Although the fundamentals have been around for a while now, Digital Manufacturing has matured through this life cycle at a pace I have never seen before. Complete virtual validation of production processes is no longer a future goal. The solutions are available today. The question is no longer “if” I should participate, but “when” and how fast can we get it going? If this describes your scenario, then I would suggest you consider applying a Lean approach to your Digital Manufacturing strategy – you might be surprised at the results you can achieve!
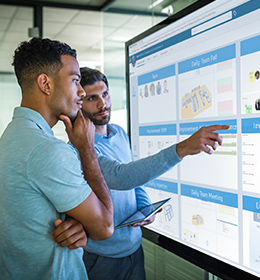
Avoiding Waste in the Digital World
Regardless the product or service you provide, waste is a bad thing. Perhaps in your personal digital world, the repercussions might not be so dire. It might be ok to take 100 pictures on your phone, even if you only want to save three. The rest can simply be deleted.
In a production environment where you are competing on a global stage, however, time and resources start to become more critical factors. It is a big deal to change over a production line – the last thing you want is to do it twice or perform multiple corrections.
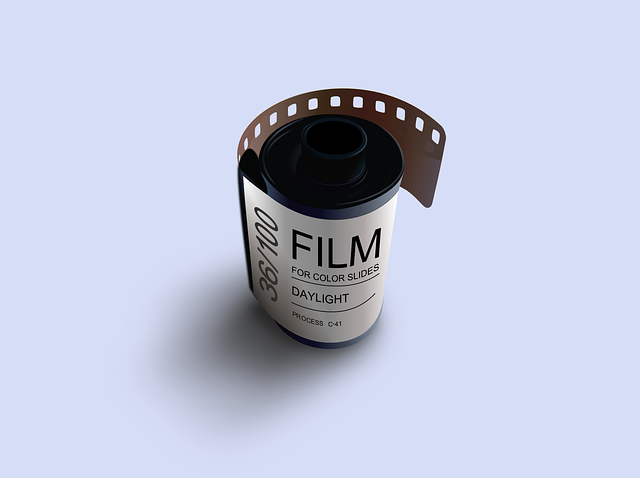
Continuing with my photo analogy, think of your physical production line being the equivalent of traditional film-based pictures.
Digital images are much easier to adjust, improve, and manage vs. the analog world where pictures are static, hard to change and tough to share. From this perspective, it is easy to see why digital manufacturing has been adopted at such a rapid pace.
Digital manufacturing has now become so widespread that it is no longer enough to just “do” digital manufacturing. You need to be highly refined and effective with the processes surrounding this strategy. If you can adapt a few weeks faster than a competitor in delivering a new product to market or implementing a cost savings program, you will reap big benefits from these actions. Going back to my earlier example, while it might just take 10 minutes to go through and delete 97 digital photos – that time could have been better spent doing another value-adding activity. Especially if you have to do this exercise 50 times.
If this kind of thinking sounds familiar, it should! Despite the origins of Lean manufacturing coming from way back in the “analog-era” 1970s as a result of efforts made by Kiichiro Toyoda, Taiichi Ohno, and others at Toyota, its concepts and founding philosophy of avoiding waste still hold true today. Now might be a good time to expand your Lean manufacturing software program to see how it might be applied as part of your digital manufacturing strategy.
The Results are In
The Boston Consulting Group conducted some interesting research to test the strategy of applying a Lean approach to a Digital Manufacturing strategy. They evaluated what performance improvement could be achieved and then summarized the findings in this article.
Here is a quick summary of their findings:
- When using either approach on its own—Lean or Digital Manufacturing—it can reduce costs by approximately 10-20%
- Companies using an integrated Lean AND Digital Manufacturing strategy can reduce costs by as much as 40%
- In addition, those choosing to use an integrated approach can reduce the costs associated with poor quality by 20% and work-in-process inventory by 30%
These are impressive findings and are consistent with the results I have observed firsthand. An example of how a Lean approach can be applied to a Digital Manufacturing strategy is the use of real-time data collection to modify engineering and product design. As production issues arise, this information can be incorporated with digital models to be integrated quickly in the next product cycle – instead of waiting for customer feedback or a reduction of sales to trigger a formal product review. The faster that data can be shared and acted upon, the greater potential to add further value to your digital manufacturing process.
While there is no way to know what new management or cost reduction strategy will be “new and improved” in the 2020s, one thing is certain – a Lean approach is likely to remain a concept that stays alive and well. Whether you are just getting started or well along your way with your Digital Transformation journey, it will pay off if you take time to remember your “analog” roots of Lean manufacturing and pay close attention to removing waste as part of your strategy.