Companies are paying more attention to supply chain risk these days, and that’s a very good thing because, according to a study by PwC and the Business Continuity Institute, 75% of companies experience at least one major supply chain disruption a year. Supply chain disruptions can be expensive, and not just for the cost of expediting replacement goods. Shutting down a production line can cost thousands of dollars per hour and the damage to customer service can be severe and long-lasting.
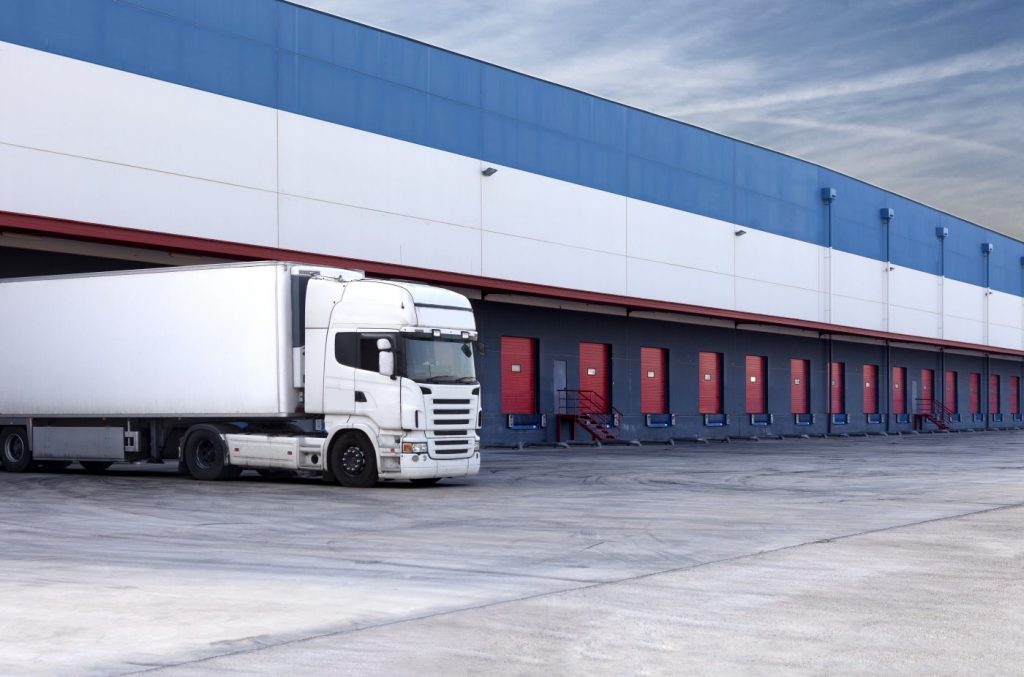
The art and science of supply chain risk management prescribes a formal process of identifying risks, estimating the impact of the disruption should it come to pass, and reckoning the probability of occurrence. Armed with this information, companies can map out the right strategy for avoiding the risk altogether, lessening the probability and/or impact, and devising strategies for recovery.
Typically, there are two kinds of risks to manage; let’s call them everyday risks and exceptional risks. The everyday risks are relatively easy to identify and manage – things like power outages, theft or damage to goods in transit, or the need to recall a defective or unsafe product. These kinds of disruptions fall into the everyday category because they occur frequently enough that probabilities can be statistically estimated with reasonable precision. Exceptional risks, sometimes called black swan events, are things that are not expected and cannot be predicted. Ordinarily, a company would not expect that a major supplier’s plant will explode, get washed away by a tsunami, or not be able to supply product due to political upheaval or an act of war. Managing exceptional risks takes imagination – thinking the unthinkable and estimating the unknowable. Nevertheless, it is a necessary part of supply chain risk management.
But there are challenges even in the management of everyday risks. Because there are typically many items to address, and many suppliers, transportation links, and service providers involved, a company has no choice but to do a kind of triage on the supply chain and devote more thought and more resources to the biggest risks, those with the biggest impact, the highest likelihood, and/or the hardest to prevent or recover from. The solution for the less significant items in the spectrum is often either tucking away some extra inventory just-in-case or just taking the risk and hoping for the best.
This is a logical, pragmatic strategy, but sometimes it can leave a company far more vulnerable that they realize. An article that appeared in the January 2014 issue of the Harvard Business Review, contained information from a study of Ford Motor Company’s supply chain that found the following: Disruption occurring at about 61% of the supplier sites would have no impact on Ford’s profits. However, about 2% of the supplier sites would, if disrupted, have a significant impact on Ford’s profits. Sounds like Ford should focus on that 2%, and not worry about the 61% that would have no impact, right? The biggest challenge would be to identify the suppliers in each group so appropriate remediation can be taken. To quote Shakespeare, ‘Aye, there’s the rub’.
According to the HBR article recap: “The supplier sites whose disruption would cause the greatest damage are those from which Ford’s annual purchases are relatively small—a finding that surprised Ford managers. Indeed, many of those suppliers had not previously been identified by the company’s risk managers as high-exposure suppliers.”
Supply chain risk management is an essential part of prudent business management. Many companies are aggressively pursuing risk management and benefiting from the reduction in disruptions, reduced severity, and quick recovery that results from their preparation. Risk identification, assessment, probability calculations, and planning remediation (avoidance, reduction, recovery) are not easy but they are vital. And, it turns out, there are some unexpected twists, as revealed in the HBR article, that could sabotage the best-laid plans.
This post originally appeared on Navigate the Future, the Dassault Systemes North America blog
Continue the conversation by joining our DELMIA Communities on SwYm. Membership is free.