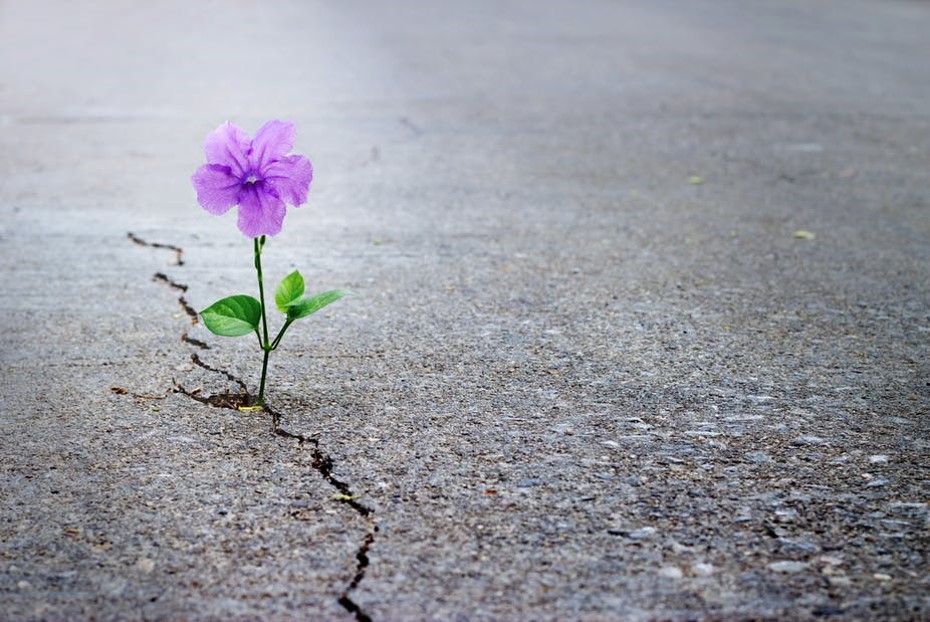
In the face of the COVID-19 crisis, production and industrial planning processes have become subject to a level of stress unprecedented in recent history. Many manufacturers depend on impacted networks for their supplies and the strain on planning organizations is jeopardizing business continuity.
What are some of the ways that manufacturers might improve their resilience, to address the crisis today and also to prepare for the recovery and the future?
Short-term Production planning software has always been about trying to make the “best” decision to meet demand given the constraints behind material, capacity and resources. Business continuity now has added challenges from today’s crisis.
Challenge 1: Production capacity is now subject to workforce absences and social distancing requirements that impacts throughput.
Challenge 2: Management now has to focus on balancing workforce capacity with costs and whether furloughing or downsizing today could impact the ability to rebound later.
Challenge 3: Visibility is now worse because suppliers have either been overloaded with demand or have supply/production problems of their own.
Challenge 4: Customer demand has become extremely volatile as demand for supplies and products changes dramatically through the lifecycle of the crisis.
This volatility is impacting different industries in different ways. Pharmaceutical and medical device suppliers are seeing surges in demand while aerospace and transportation industries have seen drastic reductions in production. In all cases though, manufacturers are asking how to optimize production now during the crisis, how they need to plan for recovery, and how they can prepare for future disruptions.
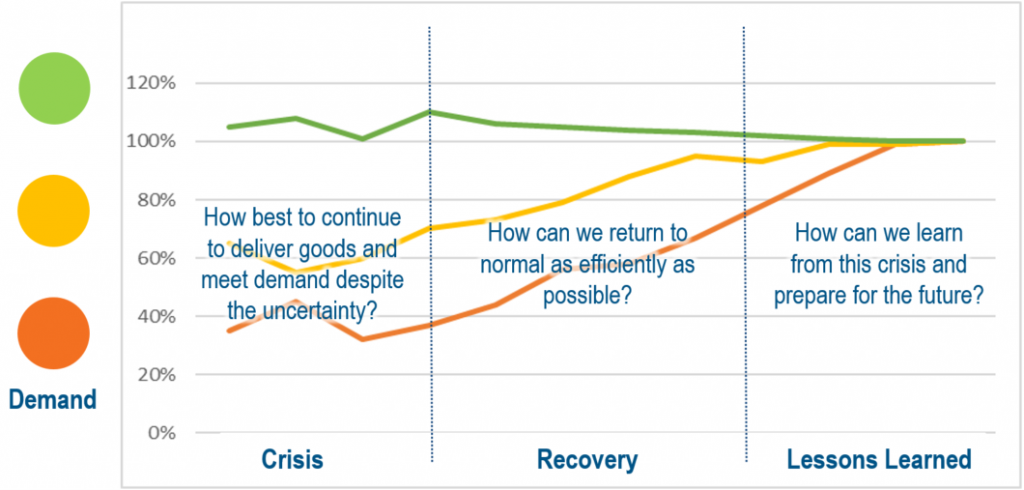
The majority of organizations are still behind the curve in terms of tools and processes with many using spreadsheets or other manual and homegrown solutions. These static tools have a high risk of error and don’t provide effective decision support, let alone true optimization to make the “best” decision to address the questions being asked.
At DELMIA, we’re proud to have been recognized by analysts as being an industry leader at solving some of the world’s most complex optimization challenges in planning and scheduling. As part of that leadership, our DELMIA Ortems solution provides the power of constraint-based, finite-capacity resource optimization, and synchronization of production flows. This enables rapid decision support in an integrated and automated environment that allows planning and scheduling to get answers to important challenges:
- How to compare line closure scenarios if there is low demand?
- How to react optimally to unplanned events such as lack of staff or supply shortages?
- How to plan increasing line capacity as society starts to re-open?
Being able to answer these questions provides significant benefit in terms of both revenue (improving agility to meet customer service levels and due dates) and costs (reducing inventory and production costs). More importantly it provides manufacturers with a business continuity plan that benefits the workforce and the recipients of potentially essential products.
Unfortunately, this crisis is probably not the last that we will experience. Given our global, interconnected business world, it’s time for manufacturers to take a positive step towards solving today’s challenges and also preparing for the future.
If you would like to learn more about our rapid solutions for planning and scheduling during disruption, you can email us at DELMIA.covid19@3DS.com for an evaluation of how we can help.