenarios to determine how best to use an asset over time.
Digital Twins of production assets are often based on the design and implementation models created and refined during the development process. In discrete manufacturing these are developed on a product lifecycle management (PLM) platform that, traditionally, has been quite separate from IIoT and other business platforms.
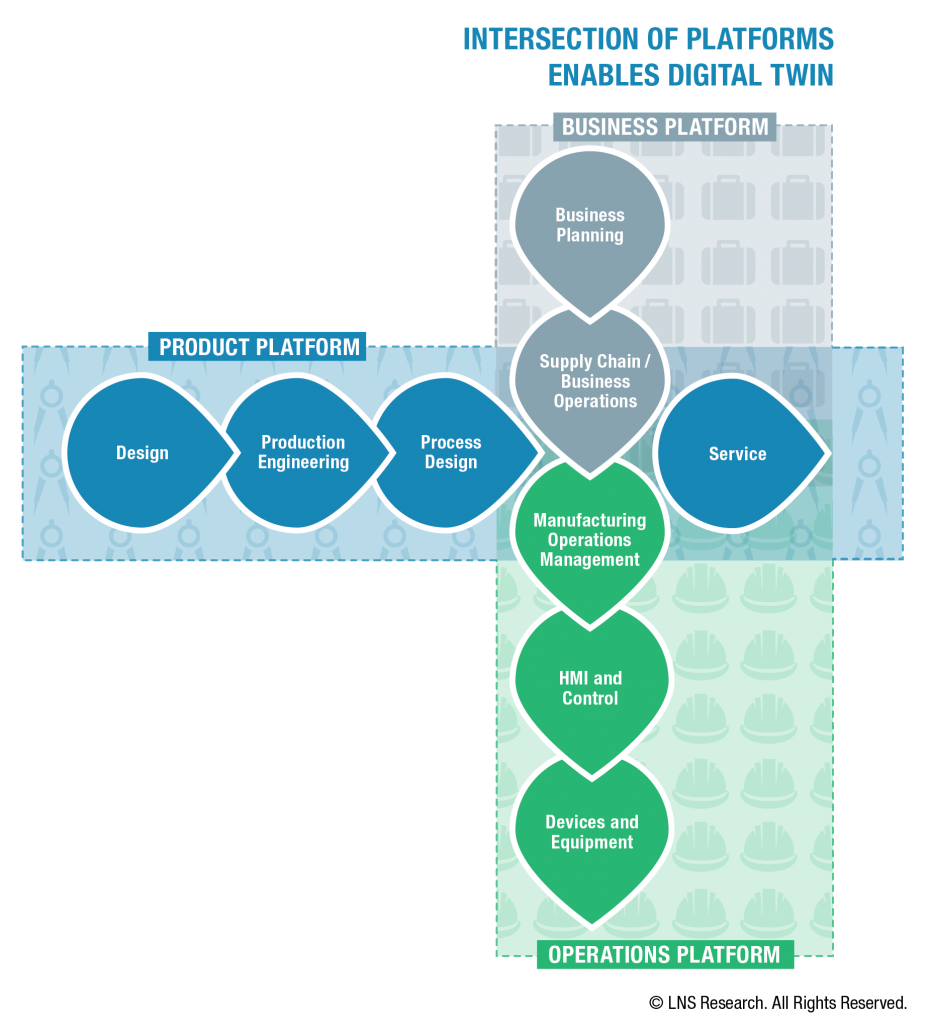
Modern PLM systems bring together product and process development, allowing interaction in the development process. As Digital Twin technology advances, we are starting to see the integration of these models into the manufacturing process itself. The future of manufacturing will see great benefits, especially as orders reduce to a size of one and design changes become daily events. Digital Twin can be used to study how product design changes can be applied in the plant and how plant changes could affect production (for better or worse). Simulation of products is already becoming mainstream as Cloud computing makes available enough resources to run complex simulations. As PLM, business and operations platforms are integrated, the potential benefits of Digital Twins across manufacturing will become achievable.
Bringing together all the data, applications and models needed to profit from Digital Twins is a long process. Many will start with IIoT platforms as they promise the data, communications, analytics, and applications that form the basis of Industrial Transformation. However, PLM, simulation and manufacturing process design are maturing technologies in discrete (especially complex discrete such as aerospace and defense) manufacturing. It makes considerable sense to start Digital Twin deployment from a PLM platform that already integrates design to production processes. Many discrete Digital Twin programs look specifically at the design of machines and products; most of the data and models required are in or can be supported by modern PLM platforms. As Digital Twin grows, an extension to the rest of the enterprise will be necessary.
Platform choice today for discrete Digital Twin development and management depends on the starting point. Manufacturers that use a mainstream PLM platform should look to their PLM provider to discuss how they can build a long-term Digital Twin strategy. However, users of PLM platforms do not necessarily use applications from that single vendor only – they might use PLM from one and CAD and simulation from others. Similarly, a vendor may not support third-party tools in his Digital Twin environment. At this early stage of Digital Twin deployment, incompatibilities like these can be expected.
The alternatives to Digital Twin on PLM include having an enterprise-wide business platform that supports IIoT technologies and a wide range of Digital Twin applications, or a pure IIoT player who would be more open, but this approach might take considerably longer to deliver real value.
While Digital Twin deployment is a long-term strategy, one of the benefits is that you can start small with single pieces of equipment or a critical part of a product and grow without losing the investment made. With its multiple benefits, we urge manufacturing company executives to explore the opportunities provided by Digital Twin technology and how it can drive the Industrial Transformation initiative.
Continue the conversation by joining our DELMIA Communities on 3DSwYm. Membership is free.