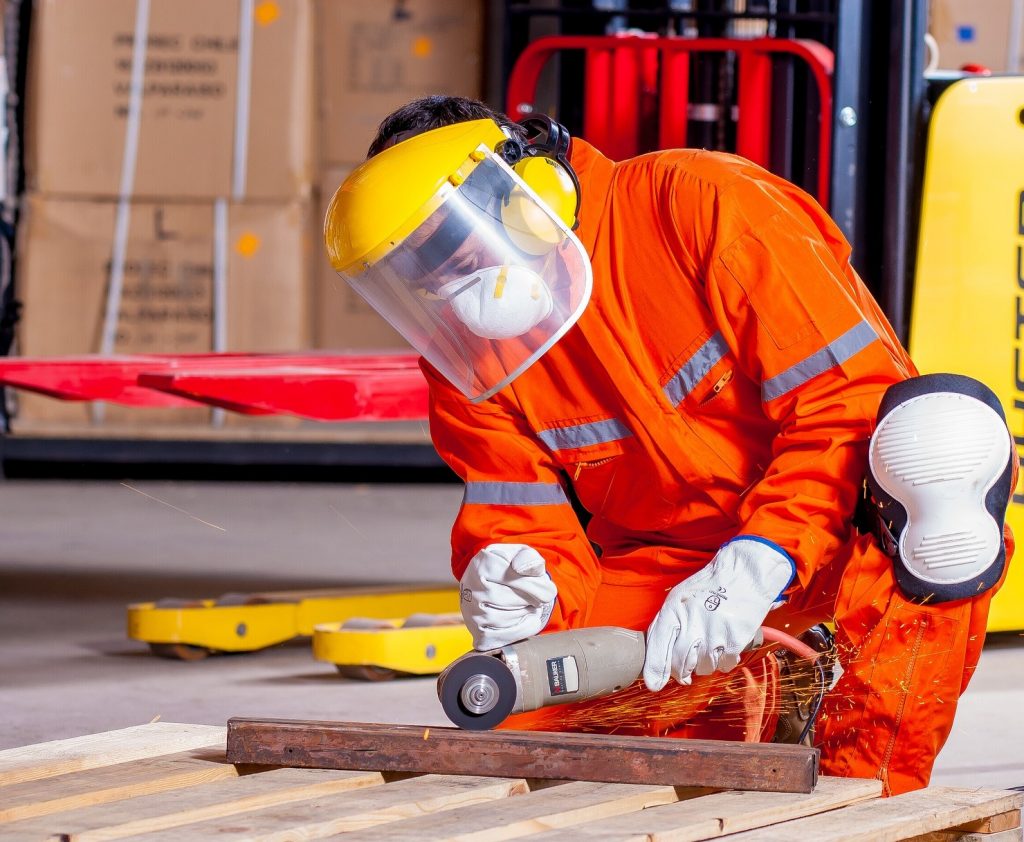
Cutting tools is a part of everyday life in metal fabrication facilities and machine shops. It’s impossible to do your job without them, but they do create a risk. Hand injuries are a common occurrence in the workplace, and they require employees to take time to recover. How can you keep your workers safe while they’re using cutting tools?
1. Consider Employee Age
While it is illegal to discriminate against someone based on their age, be mindful of your employees’ ages if they’re handing cutting tools in the workspace. While workers under the age of 25 tend to report fewer overall injuries, they have the highest percentage of lacerations. The number of average laceration injuries lowers substantially with each age group.
There is no definitive reason for this change, though it could be due to to the fact that employees gain more experience as they age, learning how to avoid injuries on the job.
If you have a swath of young employees, make sure they are well trained and monitored to avoid cutting tool injuries. Perhaps you can pair them with an older employee who can serve as a mentor and show them the ropes.
2. Recognize All Hazards
Take the time to analyze your workplace and recognize all the hazards you or your employees might experience. Figure out who is the most likely to get hurt and how they end up getting injured. If you run a fabrication floor or machine shop, cutting tools are one of the significant hazards you’ll need to address.
Once you have a better idea of where injuries might occur, it becomes easier to figure out how to prevent them.
3. Training Should be Continuous
Safety training isn’t just something that should take place during onboarding. It should be continuous, allowing you to keep safety in the forefront of everyone’s mind regardless of how long they’ve been with the company or in their current position.
With cutting tools, it is essential to choose the correct cutter for the job to prevent injuries. Educate your employees on the Rockwell hardness scale. Every material is assigned a rating on this scale, based on how resistant it is to cutting. Trying to cut an item with something higher on the Rockwell hardness scale will result in equipment damage and potential injuries as well.
4. Maintain Personal Protective Equpment
As an employer, it’s your responsibility to offer personal protective equipment, or PPE, to your employees. You also need to ensure that this equipment is properly maintained or replaced if it becomes damaged or worn out. For cutting tools, this might include but isn’t limited to:
- Eye protection
- Face protection
- Gloves/arm protection
- Masks to protect against the intense light generated by welders/plasma cutters
- Protection from any chemicals used on the job
While maintaining PPE for your employees won’t prevent all injuries, it can help to reduce their occurrence dramatically.
5. Create a Safety Culture
Just like training, safety policies shouldn’t just be words on a piece of paper or a computer screen to be read once for a test and then forgotten. Safety should be at the forefront of everyone’s mind, and should also be everyone’s responsibility. Take the time to create a safety culture. Everyone has a job that contributes to keeping the workplace safe, and the system holds everyone accountable for their actions.
Don’t let safety become something that gets taught once. If you want to keep your employees safe during their workday, make safety your priority.
Staying Safe on the Job
Metal fabrication and cutting tools are inherently dangerous, but that doesn’t mean they need to result in an injury. Make sure you’re providing proper PPE for all your employees, and refresh their safety training regularly. Safety should be everyone’s responsibility, from the highest-paid CEO to the newest employee on the fabrication floor. You can cut corners everywhere else — don’t do it where safety is concerned.
As an employer, you are the first line of defense when it comes to workplace safety — but you can’t do it alone. Create a culture that is focused on workplace safety, and everything else will fall into place.
Continue the conversation in our DELMIA SwYm Communities: https://www.3ds.com/products-services/delmia/communities/