This blog was originally published in May of 2021.
Provide Airflow to Multiple Patients from a Single Ventilator
The COVID-19 pandemic has completely changed human lifestyle and health care in the course of the year 2020 and also in 2021. It has created an unparalleled demand on the health care industry for quick and innovative solutions to ensure the safety of patients and health care workers. The healthcare industry has worked tirelessly to provide healthcare at an unprecedented level, benefiting from innovation enabled by modeling, simulation and advanced manufacturing. The industry will continue to benefit in 2021 and beyond.
As the COVID-19 pandemic spread in early 2020, concerns grew about lack of ventilators to support ICU patients. As the number of patients grew, many healthcare facilities witnessed a massive shortage of ventilator machines needed to treat critically ill patients. Many efforts and innovative solutions by various industry members across the globe were carried out to deal with the possible shortage of ventilators upon sudden surges of patients. Efforts continue into 2021 and beyond.
Significance of the Flow Splitter
To help hospitals maximize ventilator support, we have seen instances of hospitals utilizing novel flow splitters installed on ventilators to help more patients by splitting the airway path. The basic principle of a ventilator flow splitter is to connect two or more patients to one ventilator system. A flow splitter splits the incoming air from the ventilator system into multiple air passages to cater to the respective needs of the patients.
A proper and robust design plays an important role in the functioning of the flow splitter to withstand all the possible real world scenarios. The design must adhere to several design criteria and constraints including, but not limited to:
- Ensure an adequate amount of air reaches each patient, by minimizing the pressure drop in the splitter.
- Ensure that there is no obstruction of air flow and that consistent and continuous flow is maintained within the splitter.
- Ensure that the structural design of the splitter can withstand various possible mechanical real events such as pull, drop, twist, etc.
This leads to a few questions:
- How can designers build a product quickly and reliably?
- How can designers realize a design that meets competing design objectives?
- How can a designer bring a product to market with confidence while minimizing the development cost?
Flow Splitter Optimization Using the 3DEXPERIENCE Platform
In this hour of need, engineers from Dassault Systèmes set forth to demonstrate how a flow splitter could be optimized using tools on the 3DEXPERIENCE platform. The 3DEXPERIENCE platform leverages seamless transition from modeling to simulation and equally seamless transition between different simulation disciplines. The 3DEXPERIENCE platform also provides a world-class collaborative environment to track modeling and design changes across multi-functional and global design teams. Using the 3DEXPERIENCE platform with its combination of design-simulation associativity and automated meshing capabilities, we are able to shorten the time to market and reduce development costs.
Using the 3DEXPERIENCE platform, one can design and build a complete model proceeding from the initial system requirements phase all the way to the manufacturing phase, all under one framework as shown in Figure 1.
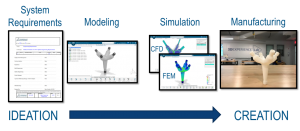
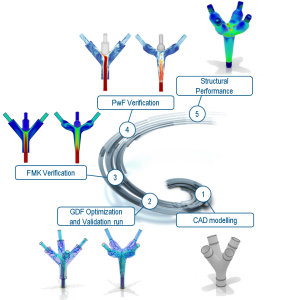
For this study, the following steps have been executed as outlined in Figure 2:
Baseline Design Using CATIA
Starting from system level technical specifications based on WHO recommendations (World Health Organization. (2020). Technical specifications for invasive and non-invasive ventilators for COVID-19: Interim guidance, 15 April 2020. World Health Organization. https://apps.who.int/iris/handle/10665/331792. License: CC BY-NC-SA 3.0 IGO) a geometry model was constructed as a starting point for the flow splitter. An initial baseline design was modeled using the CATIA applications with the desired specifications and dimensions.
Fluid Optimization
An intuitive flow splitter design was analyzed with steady-state CFD, after which the design was further optimized with flow-based topological optimization design tools to minimize pressure drop. Seamless integration between CFD analysis and topology optimization helps to obtain an optimized design in a straightforward workflow, which is not possible with traditional techniques.
