A manufacturer’s operations are constantly exposed to the risk of inconsistent supply. When it happens, supply chain managers can sometimes face a level of disruption that goes beyond the threshold of correction.
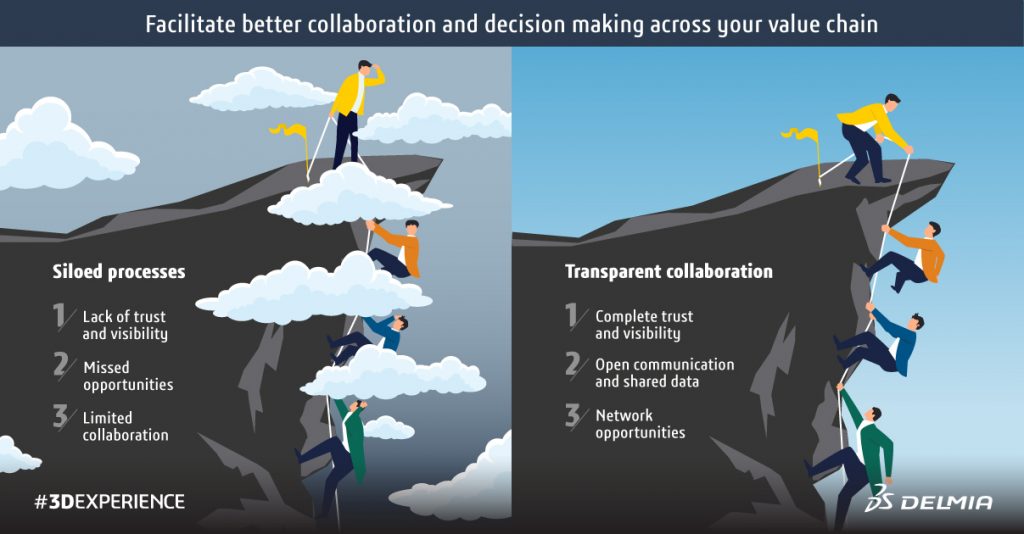
The COVID-19 outbreak was one such situation. However, major disruptions are not just sparked by global crises. Upheavals in one country can heavily impact manufacturers worldwide, too.
For example, the 2011 Tōhoku earthquake and tsunami significantly affected many industries, even those with production plants outside Japan. Manufacturers realized that they had no backup plans for the production of components critical to their operations.
Nine years later, many supply chains have still not realized the dream of connecting effectively with their partners to collaborate and make better decisions.
Strengthening value network
To avoid throttling or temporarily shutting down production plants in the event of a massive disruption, manufacturers need to strengthen relationships within their global sub-tier supplier networks. A well-managed manufacturer-supplier relationship will result in better quality and service, reduced risks and lower costs. To do this, manufacturers must have visibility of the structural risks and opportunities in their sub-tier networks, while monitoring supplier health and lead times.
Achieving this level of visibility requires communication and collaboration between the stakeholders on all levels. It is important to share forecasts, production schedules, inventory, transportation plans and other vital information. It is not just about having an overview. The ultimate goal is to make better overall decisions.
The key to managing fluctuating demand
Your suppliers have to deal with continuously changing forecasts. A low-order intake can cause them to drive down production schedules to avoid excess inventory and its associated costs. However, as suppliers reduce their capacities to stretch their order books over longer periods, this will cause an inverse effect on lead times. And worse, with your suppliers’ current systems, you likely can’t see the future effects of these decisions.
Another thing to consider is that many companies use demand forecasts that are based solely on historical data. But this only makes sense for products that behave consistently over time and in markets that remain stable, which is not the case for 2020.
Due to this year’s volatile global market and sociopolitical challenges, it’s better to use a range forecast instead of a single value forecast. Range forecasts,otherwise known as prediction intervals, are based on a range where the actual demand has some probability of occurring.
When dealing with fluctuating demand, a sophisticated forecasting solution can generate a number of scenarios as well as organize, review and analyze huge amounts data. It’s impossible to do all of this manually – and without it, your forecasts will be less accurate and effective.
Planning in uncertain times
Demand forecasting is not the only challenge this year. Production is being frequently rescheduled too.
To be resilient in these uncertain times, manufacturers need a solution that provides an integrated production plan covering multiple production resources and assembly lines within a manufacturing plant. The plan must also include all relevant planning knowledge, rules and assumptions.
Planning and decision-making in a complex environment cannot just depend on the planner’s estimates and past experiences nor on simple heuristics. The best decisions can only come from a powerful solution that calculates all eventualities and identifies potentials for additional value.
For one, an intelligent planning solution can create many different schedules that propagate and display the effects of changes, decisions and disruptions in real time across all production steps. It can also automatically check the availability of all resources such as materials, containers and staff with the appropriate skills.
Smart Planning Software
With this intelligent planning solution, manufacturers are empowered to:
- Simulate different planning scenarios while monitoring their impact on relevant KPIs
- Identify added value that can be measured via various KPIs, allowing the success of any adjustments and the resulting scenarios to be quantified
- Use these KPIs to manage planning decisions and optimization efforts, thereby influencing how the company performs in the future
- Allow real-time collaboration, which gives planners clear information on what suppliers can deliver on time
- Evaluate scenarios in real-time based on planning KPIs when a production plan is adjusted
- Show the effects of these scenarios propagated downstream as changes can now be displayed based on time dependency
The COVID-19 global crisis is not only a time for organizations to come together but also a call to reflect on their broader mission and purpose in the value network. In a time of great uncertainty, manufacturers and suppliers must integrate within the value network so that they can make better decisions that benefits their organizations and beyond.
Learn more about the challenges faced by manufacturers and how to solve them in our brochure, “Are Control Towers enough for a competitive edge?” Download it here.