Door assembly design is a complicated process with multiple challenges. The 3DEXPERIENCE platform helps to overcome these challenges with a solution that is digital, connected, model-based, and end-to-end.
We asked Preeti Verma, Solution Consultant with SIMULIA who developed this workflow, to provide answers to some common questions.
Q. Why does this workflow need to be analyzed?
A. One of the top priorities in the industry, profitability, is proportional to shorter time to market, while maintaining high quality and performance. There are key industry challenges to be addressed in the automobile industry for creating profitable products using design and simulation software. Today the industry employs several different software products and tools to design components, verify the design using simulation and, validate the simulation results against test/legacy data. Target requirements for the design, simulation and test phases are usually managed manually and may not be traceable. The design and simulation divisions use different tools, use different design languages and this hinders collaboration. The current process works well but it is the best version of what can be done, leaving little room for improvement. The reason is simple, the tools are not integrated – it is a file-based information exchange system.
Furthermore, limited parametric studies in the preliminary design phase leads to a sub-optimal initial design. With design revisions coming in too late, the process may become too costly.
These challenges can be overcome with a solution that is digital, connected, model-based, and end-to-end on the 3DEXPERIENCE platform.
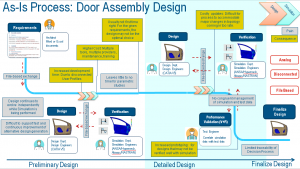
Q. Describe the workflow.
A. This particular example is applicable to the Transportation and Mobility (T&M) industry, but it can be extended to any industry by adopting the 3DEXPERIENCE solution. Based on a T&M example of a performance driven door assembly optimization workflow to meet multi-domain requirements of stiffness and vibration, the workflow covers preliminary design to detailed design phases of the product development cycle.
- Performance requirement management.
- Preliminary design
- initial verification using Simulation Vertical Applications. Vertical Applications (VA) are wizard based applications created for a specific workflow that make complex analyses easy for design engineers helping to drive their product design VAs have a simplified, top-down sequential, user guided setup ideal for any scenario that has been standardized within an organization. They are XML based facilitating straightforward construction.
- Preliminary design exploration leveraging design of experiments (DOE) using SIMULIA best practices. Democratized templates with configured interface help engineers to run parametric optimization with ease.
- Design space optimization using response surface methodology (RSM) and results data analytics.
- Detailed design and verification using simulation.
- And, test data validation and management to arrive at the optimal design.
This is a complete end-to-end solution on the 3DEXPERIENCE platform using integrated SIMULIA, CATIA and ENOVIA technology.
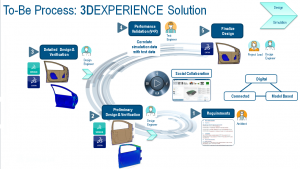
Q. What were the advantages (benefits) of using simulation?
A. With a focus on democratization, the content shows how we bring this advanced technology to design engineers to size design propositions and compare the alternatives for faster decisions, to detect flaws early and most importantly, find the best possible design for a given set of target requirements.
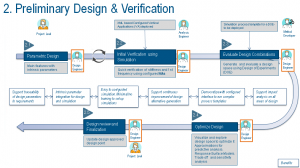