Fluid Performance Verification
A steady-state CFD simulation was executed on the optimized topology to confirm results and product performance. In order to gain confidence in the generative steady-state CFD based design, additional highly accurate Lattice Boltzmann VLES CFD simulations were executed to confirm the performance improvement of the realized shape/design.
Structural Performance Analysis
The 3DEXPERIENCE platform enables multi-physics, multi-scale simulations with direct CAD associativity. This provides a seamless migration from fluids analysis and design to structural analysis and design. Once the flow path geometry was designed with CFD, a thickness was prescribed for the flow splitter structure and an FEM model was constructed and evaluated to ensure the wall thickened CFD designed flow path met structural requirements. A series of FEM simulations evaluating the structural performance of the 4-way flow splitter under push, pull and twist loadings were performed. Once both the CFD and FEM analyses met the requirements set forth in the technical specification document, the design was sent to a 3D printer for manufacturing.
Results
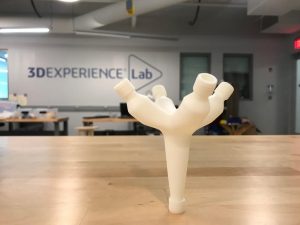
Based on the technical specifications, a parametrized model was created using the CATIA part design application. The easy to use interface with parametric capability helps us to build a model and change dimensions quickly based on our needs.
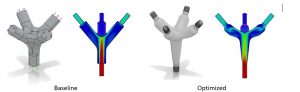
The fluid optimization study helped us to generate a new robust design by reducing the recirculation zones and minimizing the pressure drop. Figure 4 shows the velocity magnitude slice plot of the flow splitter. The new design reduced the pressure drop by 70% compared to the baseline design while ensuring a consistent and continuous flow within the splitter.
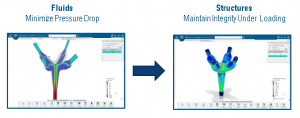
The optimized design was then evaluated for structural performance under various real life scenarios like pull, drop, twist, etc. as shown in Figure 5. A series of FEM simulations with appropriate boundary conditions were executed. The seamless migration from the fluid to structural scenario in the 3DEXPERIENCE platform helped us to determine if the product meets the requirements from both fluids and structures aspects. Once it was demonstrated that both the CFD and FEM analyses met the requirements, the design was printed using the 3D printer.
Conclusions:
- The 3DEXPERIENCE platform provides a complete end-to-end solution right from ideation to creation including the design phase and validation.
- The Integrated Modeling & Simulation approach on the 3DEXPERIENCE platform along with data associativity and topology optimization helped us develop a product in a smooth and straightforward way. Topology optimization helped us to quickly and seamlessly generate the CAD design from a human design while ensuring minimal pressure drop.
- Seamless migration from fluids analysis to structural analysis helped us to test the product and predict its behavior in various real life scenarios.
- The approach reduced the time to market and development cost associated with it.
The flow splitter optimization is only one example of the power that is brought to the Life Sciences industry by Integrated Modeling and Simulation. Ideation to creation can be realized with the power of the 3DEXPERIENCE platform, helping us to fulfill our mission of harmonizing Product, Nature and Life.
Learn more about our 3DEXPERIENCE simulation portfolio by visiting https://www.3ds.com/products-services/simulia/products/3dexperience/
In a webinar taking place on July 14, attendees will learn more about this study as well as details on how parametric design was involved. Parameterization and automation are valuable to save time, conduct sensitivity studies and evaluate the influence of certain parameters. Drawbacks, however, include the fact that the outcome depends on the input design space and would likely give few percent of improvement on fluid performance. Generative design, in contrast, is more direct, more disruptive, and enables a shorter turnaround time for a designer to obtain an optimize flow path. Learn more and register for the webinar, which will also be available on-demand after the live event, here.
SIMULIA offers an advanced simulation product portfolio, including Abaqus, Isight, fe-safe, Tosca, Simpoe-Mold, SIMPACK, CST Studio Suite, XFlow, PowerFLOW and more. The SIMULIA Community is the place to find the latest resources for SIMULIA software and to collaborate with other users. The key that unlocks the door of innovative thinking and knowledge building, the SIMULIA Community provides you with the tools you need to expand your knowledge, whenever and wherever.