Understanding the Journey
My first blog post of this manufacturing operational excellence series presented a few reasons why manufacturers have decided to pursue a strategy of improving their operational excellence. My second blog post discussed some of the tools available to accomplish this objective. This post suggests appropriate next steps to put your plan into action.
Business and manufacturing professionals are always looking for new ways for operations to support improvements to their company’s products, services, and bottom line. However, it’s also important to focus on optimizing limited human and capital resources to ensure operations can consistently perform with good results.
Whether coming from a large, global manufacturer or from a smaller, more regional organization, these are challenges on the top of nearly executives’ mind. What I have found in recent research and discussions with industry leaders is that these challenges can be effectively addressed by pursuing an operational excellence journey to elevate the performance of manufacturing operations. This strategy requires bold thinking, rapid reactions, and improvement actions, along with fully informed and engaged teams.
The 2013-2014 LNS Research Manufacturing Operations Management (MOM) software survey provided considerable new data and insights on how to navigate the complex landscape of operational excellence challenges in order to provide unprecedented new gains in productivity, quality, responsiveness, risk mitigation, and economic value generation.
Harnessing the Potential of People
It should come as no surprise, but harnessing the potential of people is one of the greatest assets that companies can leverage for an effective operational excellence journey. Market-leading companies have organized around cross-functional teams to support this journey. As a best practice, when it comes down to actually putting your plan into action, you will achieve the greatest success if you proactively align and harmonize the goals, objectives, and Key Performance Indicator (KPI) metrics of your staff and management team with your corporate objectives. And, as part of accomplishing this goal, you will need better and faster data analysis and real-time visibility to plant and enterprise information so as to best support your “human capital” to drive the right behaviors from teams and individuals.
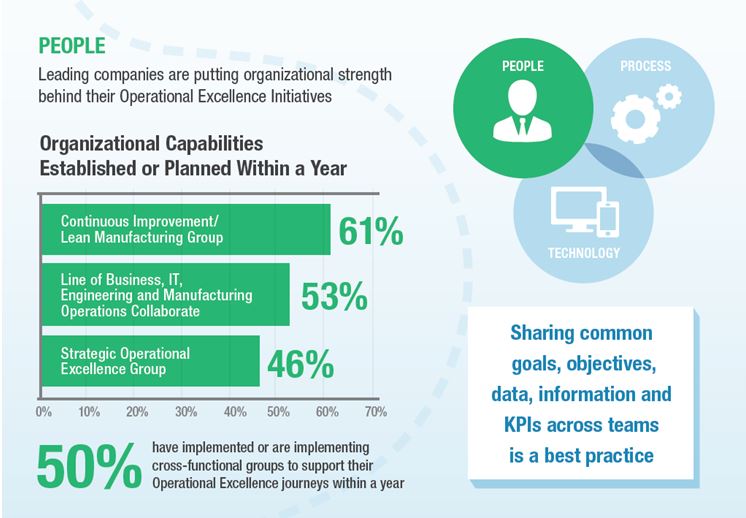
Process Improvement Programs
As continuous improvements are made along the road of an operational excellence journey, it’s important that these incremental improvements are sustainable by making them part of future processes and procedures. Without this capability, your journey to improved operational excellence will be cut short and never truly accomplish the desired objectives. In other words, if you can’t count on your improvements to stay in place, there is no way to evolve to new levels of operational performance. In order to accomplish this on a systematic basis, market leaders are accelerating their pace toward operational excellence through formal manufacturing programs and training.
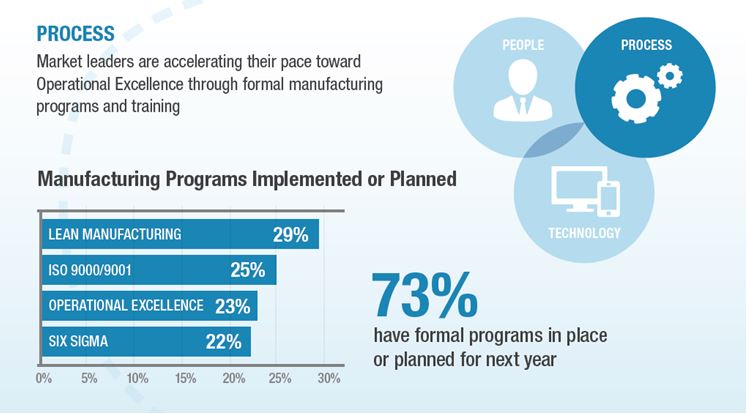
As we can see, 73% of companies have some type of formal manufacturing improvement program already in place.
The top programs planned or in place are Lean Manufacturing software at 29%, ISO 9000/9001 at 25%, holistic Operational Excellence at 23%, and Six Sigma at 22%. All of these programs offer structured methodologies, training, certification, and they support company-wide engagement and collaboration. A great place to start your operational excellence journey is to begin using these methodologies in conjunction with a small subset of processes that are most in need of improvement.
Accelerating Success with Supporting Technology
It makes no sense to implement technology without first understanding the supporting role of technology to support the people and process aspects described earlier. However, it is undeniable that technology can play a pivotal role in helping companies accelerate and sustain their operational excellence position.
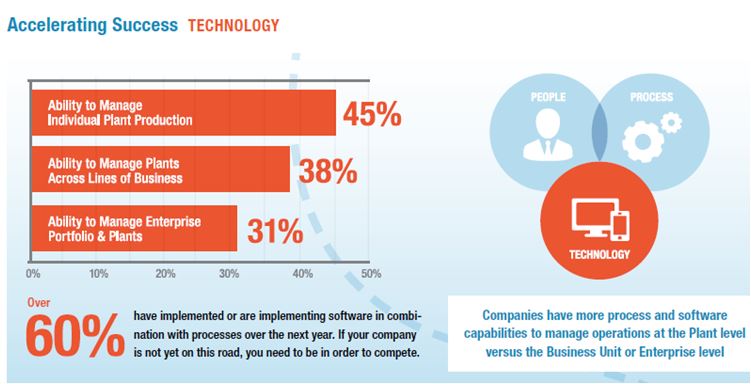
Most companies are accelerating their initiatives by institutionalizing best practice processes into software. In fact, over 60% have already implemented or are planning to implement processes supported by software technology. When we look at the process and software capabilities that are either in place or planned across a broad set of industries, we can see that there are more companies that have the ability to manage single plants with both processes and software (45%) than at the line of business (38%) or enterprise level (31%).
Conclusion
This Manufacturing Transformation blog series has taken a close look at why manufacturers might take an operational excellence journey – a strategy that might take years to implement, execute and master. While the time and resources might be significant, the rewards can be equally substantial. By deploying the right tools and incentivize the right people to do the right actions, the right rewards can be achieved – possibly making the difference between your being a market leader or a laggard. In the end, you have to make a choice as to what type of organization you want to lead and be part of. If your goal is to be the leader, then now might be the time to get your hiking boots out, because you have an exciting, rewarding and often challenging hike ahead of you!