The industrial equipment industry today is more complex than ever as we see growing technology trends such as automation, IoT, AI, machine learning and cloud computing brought about by the Fourth Industrial Revolution.
As such, there has been an increasing demand for customized industrial machines, automation, and new power sources including electric, hydrogen, and solar. This has resulted in manufacturers racing to innovate and produce smarter, autonomous equipment.
However, they also find themselves facing rising pressure to lower costs all while increasing delivery speed and quality. While it is not impossible to check all these boxes, it comes at an exorbitant price tag.
That’s why best-in-class manufacturers have started turning to digitalization, especially virtual builds, to not only overcome challenges, but to seize opportunities in the face of disruptions and emerge as a market leader.
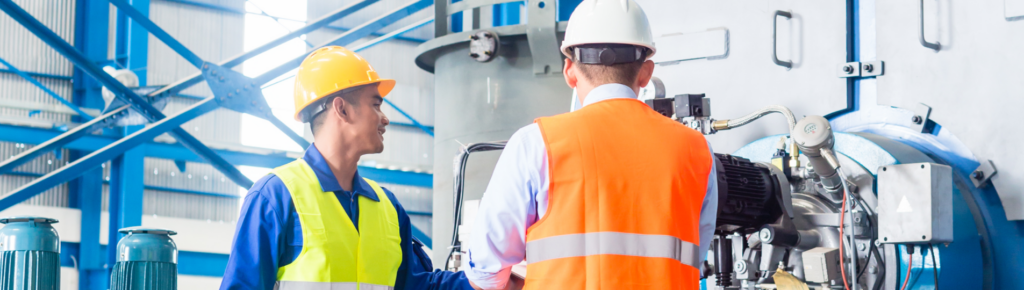
Tech-Clarity & DELMIA Manufacturing Engineering Survey
Together with Tech-Clarity, DELMIA surveyed 177 people directly involved with manufacturing engineering. It found that digital transformation drove higher manufacturing engineering and performance—translating into greater profitability.
Here are three key capabilities manufacturers gain when they leverage DELMIA as a solution to out-innovate competitors without sacrificing product cost and quality.
1. Enhance productivity gains
To drive profitability and productivity, inefficiencies need to be eliminated. This starts with non-value-added tasks. In fact, the survey respondents reported that up to 25% of manufacturing engineering time is spent on:
- Searching for data
- Re-keying information
- Recreating data
- Documenting feedback for others
- Modeling common assets
- Other activities that are not relevant to engineering innovation and decision making
With DELMIA, mundane and menial tasks are automated. This allows workers to focus on value-added tasks. In addition, the solution runs on a single digital platform, which connects all stakeholders.
All relevant information is collated on it, preventing discrepancies that can greatly impede progress or hamper quality checks. Stakeholders can easily collaborate as well as leave and receive feedback in real time on a single source of truth—driving optimized decisions.
2. Increasing cost-efficiency
One of the largest costs manufacturers face is building physical prototypes to validate manufacturability—especially in the industrial equipment industry. They are time-consuming and expensive to build and tweak during the optimization process.
Leveraging 3D and virtual simulations, manufacturers can create a digital replica of the product, known as the virtual twin. The virtual twin is built and updated with real-world and real-time data.
They can then run simulations to test how the product reacts to different stresses and conditions. DELMIA enables manufacturers to generate a greater number of “what if” scenarios that traditional testing methods would not be able to recreate due to physical limitations. With a more stringent and strict testing method, manufacturers are able to increase their chances of achieving first-time-right quality. This translates into minimized waste and shorter time to market.
3. Accelerated time to market
In such a competitive landscape, manufacturers know that the first to market will gain the biggest advantage.
However, speed must not come at the cost of quality as this can lead to product recalls and heavy fines.
Imagine gaining a complete view of the product and experience it being manufactured virtually first. This enables you to identify and rectify any problems before a single cent is spent on deploying physical resources.
That is the value DELMIA brings to the table with its virtual builds.
The survey also found that top performing companies are more likely to use 3D and/or simulation to validate manufacturing operations. They are also 33 percent less likely to run into manufacturing issues during production, which incurs a much higher cost to fix.
Other compelling business values of utilizing virtual builds in industrial equipment include:
- 37% fewer prototypes
- 35% less Engineering Change Orders
- 35% reduction in time to market