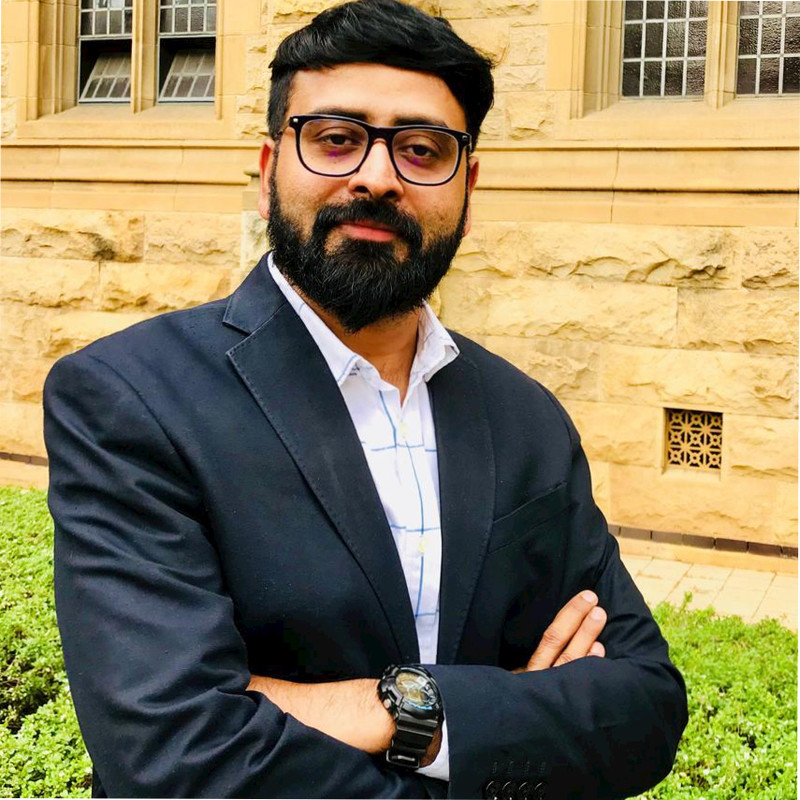
Dassault Systèmes is a member of Austmine, the leading industry body for the Australian Mining Equipment, Technology and Services (METS) sector, and a sponsor of the Austmine Conference 2019 held at the Brisbane Convention & Exhibition Centre. Themed “Mining Innovation – The Next Horizon”, the Austmine conference brought together leading mining innovation champions from the industry.
At Austime I recently engaged with senior executives from OZ Minerals, Debswana and Rio Tinto at a panel session, “What is the Future of Plant and Processing?” during the conference plenary. Facilitated by Brett Morgan, Director of Austmine, the session addressed the current challenges facing the mining industry and what these mean for plants being commissioned now and into the future. Here is the continuation of that discussion.
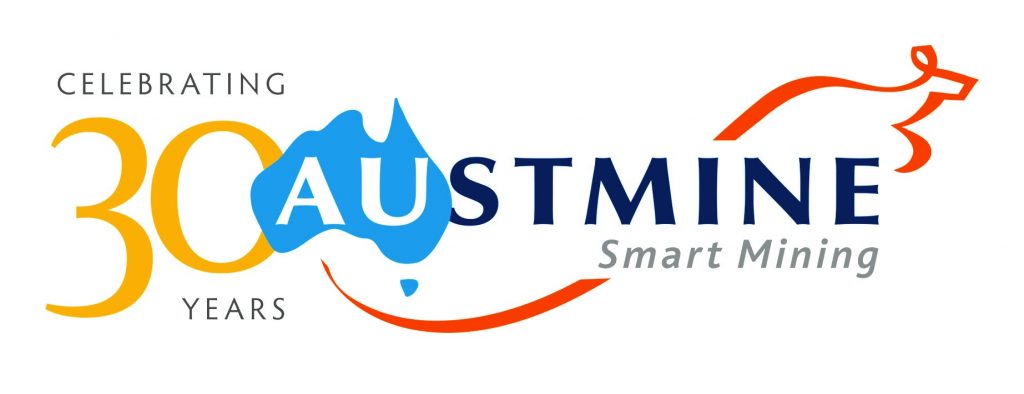
Part 2 of a 2-Part Panel Discussion Series
Q. What innovations in processing currently excite you the most and which technologies do you think have the most potential for positive impact?
A. The concept of the ‘smart factory’ excites me the most. The ‘smart factory’ can run largely autonomously through AI technology, robotics and data analytics, with the ability to self-correct thanks to the digital feedback loop. The ‘smart factory’ model connects the plant to other entities in the digital supply network, enabling more effective supply chain management. This model has huge potential in helping mining companies address the challenges of workplace health and safety, lean practices, ‘zero waste’ goals and sustainability. Other industries have already embarked on this journey and it is great to see companies in mining and oil & gas starting to deploy the ‘smart factory’ model.
Q. What skills do we need to deliver the processing plant of the future? How are you building your company’s internal skills?
A. Field workers will have to become more and more multi-skilled. They will not be assigned anymore to repetitive tasks, which will all be undertaken by cobots – collaborative robots. Plant operations will become more and more autonomous and machines will notify alerts when they will not be able to know how to behave when they will face new unexpected situations. Field workers will have to intervene only on-demand on asset management and will have to update the behavioural models in the plant processes.
Field workers will have the opportunity to receive training in the virtual environment through immersive reality technology, and will get access in context to any information that might be relevant for their tasks, thanks to augmented reality applications, such as consulting 3D views and work instructions on the same digital platform. The digital platform and experiential learning will be the workforce of the future enabler. We’ve been investing in technology development for last 3 decades – with the last decade focused on the 3DEXPERIENCE Platform for breaking down silos, connecting dots and democratising the technology.
Developing the “Internet of Experience” through the 3DEXPERIENCE platform, where plant operators can actually ‘experience’ virtually the varied scenarios of their plant performance in a 3DEXPERIENCE virtual twin through immersive and augmented reality, and base their decision-making on the insights from this virtual experience, is the key to build the plant of future.
Q. Which processing plant, anywhere in the world, do you see as demonstrating best practice? Why?
A. We have worked with a major Oil & Gas player who have been embarking on best practices in predictive maintenance and application of the 3DEXPERIENCE platform for virtual twin. What stands out is that they haven’t focused just on automation, but on developing a model-based enterprise and adopting best practices from lean manufacturing software, continuous worker enablement and the ‘digital worker’ concept from the ‘smart factory’ model.
Q. Every process plant operation is unique and therefore, one-size fits all technologies or procedures fail in reality. How do you work with partners to help them understand your challenges? Is co-innovating the answer to creating sustainable processing operations?
A. We work with partners through a tailored, systematic approach, which we call value engagement. It is about assessing a company’s value first. In order to optimise their business processes, ask the company what is their immediate need – is it optimising their production process, being able to produce more with less, reduce plant operators’ involvement in hazardous zones, and/or implementing effective cost controls? Conducting a value assessment with a company is key to justify their return on investment and meet their needs, and importantly, to identify a road map for their digitalisation strategy.
Get caught up with “The Future of Plant and Processing in Mining,” Part 1.
For more news and insights on Dassault Systèmes’ mining events in Australia, go to https://events.3ds.com/mining-australia