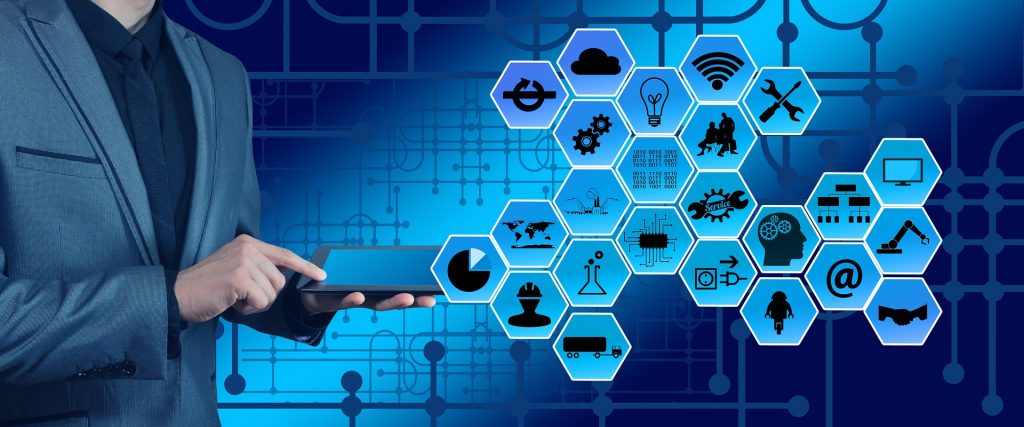
Much has been done to improve manufacturing efficiency. Supply chains have been optimized; warehouse inventory tracking has reached new levels of precision; production lines can operate with virtually no downtime. But, what about overall workforce productivity? As the common linchpin that brings together all manufacturing activities, has this metric improved along with all the investment in new technologies? If not, what can be done to address this shortcoming?
One of the themes I have observed with typical technology investments or systems upgrades has been a focus on ROI. This is usually measured by improved output (for the same cost), less downtime, or as a lower cost of quality. Most of the people you talk with will agree that there is an overall productivity improvement expectation when implementing a new solution, but it is often difficult to quantify. These benefits are often referred to as “soft,” given the somewhat subjective nature of measurement. As a result, this metric is often downplayed or not referenced in the discussion.
Digital Manufacturing as an Enabler of Workforce Productivity
As manufacturers continue to invest in automation and software simulation solutions, the need to integrate each of these disparate systems together increases. This is the power of the Industry 4.0 transformation now underway. If you can invest in a new warehouse tracking system that also helps to reduce quality issues without impacting output, then the benefits of such an investment will be far higher, driving greater profit to the bottom line. These benefits often go unrecognized.
Here is where digital manufacturing has really shown the power of taking a more holistic approach to operations management. By simulating how various system engagement occurs, such as how robots move across a factory or how track and trace intelligence could be better collected during the entire product life cycle, it is possible to break down the traditional silos of how performance improvement is measured. Digital manufacturing methodologies can not only drive performance improvement – but they can also usher in a new level of how performance is measured and assessed.
A critical component of how operations are managed – and how they must also be simulated – is the role workers play while performing the various tasks associated with maintaining operational excellence across the production environment. Today’s digital manufacturing and simulation programs now offer a whole new level of granularity than what was previously possible. Now it is much easier to map out workforce activities and movements, to then perform ergonomic and other efficiency reviews to ensure every employee is operating with the greatest efficiency while being subject to the least amount of strain or wasted activities.
Artificial Intelligence will soon play a greater role during this exercise. By offering the ability to predict future actions or engagement, we will be able to avoid future issues before they happen. The better manufacturers get at avoiding unplanned, wasteful activities and unnecessary friction across each of their systems, the greater output will improve. This compounding of performance improvement will allow workers to continue to improve efficiency and productivity – well after a new system or application has been implemented.
Validation by Case Study
CenterLine (Windsor), a Canadian industrial equipment manufacturer with a distinctive product that sells very well in the automotive aftermarket wheel market, offers a firsthand perspective of the potential to improve workforce productivity, based on the results achieved so far with their industrial transformation strategy.
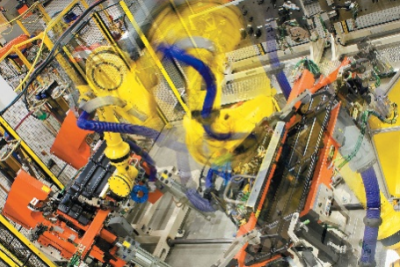
Luciano Mancini is the Robotics Simulation Lead at CenterLine (Windsor) Limited. As he explains, “DELMIA Robotics software helps us visualize and conceptualize our designs before they’re manufactured on the floor. That helps us resolve issues upfront and gets the product out right the first time … By building virtually, we demonstrate that we can produce their complicated systems on time and on budget, and exactly how it will improve their operations.”
The more activities can be digitally modeled first before being actually done in the physical world, the better an opportunity that manufacturers will have to perform the action right the first time. As digital manufacturing continues to be embraced and deployed on mass scale, look to see greater simulation of more activities, including how humans interact with their machine counterparts, in what could be an interesting game of “leap frog” whereby each action contributes to future responses in what could be a never ending continuous process improvement cycle.
Learn more about CenterLine at the the CenterLine Factory Showcase March 4, 2020. Visit the Center Ltd., plant in Windsor, Ontario, Canada for their Factory Showcase. Discover how they leverage DELMIA solutions on the Dassault Systèmes 3DEXPERIENCE® platform to simulate processes and factory operations to optimize robot movements, plant layouts and material flow. Register today! http://go.3ds.com/pk5