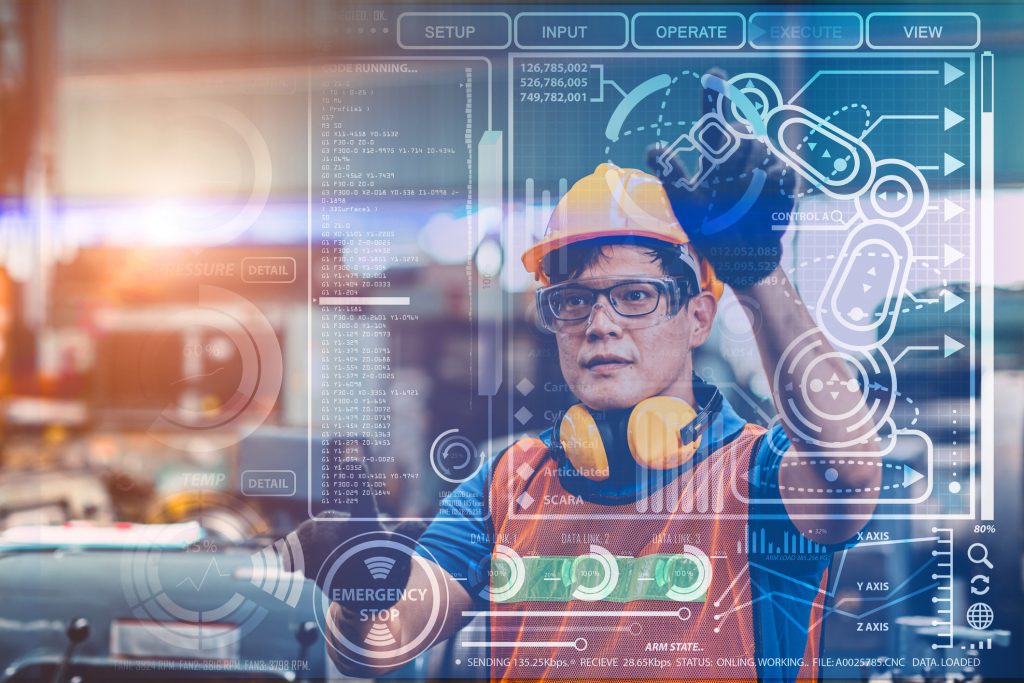
This blog features excerpts from the Manufacturing Leadership Journal’s article, “Leveraging Digital Twins to Accelerate the Journey to Factory of the Future.“
When the pandemic disrupted the operations of manufacturing companies and their supply chains, many organizations were forced to reexamine their strategies. For example, on how to secure business continuity.
To adapt to the “next normal” in the current economic environment, analysts believe that companies need to work toward:
- Re-skilling and prioritizing the safety of the workforce
- Relying more on workforce automation
- Building resiliency into supply chains
- Improving manufacturing agility and flexibility
These make up the Factory of the Future. Powered by highly automated, interconnected manufacturing tools, these advanced systems leverage sensors and data in a closed-loop system. This enables machines to self-regulate and optimize what’s being manufactured with the most efficient use of resources, time and effort.
Manufacturers can benefit immensely from the Factory of the Future. More efficient use of the workforce and assets enables companies to produce more with the same amount of resources in a shorter time. It also facilitates a greater capacity for innovation, enabling the development of new products within shorter cycles. However, achieving this ideal is not without major challenges.
The sheer mass of IoT data generated within an enterprise and the complex rules needed to organize that data alone requires a unified digital architecture. However, automated machines and devices currently in use tend to have different dialects, making it difficult to implement seamless universal communication between machines. This universal digital protocol is a key ingredient of the Factory of the Future, along with automated systems and human capital with the skills necessary to operate these systems.
This transformation may seem like a monumental task, but it can be made possible with the latest developments in digital twin technology. The latest evolution of this technology, the virtual twin acts as a real-time virtual representation of products, processes and systems to help enterprises model and optimize real-world operations and drive continuous improvement in performance and results. The depth of data insights provided through the virtual digital twin supports decision-making that allows manufacturers to keep global operations running smoothly, efficiently and sustainably while maximizing profit.
Discover more about the role that digital twins play in helping manufacturers achieve the Factory of the Future. Read the full article in the Manufacturing Leadership Journal to learn more.