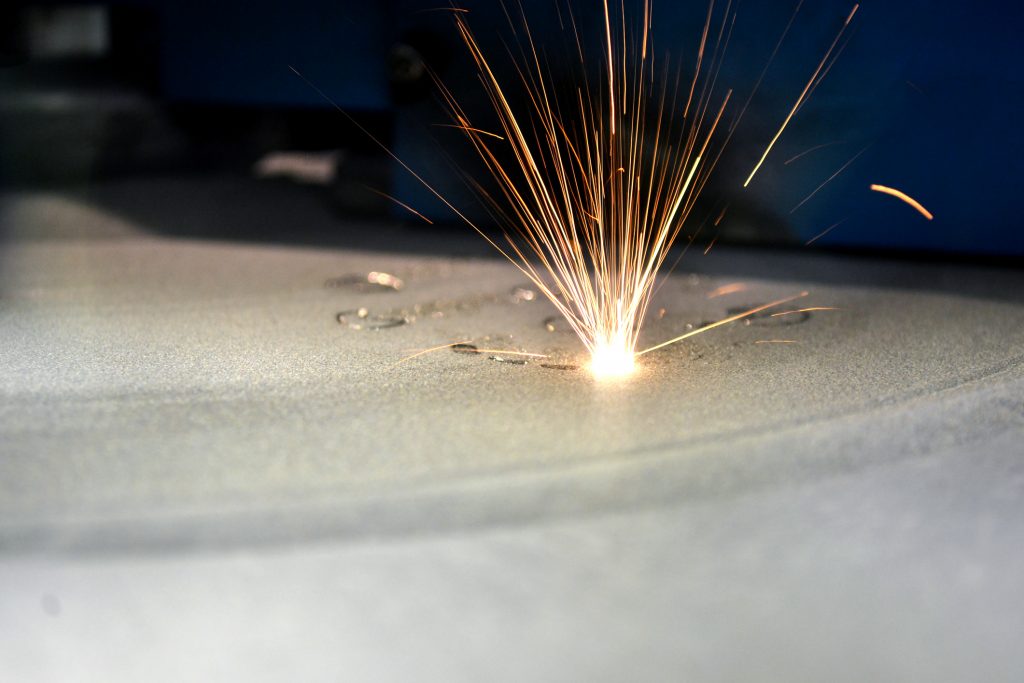
Leveraging their 3DEXPERIENCE® platform, Dassault Systèmes has been developing a set of dedicated applications for Powder Bed additive manufacturing software processes, from design to build job preparation and simulation. To ensure a continuous digital thread all along the process, it was mandatory to have a connection with Powder Bed printers as well. Dassault Systèmes has made this connection with machines from EOS, the leading technology supplier in the field of industrial 3D printing of metals and polymers.
With the seamless integration of the open EOSPRINT SDK, users of DELMIA Powder Bed Fabrication and SIMULIA Additive Manufacturing Scenario can now use native CAD data coming from CATIA or SOLIDWORKS to prepare the job, directly create a job file, and run a print simulation to analyze residual stress and potential distortion for EOS machines.
Users of the 3DEXPERIENCE platform can now connect to an EOS community hosted by Dassault Systèmes in which they can retrieve the Virtual Twin Experience of EOS machines configured to connect to EOS open software interfaces (APIs).
Customers can assign their exposure sets to each CAD geometry of parts and supports on the build tray based on the EOS material sets, which come with the integrated EOSPRINT SDK. Once this is done, the Powder Bed Fabrication app connects to the physical EOS 3D printer to calculate the scan vectors of the job file.
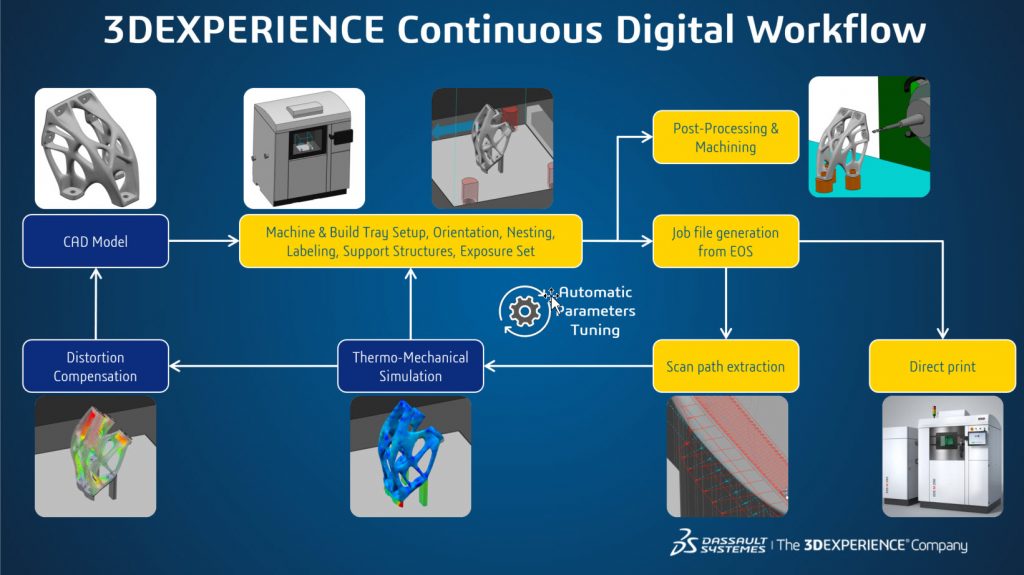
Users can then choose to directly send the job for printing and/or store the job file for later use. Extracting the scan vectors with assigned laser parameters declared in the exposure sets, the Additive Manufacturing Scenario app performs a thermo-mechanical simulation of the build, predicting with the finest accuracy any potential defect or distortion on the parts. By using the Virtual to Real shape application, they can compensate the potential distortion on the initial CAD and ask for a new job file creation without having to start the build job preparation and simulation from scratch. This deep integration into the 3DEXPERIENCE platform was made possible by the open interface called EOSPRINT Software Development Kit (SDK), which can be used by every EOS Software partner and customer.
Martin Steuer, Senior Vice President Division Software at EOS states: “Integrating the EOS 3D printing technology into the powerful 3DEXPERIENCE platform provides a seamless workflow to our mutual customers to increase the efficiency and reliability of their additive manufacturing software. As Dassault Systèmes plays an important role in the industry, we are happy that our investment in open interfaces is perceived so well by Dassault Systèmes and that we now have an integrated solution as a result of this collaboration.”
All these capabilities are already available today with the on-premise and cloud version of the 3DEXPERIENCE platform. The list of compatible EOS 3D printers can be found on the EOS Community.